Maintenance optimization is a core trait necessary for any successful plant. By understanding what tasks need to be performed and when they should be carried out, a maintenance team can create a proactive schedule that reduces downtime and removes barriers to success. But how can teams begin shifting from a reactive to a proactive mindset?
First, teams need to get back to the basics. Simple is effective, and checklists are no exception. They are a powerful tool that ensures the most important steps of a procedure are carried out as intended, and a great checklist helps build confidence in even the most junior of members. By revisiting the basics, we build a strong foundation for the rest of our maintenance strategies.
Once a solid base is developed, it’s important to discover how maintenance technologies can help enhance the efforts of the maintenance team and assist with plant development. From data systems to learning modules, technology presents a rare opportunity to go beyond the limits of human error and fill in knowledge gaps to create a holistic program focused on the health and prosperity of critical assets.
On your maintenance optimization journey, it’s essential to uncover quick wins with “low-hanging fruit” that can be communicated to your team to boost morale and improve company culture. Lubrication presents the chance to create a maintenance plan applicable to the entire facility and a success story highlighting the effectiveness of this plan. Remember, even small steps are still steps in the right direction.
Another tool for creating a successful maintenance plan is root cause analysis. Fixing a problem is not the same as solving a problem, and by applying root cause analysis techniques, maintenance teams not only repair a machine, but understand the original source of the issue. By identifying and correcting the problem’s source, maintenance teams prevent the issue from repeating and free up their time to focus on higher-level activities.
These higher-level activities include not only maintenance tasks but also maintenance planning — and a key component of planning is gathering data from across the facility through sensors and connected technologies. But what do you do with this data? By developing a system to understand and synthesize this information, the data can help create proactive, actionable steps that lead to lasting changes.
These maintenance efforts, backed by data, help create a predictive maintenance system capable of reducing downtime and improving machine health. By discovering why machines fail using the data available, teams can predict when and how a machine will fail, allowing them to perform the necessary work needed to keep the machine healthy. This allows for a smoother working schedule for maintenance teams, who can now allocate their time to other projects instead of putting out fires.
By having a system and culture that optimizes the maintenance activities of your team, you can increase productivity while freeing up time to tackle larger tasks that will help the company succeed in the future. By learning to transition from a reactive to a proactive mindset, we can remove our barriers to success and become competitive leaders in the industry.
If you or someone you know would like to be considered to contribute content for future issues of Reliable Plant Digital Magazine, email our editor at bmoll@noria.com.
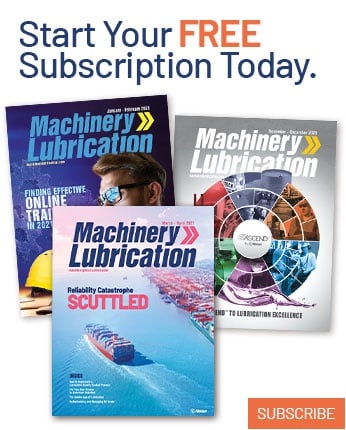