What is Wrench Time?
Wrench time is defined as the actual amount of time a craftsperson spends doing value-added work. A wrench time study, or work sampling study, is aimed at identifying and eliminating or mitigating the time spent on nonvalue-added tasks.
Wrench time does not include:
- Obtaining parts
- Looking for tools and instructions
- Travel associated with obtaining parts and tools
- Traveling to or from jobs
- Time spent obtaining work assignments
Wrench Time Facts
Fact #1: World-class wrench time is 55-65%; most companies have a wrench time between 18-30%.
Fact #2: It is not uncommon for the effectiveness of planned and scheduled jobs to be 25% or more than the same job without planning and scheduling (P&S). To see just how critical maintenance effectiveness is, consider the following:
Fact #3: The term “wrench time” refers to a unit of measure for the time maintenance personnel spend doing the actual work for which they are responsible for. It does not include the time a technician spends:
- Looking for parts
- Looking for their supervisor
- Waiting on production
Fact #4: Wrench time is usually expressed as a percentage, and national studies typically put this number between 25-50% for North American Industries.
- As an example, the time a maintenance mechanic takes to replace a mechanical seal and do a laser alignment on a pump would count as wrench time. However, the time spent leaving the job to get the seal from the storeroom, and the time spent away from the job site to obtain additional shims for aligning the pump, would not count as wrench time.
Fact #5: The goal is to eliminate all delays and nonproductive work so that maintenance personnel can work effectively and efficiently by never having to leave a job once they start, except for regularly-scheduled breaks, mealtimes, and the end of the working day.
- In an ideal situation, the only time that would not be counted as wrench time would be things like safety and other critical meetings, break and lunch times, and travel time to and from the job.
- While this measure is somewhat idealistic, it does provide a clear way to assess overall effectiveness.
Fact #6: P&S is the most effective way to improve an organization’s wrench time. The power in improving wrench time is considerable.
- For example, if you have a crew of ten people that have a wrench time of 30% and it is improved to 40%, one mechanic effectively will have been added, and this mechanic has a wrench time of 100%.
Fact #7: The only way to optimize maintenance wrench time is to have an effective maintenance planning and scheduling process with a highly trained maintenance planner or planner scheduler.
Measuring and Optimizing Wrench Time
One of the most effective ways to measure maintenance wrench time is through a Maintenance Utilization Survey Checklist, which can help an organization identify where technician time is being wasted.
Once you have identified where the waste is occurring, you can begin taking steps to optimize your wrench time. The most effective way to accomplish this is through a formal planning and scheduling process, which requires that roles and responsibilities be well-defined to maximize their effectiveness.
One way to clearly define these roles and responsibilities is by utilizing a RACI responsibility matrix. A RACI responsibility matrix is a “chart designed to ensure clear communication and smooth workflows across all parts of a team by clarifying employee roles and responsibilities for each task, milestone, and decision that takes place throughout a project,” (Forbes). An example of this matrix can be found below.
There are several benefits to a formal planning and scheduling process, including:
- Minimizing human error.
- Reducing the overall percentage of reactive work.
- Reducing total maintenance costs by minimizing the amount of maintenance rework.
Typical maintenance costs versus those experienced by world-class maintenance teams can be expressed as a percentage of the replacement of asset value. According to SMRP, replacement asset value (RAV) is defined as “the monetary value that would be required to replace the production capability of the present assets in the plant. It includes the replacement value of the buildings and the grounds if these assets are maintained by the maintenance expenditures.”
It has been found that typical maintenance costs as a percentage of RAV range from 4.5% to 11.2%, whereas the percentage of RAV for world-class maintenance teams ranges from 2.0% to 3.4%.
There are several ways of improving a team’s RAV, including:
- Providing formal training in maintenance planning and scheduling.
- Baselining the current cost of maintenance labor and materials.
- Performing a Maintenance Planning and Scheduling Assessment to identify gaps in the current process and create a plan to optimize planning and scheduling. An example of an assessment is included below.
- Creating a Key Performance Indicator (KPI) Scorecard to measure progress and identify areas needing improvement. The scorecard should be posted in high-trafficked areas such as the maintenance shop or team member breakrooms.
This article is based on the information provided in Rules of Thumb for Maintenance and Reliability Engineers by Ricky Smith and Keith Mobley. To purchase a copy of their book, please visit the Noria Bookstore at store.noria.com.
For questions or additional information related to the material within this article, please contact Ricky Smith at rsmith@worldclassmaintenance.org.
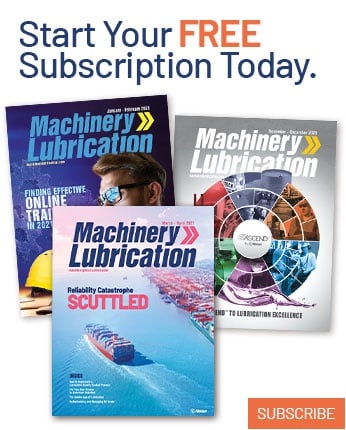