Maintenance and reliability can often be a chaotic world with multiple demands tugging at the maintenance manager’s time, dollars and resources at the same time. Improving the situation takes dedicated effort, planning and a roadmap to follow. It would be ideal if there were a single roadmap developed by experts in maintenance and reliability to tell you what to do and how to get where you want to go, but like life in general, it isn’t that easy.
It just isn’t possible to create a one-size-fits-all maintenance improvement plan because no one else is where your plant, facility or organization is on your maintenance journey. There is also the difference of the place each individual organization will go to reach its goals. Your maintenance organization may be in a completely reactive mode, or like the one I work in, be a good way down the road with an extensive planned maintenance system in place and proper use of predictive tools.
In some organizations, particularly pharmaceuticals and food processing, your path will in many ways be dictated by regulatory requirements. In other businesses, your final destination may be decided by the amount of investment required and corporate buy-in to a full-on asset management strategy or something less rigorous. In the end, you must figure out where you are, how far you intend to go, and create a rational roadmap to get your organization to the desired destination.
Assess Where You Are in Your Journey
The first order of business is to figure out where you are on your maintenance journey. The most obvious way to begin this task is through observation and auditing. Watch how your maintenance organization works each day, whether it is concentrated on preventive tasks and proactive repairs during scheduled downtime or conversely “fighting fires” all day long to keep equipment and production running. If you are using a computerized maintenance management system (CMMS), you can gather data to support what level of reactive versus planned maintenance is occurring.
Another way of identifying where your organization is in the continuum of maintenance maturity is to conduct a formal assessment. You can create your own evaluation using benchmarks for your industry or “world-class” benchmarks available from organizations like the Society for Maintenance and Reliability Professionals (SMRP), which are free to members or available for a fee. Vendors like SKF can facilitate a maintenance assessment for you as well.
There are also free tools available online if you do a search for “maintenance assessment.” The advantage of using a pre-determined assessment is that it saves time, but if you review a number of them, you can create your own, which will allow you to tailor your survey to your organization and its goals and objectives.
Determine Where You Want to Go
Once you’ve conducted your assessment, the next step is to review it with the organization’s leadership and discuss the major areas of concern. These may include safety, equipment downtime, maintenance costs, manpower and technician skill levels among other potential items.
This review will help you to identify which areas are most important to your organization and focus your plan on improving them as a priority. You shouldn’t concentrate only on those areas, as there will be other building blocks that may need to be reinforced to support them and others that must be done in addition to the priority items. Now you have a basic idea of where you want to go.
Choose a Maintenance Strategy
In order to flesh out your plan, you should consult some models of what a fully formed maintenance strategy looks like. Don’t be intimidated by the idea that there are many elements you may not have even touched yet. Just find one that is the “best fit” for where your organization wants to go.
This is where you will need to consider other elements that will interact with and affect your efforts in maintenance improvement. Your business may be in the process of doing a lean implementation or may have completed one. This will impact how you build your plan and the model you choose. You can do a web search for “maintenance pyramid,” which is a popular model for describing the maintenance continuum.
There are other models available from professional organizations such as SMRP. There may also be specific maintenance structures and best practices available within your specific industry through a trade association or other body.
Build Your Roadmap
Now that you have the building blocks of a strategy from your model, you can map your maintenance assessment scores onto the model and identify the areas of greatest potential for improvement. You will also reveal your strengths during this process. You may want to work in one of your areas of strength at the beginning to gain some “quick wins,” which not only will earn management support but can energize the team tasked with the work to be done. No matter where you choose to start, there will be a lot of work identified.
The effort across multiple areas of the strategy will need to be planned and tracked to make your new maintenance journey successful. Creating a tool using a Gantt chart or similar method will help to plan the efforts, level out resource usage and provide a timeline for tracking and accountability. I use a “tactical implementation plan.” Your team likely has a similar tool available.
Create a Plan to Execute
Now that you have an idea of where you are, where you want to go and a roadmap to get you there, it is time to execute. Use your implementation tool to track your progress and monitor your indicators in your CMMS system to verify you are making progress along the way.
It is not a bad idea to periodically (annually) re-perform your assessment survey to measure your progress and identify areas that may need more focus. Re-evaluate your chosen areas of focus from your model and adjust your plan to reinforce your foundation work and keep driving progress. Your plan will be an incrementally changing continuous improvement tool.
We’ve discussed how to make a plan to improve the maintenance performance of your organization. To review the key steps, you need to determine where you are (assessment), figure out where you want (or need) to go (goal setting), choose a model to represent what you want your completed ideal organization to look like (visualize), select the elements to engage in to move you toward your goal (map-building), and create a plan to execute all the items from the roadmap (tactical implementation). Breaking down what at first looks like a daunting task can reduce it to manageable chunks and tasks that, with a little help, aren’t so intimidating after all.
This article was previously published in the Reliable Plant 2019 Conference Proceedings.
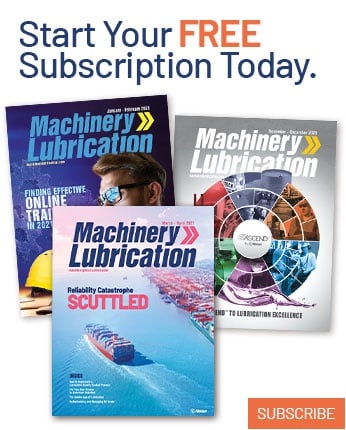