
The Perfect Storm of 1991 – the one that infamously took down the fishing vessel the Andrea Gail in the North Canadian Atlantic – began with a cold front on the East Coast of the United States. The cold front gave birth to an extratropical low just off Nova Scotia, and at the same time, a ridge of high pressure spanned from the Appalachian Mountains northeastward to Greenland. The cumulation of these ingredients eventually formed a nor'easter that absorbed Hurricane Grace.
Just as conditions were perfect for this massive storm to form nearly 30 years ago, manufacturing companies are dealing with the onset of a perfect storm themselves, one stirring up from issues such as an aging workforce, insufficient educational systems and the lack of technical apprenticeships, according to Terry Wireman in his book Training Programs for Maintenance Organizations.
As of 2018, finding skilled workers to fill available positions was rated as the No. 1 issue among employers, based on a recent Plant Services survey. The next two most pressing issues were knowledge capture/transfer (51 percent) and retraining/upskilling workers due to evolving roles and responsibilities (49 percent). Despite U.S. manufacturers adding nearly 246,000 jobs last year (the most since 1988), a mix of baby boomer retirements and ever-changing roles, like the ability to use advanced technological tools on the job, has created a gap between supply and demand for manufacturing jobs. This gap could leave 2.4 million manufacturing jobs unfilled by 2028 and significantly impact the U.S. economy, according to Deloitte's 2018 skills gap study.
As of 2018, finding skilled workers to fill available positions was rated as the No. 1 issue among employers.
So, how is the manufacturing industry preparing for and combating this brewing perfect storm? It is tackling two of the biggest contributing factors: lack of education and/or technical apprenticeships. Not only is it crucial for employers to address these two factors, but it seems as if the younger generation realizes the importance of staying on top of new skills and technological trends. These younger workers are looking for jobs where employers provide a decent paycheck as well as continuing education in their field where they can make a solid impact on the job. The Plant Services survey found that 66 percent of workers say they have participated in or taken advantage of career-development programs offered by employers, while 51 percent say they are very likely to engage with a mentor or a coach if their company provided the opportunity.
Given this realization and the national discussions about supporting trade schools and manufacturing training programs at community colleges, many employers are partnering with educational programs for outreach efforts. Nearly 78 percent of organizations work directly with two- or four-year universities to find new talent. Notably, around 43 percent of organizations (one in five) said they have worked with adult education or retraining organizations to develop current employees' skills or to ensure potential candidates from high schools have the necessary skills.
Working directly with technical colleges and adult education organizations is not only a great way for manufacturers to guarantee the appropriate skills and training are being taught, but it also allows for opportunities like apprenticeship programs where students can learn precise skills through on-the-job training.
Lastly, it's important to consider employee retention as another ingredient contributing to the strengthening perfect storm. While 74 percent of employees say they'd be happy to remain at their current job over the next two years, that number is trending downward from just a year ago. Better pay and benefits lead the way as the top reason why workers would want to leave (71 percent), followed by more attractive job responsibilities (50 percent) and more potential to advance their career (45 percent).
When asked about factors that would cause them to leave their current organization voluntarily, 80 percent of millennials said dissatisfaction with the corporate culture would be the leading factor. About half of baby boomers reported the same thing. This could be due to a shift in leadership styles.
"Millennials are demanding improved workplace cultures and are voting with their feet," says Cheryl Thompson, founder of the Center for Automotive Diversity, Inclusion and Advancement (CADIA). "They are not accepting poor leadership behavior that previous generations did."
Thompson also notes that more millennials are becoming managers and are leading in a more collaborative and inclusive way.
Despite their weariness of the corporate culture, millennials have a much more positive outlook than baby boomers on the use of technology to make their jobs easier. Technology, such as condition monitoring and asset management, are improving their teams' efficiency and simplifying daily tasks. With this outlook comes an eagerness to continuously learn new skills to remain valuable in the industry.
The skills gap is poised to reach nearly 2.4 million unfilled manufacturing jobs over the next decade.
Although the perfect storm is rearing its ugly head, replacing the aging workforce is possible through education and training. The manufacturing industry is experiencing a rapid onset of technology with advancements in artificial intelligence (AI), robotics and the internet of things (IoT). This technology is changing the entire industry, including job skills and current roles. As these changes take hold, many are afraid some positions will be eliminated. However, more jobs are actually being created in manufacturing, according to Deloitte's skills gap survey.
Of the millions of jobs potentially going unfulfilled over the next decade, those positions dealing with digital talent, operational management and skilled production are poised to be nearly three times as difficult to fill in the next few years. In fact, a lack of personnel with the ability to interact with integrated technology was the biggest concern among maintenance mangers when it comes to performing predictive maintenance tasks, based on a Reliable Plant survey.
The good news is we know how to weather the storm. Even better news? Current and potential workers are willing and even eager to develop and continually advance their skillset in the manufacturing industry. It's important to ask yourself where you stand in terms of attracting and training the up-and-coming workforce. According to manufacturing employees, the biggest trends they see in their plants revolve around expanding digital and soft skills, leveraging the digital toolbox, and keeping humans in the loop while working alongside technology.
The skills gap is poised to reach nearly 2.4 million unfilled manufacturing jobs over the next decade. Consistently investing in training by developing a positive relationship between workforce development and highly skilled employees is key to preparing for this gap. The perfect storm is on the horizon. How will you weather it?
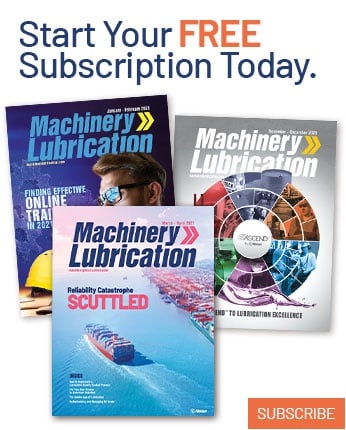