There are two philosophies that dominate the approach to industrial maintenance. The first and most prevalent is that the role of maintenance is ‘fixing things’ and the second and more successful is that the role of industrial maintenance is to ‘keep equipment running’. Some people think these are two ways of saying the same thing. They aren’t. They represent a huge difference in attitude, approach, priorities, and results.
The fix-it philosophy is easy to implement and plays into the skills and abilities of the technicians hired into the maintenance department. The downside is that it costs more to perform and leads to lower equipment uptime and a less profitable business.
The ‘keep it running’ philosophy requires more management, a support system, and constant upkeep. The upside is that it leads to lower maintenance costs, better equipment uptime, and higher profitability. This is a simplification. These are not one or the other philosophies, they are a continuum where a department can be any mixture of the two.
The true goal should be to keep the equipment running and one of the reasons that all department don’t fight to reach that goal is that it isn’t clearly understood how to get there. The following is the start of a bi-monthly series where each article will focus on one of the needs of a successful maintenance department.
The Industrial Maintenance Manager
The philosophy of almost every industrial maintenance department is determined primarily by the attitude and the conviction of the maintenance manager. This is the weak point in the entire system. Understanding equipment and understanding how to troubleshoot and repair it are not the primary qualification for managing a maintenance department and unfortunately that is the criteria often used to choose a maintenance manager.
I’m not denigrating the need for equipment knowledge or the value of people that can troubleshoot and repair equipment. Those necessary skills and talents are just not the primary qualities needed in the manager.
Job one of the maintenance manager is to give the department focus and direction and to maintain that focus against opposition. To do this well the manager has to understand industrial maintenance and the financial side of the business and keep the maintenance department focused in support of the goal – profitability.
In a vacuum or without a clear understanding of what the focus should be departments will always move toward the lowest level which is purely reactive maintenance. Purely reactive maintenance is bad for the department, bad for the site, and bad for the job security of everyone involved.
To maximize maintenance effectiveness and minimize downtime and equipment repair costs requires a web of support systems such as a PM, spare parts, training, tooling, information systems, and several others that will be discussed in future articles. The need, design, and sophistication of each of these support systems will vary with the size of the department and the characteristics of the business.
A growing company that runs a 7X24 schedule will have different requirements from a mature company with a 5X8 schedule. The manager needs to understand the cost and benefits of each of the support systems to design the lowest costs, highest uptime department for their unique situation. The manager also needs to understand these requirements will vary over time.
So where does the maintenance manager gain the knowledge needed to design and implement these systems? This is a problem. There is no one-stop shop for educating maintenance managers. The education they need to run their departments well must be gathered in pieces from a variety of sources sort of like assembling a jigsaw puzzle.
The school of hard knocks and trial and error is one of these valuable sources. Real experience in what works and what doesn’t are rocks that we can build on – but too often this is the only real source of the manager’s knowledge. The manager must learn about concepts that he hasn’t seen or hasn’t seen used successfully and it takes overt effort to do this. Industry publications are full of insight regarding successful programs and successful implementations.
People coming into the department from other companies provide insight into what worked somewhere else, industry conferences offer the ability for structured instruction on specific programs or technologies and the ability to interact with others dealing with the same problems.
Visiting other plants both in and outside of your company and industry often show you a completely different philosophy and structure. Vendors can also be a source of information as they educate you in the hope of making a sale. Search out this knowledge and understand where implementing it will make your company better then learn how to implement it.
Just remember, what worked for someone else may not work for you. Every situation is different and implementing change, even change for the better, is never a slam dunk. The manager not only has to determine the best path, the manager will need to convince people that it is the way to go.
People’s reactions are often random and inertia is a powerful force. This is where the conviction of the manager is essential for improvement. This conviction will be based on knowledge and belief and it will still require a strong person to push it through against opposition inside and outside the department. That’s alright – industrial maintenance isn’t for the faint of heart anyway.
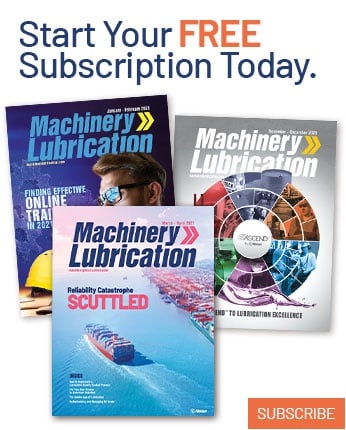