Similar to business models, which are frequently assessed to improve their strategy, modern maintenance organizations are constantly evaluating their processes. This not only avoids negative business consequences, but eliminates the potential risk to people, the environment, and the products that are deeply impacted by equipment reliability.
With regard to asset reliability, failure anticipation through the applications of technologies and strategies, such as condition monitoring, are growing considerably. They not only avoid downtime based on the component’s trending health data, but they also use smart data to support complex decisions that contribute to manufacturing improvements and the extension of asset life.
Condition Monitoring and Artificial Intelligence
Condition-Based Maintenance has been gaining considerable space in the last few years. In some industries, such as automotive or chemical, many maintenance intervention decisions are already automated using Artificial Intelligence (AI) algorithms that operate at process controllers and maintenance systems databases. These algorithms can define the maintenance services’ triggers, as well as their scope.
Manufacturing floor issues can also be anticipated by analyzing process patterns using asset condition monitoring figures. For example, a viscosity deviation problem can be avoided if vibration analysis data is used to detect pump cavitation.
Condition monitoring applications are also expanding in manufacturing. For instance, a critical process parameter, such as viscosity, may start to trend abnormally when influenced by an evolving bearing failure mode. But, appropriate vibration analysis, paired with oil analyses, can anticipate this failure before production losses occur.
However, while these predictive techniques, cross-referenced with process parameters, can be integrated to automatically identify abnormal patterns, these AI algorithms should be tested and validated against stringent criteria, such as Good Manufacturing Practices (GMP). Many maintenance and engineering departments choose to initially develop their AI projects in the utilities area, and once successful, they then deploy these concepts in the production area.
TBM to CBM Transition
The idea of progressively replacing Time-Based Maintenance (TBM) with Condition-Based Maintenance (CBM) isn’t new. In fact, because of its vast list of benefits, the TBM to CBM transition has been promoted by engineering consultants for decades. But CBM adoption with a supporting strategy doesn’t empower higher reliability.
Time-Based Maintenance
Planned maintenance alerts used in predictive and preventive maintenance that are triggered based on a set schedule or time interval.Source: Reliable Plant
This concept is similar to the maintenance of human health. More frequent tests, such as blood or temperature measurements, performed during a short timeframe won’t considerably improve the medical assessment’s accuracy. But, performing other tests that combine to provide a broader account of our current health can give physicians insights that help identify and proactively treat health issues as they develop.
Likewise, with asset health, by integrating the right combination of techniques and digital tools to support data analysis, we can develop a more encompassing assessment of our equipment. Rather than investing in time-based changes (such as increased inspection frequency), the right digitally optimized condition monitoring practices can more accurately avoid critical asset and process failures.
With Digital Transformation programs benefiting from digitally modified engineering tools enhanced by analytics and statistical capabilities, companies are investing more in failure mode analysis.
For example, by using this data, which is stored digitally in an integrated database, risk assessments as Failure Modes and Effects Analyses (FMEA) can be changed into Failure Modes, Effects, and Criticality Analyses (FMECA). This enhances the criticality analysis with statistical calculations based on factors such as sensor recordings, hardware maintenance history records, and calibration logs.
Modern reliability engineering has benefited from introducing these analytics tools and relevant amount of smart data, now digitally available, which helps to assess patterns associated with failures and propose more accurate solutions that avoid failure recurrence.
Vibration Analysis and Lubrication Partnership
Among the vast list of maintenance techniques that help avoid mechanical failures, some combined applications bring the best of both worlds – diagnosis and prevention. In the context of anticipating equipment failures using smart data, let’s explore one of the most effective reliability prediction partnerships – vibration analyses and lubrication.
While lubrication mostly targets failure prevention by reducing wear in rotating elements, vibration analysis integrates with the diagnosis to anticipate unplanned equipment downtime.
Did You Know?
The condition monitoring market is expected to reach $4 billion by 2027, and vibration monitoring technologies are expected to account for the largest market share during that forecast period.Source: Markets and Markets
With vibration analysis, good Root Cause Analyses (RCA) can be performed to successfully create a service plan. This allows for the creation of a scheduling window that can be deployed to minimize production disruption. It can also be combined with additional lubrication practices to decelerate the rate of damage until the repair can be performed.
It's worth mentioning that to experience the mentioned benefits, a good lubrication program appropriately applies the lubrication materials, such as oil or grease, in its appropriate amount and at a suitable frequency.
Condition Monitoring and Sustainability Applications
The energy-intensive processes of many industries have a significant carbon footprint impact. As a reaction, from facility design to carbon offset projects, companies are revisiting their emissions targets and investing in more sustainable operations.
With this mindset, the right combination of condition monitoring strategies can contribute to sustainable initiatives and help determine the exact causes of impending failures that would have a negative environmental impact.
Previously, environmental factors weren’t considered; maintenance prevention investments were assessed mostly for budget purposes and were based off Return on Investments (ROIs) that compared the cost of the investment with the cost of the downtime and the required repairs.
Today, however, other intangible cost-avoidances associated with carbon footprint size are entering the equation. For example, acoustic imaging used to detect gas pipeline leaks not only reduces carbon footprints by preventing the excessive energy consumption that would be required to compensate for the system’s volume and pressure decay, but also avoids the emission of contaminants into the atmosphere.
Ultrasonic and thermography also strongly supports the detection of leaks at steam traps, which not only demands expenses for repairs, but also consumes excessive environmental resources to generate enough energy to counteract the steam loss.
In this way, the combined processing and analyzing of manufacturing data (pressure, flow, temperature) with the maintenance history can contribute to more effective solutions for avoiding faults that can compromise the asset and create harmful environmental outcomes.
Conclusion
Companies are constantly evolving their asset management strategies to be more efficient, avoid losses due to downtime, and eliminate environmental risks by employing modern methods and techniques, such as condition monitoring, in partnership with digital engineering tools.
Combining predictive maintenance techniques, such as vibration and oil analysis or ultrasonic and thermography, can not only avoid downtime, but contribute to manufacturing improvements, especially when using smart data to empower the asset management and process optimization decision-making process.
Strategies focused on the synergy between machine data and manufacturing parameters can foster more sophisticated and in-depth analysis of equipment and process failure modes, positively revolutionizing asset cost management and exponentially improving the ability to predict process problems.
References
1Data-Driven Predictive Analytics Can Transform Plant Engineering, June 2016 edition of Manufacturing Engineering magazine.
2IEC 62740:2015 describes the basic principles of root cause analysis (RCA) and specifies the steps that a process for RCA should include.
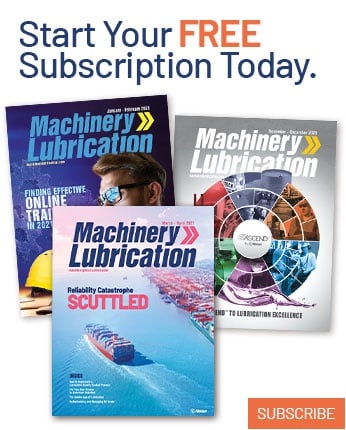