Maintenance is the effort required to fix something before it is broken. A well-structured and implemented maintenance schedule enables plant managers to build a solid and fulfillable production plan. In a well-managed plant, efficiency improvements can be scarce and may only be achieved by streamlining the maintenance processes.
Lack of a Maintenance Plan
The most important task of any maintenance manager is knowing the equipment and taking care of it. However, developing a maintenance plan should also include emphasizing safety and identifying things that could potentially hurt you or your colleagues when not properly serviced.
Planned downtime will be the best time for personnel to work on making the plant a safe and reliable operation. Depending on the production rate and wear, planned downtime may vary from once every 14 days to annually. On the other hand, unplanned downtime is an expensive and time-sensitive disruption of production that must be remedied as soon as possible.
Optimization Process
The right motivation and support from the plant manager will be vital when implementing an optimization process. Extrinsic motivation could be instructions from management to save costs, while intrinsic motivation might be the goal of flawless operation or the need for time to perform other tasks.
Standardized incident and repair reports can help when building a knowledge database. A failure report for a main shaft issue could include an assessment of what went wrong, including any machine noise, the power consumption, bearing clearance, leaks and impurities. The main shaft should then be inspected, and the seals checked for hardening, cracks, dust and impurities.
If this solves the issue, reassemble the shaft and restart the equipment. If not, you may need to further assess the root cause of the problem. This should be done with the assistance of the equipment manufacturer or a service company.
Create reports that detail all abnormalities and causes of failure, including photos. If necessary, have worn or broken parts analyzed and incorporate the results in your report. By documenting all major failures in your reports, you can build a database of solutions for the future.
Finally, remember that maintenance optimization should be a continuous process. Any lessons learned and other knowledge should be available for future assessments. By assessing the status quo, shortcomings become apparent, either through analyzing the equipment’s status or through breakdowns.
Your staff should know the plant equipment very well, but when in-house expertise is not sufficient, third-party consultants can help overcome organizational blindness. Once your action plan has been developed, it then will be time to execute it.
This article was previously published in the Reliable Plant 2019 Conference Proceedings.
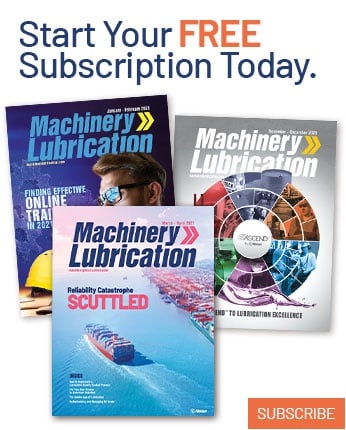