More than two centuries ago, German philosopher Immanuel Kant described virtual reality as an existence within our minds, rather than the physical world. Today, virtual reality (VR) is an established technology that has been deployed in various industries, including gaming, marketing and manufacturing. But what about augmented reality (AR)?
Augmented reality describes a digital enhancement to the external world. A good example of this would be Nintendo’s Pokémon Go app, which overlays images of characters onto the real world through the user’s cellphone screen. There are several popular examples of successful augmented reality. However, many of these have been for gaming or novelty applications.
In the manufacturing realm, most applications for augmented reality are still in their infancy, but they do have great potential. The beauty of augmented reality is the ability to present much more than digital characters or images. Using the technology, you can also overlay instructions, statistics and information.
For example, looking at a piece of equipment through an AR device could show important data related to the machine, such as its current performance, output and temperature. Microsoft’s HoloLens mixed-reality headset is a combination of augmented and virtual reality technologies that has already been deployed in manufacturing facilities for this reason.
However, some of the most beneficial areas of AR’s use is to help solve problems related to maintenance. For instance, if a piece of manufacturing equipment is broken, a technician could use a mixed-reality headset to simultaneously examine the physical parts of the machine while also viewing text, instructions and images to help fix the problem. The information that technicians need when checking or repairing an industrial motor can be projected directly onto the part on which they are operating. This eliminates the need to consult charts and instruction manuals, speeding up the process. Moreover, the projected information guides the operator chronologically so that even a relatively inexperienced worker can perform the necessary repairs.
This is particularly advantageous for complicated pieces of equipment or facilities with few experienced personnel. In these instances, augmented reality can be used to deliver expert support remotely from the original equipment manufacturer (OEM) without needing to fly specialists from one side of the globe to the other.
Industrial robots provide a good example of this flexibility. Imagine a six-axis robot has malfunctioned, but no employees have the expertise to fix it onsite. Using a headset for remote maintenance would allow any employee with an AR device to be guided by a specialist, such as the robot manufacturer based in Japan. The expert can provide support by simulating the actions the employee should perform. This technique can also be used to train new employees, which is a valuable tool considering the current skills shortage.
In fact, training new employees is one of the most valuable areas for AR in manufacturing. When onboarding a new staff member, it can be challenging to ensure the employee is aware of the correct protocols and procedures. Uncertainties can lead to safety issues, especially in processing industries with dangerous operations. In this instance, mixed-reality headsets may not be appropriate because they usually are designed like virtual-reality headsets and can be obstructive and distracting. A smaller device, such as a tablet, cellphone or pair of digitally enhanced glasses, would be ideal.
Suppose a new employee has been assigned to operate a piece of processing equipment that he has never used before. With AR technology, a device could automatically provide machine data to help the employee complete the task correctly and safely, delivering alerts if the machine is outside the specified temperature range.
Jaguar Land Rover has already demonstrated the potential of augmented reality for training purposes in a joint project with Bosch and its software system. The project developed an application that digitally visualized an X-ray onto the dashboard of some of its vehicles. Using the technology, the app allowed technicians to see everything in operation behind the vehicle’s paneling. This removed the need to remove and reinstall the dashboard, simplifying training and saving on costs.
It has been two centuries since the potential of augmented and virtual reality was envisioned. However, it is only recently that the technology is coming to fruition for manufacturing. While AR’s applications in industry may not be as novel as catching Pokémon, the technology is set to make a significant impact on training and maintenance.
About the Author
Mark Howard is the director of EU Automation, an industrial equipment supplier.
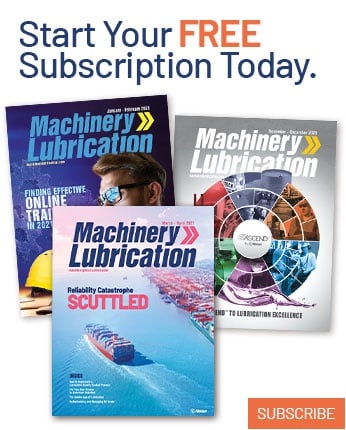