Maintenance managers are experts at making their current schedule work. However, rarely is the current schedule the right schedule. In many cases, schedules are inherited, based on tradition, or copied from a nearby facility. Often maintenance staffing plans are only an afterthought, completed after the production schedule is determined. Most planners and schedulers would agree that every schedule requires a careful blend of the business needs, employee desires, and health and safety considerations. You must start by defining what a schedule is and what it is not.
Defining the Schedule
Many managers believe the schedule is about covering certain days using a shift length. “Are you using 8-hour shifts or 12-hour shifts?” Although both days of coverage and shift length are important considerations, they are only part of the solution. A schedule starts as a system for deploying key resources: capital and personnel. But to be effective, that schedule needs to have employee buy-in.
Additionally, the system must include all the work, pay and coverage rules that make a schedule what it really is. For example, the Monday through Friday schedule where no one works on the weekend is much different than the Monday through Friday schedule where everyone is forced to work every Saturday and half the Sundays. On paper, both appear the same, but the actual schedules, the ones that effect employees, are very different.
The Monday through Friday example is applicable to numerous maintenance organizations. How many plants have maintenance technicians working 40 hours during the week, only to come and work every weekend on overtime? It is such a standard practice that most people consider it a way of life.
The worst part about it is that typically maintenance personnel cannot get to the equipment they need to work on during the week because it is being used by operators. I have even heard, “I stand around on straight time during the week and come in to work the weekends on overtime.”
And if the plant works six days a week, the maintenance crew is working every Sunday. Round the clock and 24/7 operations have very similar problems. I am here to tell you that it doesn’t have to be that way.
So, what if operations does need to work Monday through Friday or 120 hours each week? Wouldn’t it make sense to have maintenance scheduled at some reduced staffing during that period to cover unplanned emergent work or, if necessary, to support with changeovers and other operation-type work? If that’s the case, maintenance should be scheduled to be fully staffed when operations are shut down, like on the weekends.
However, even this strategy has some issues. First, while handing the plant over to maintenance for 48 straight hours might be easy, it may not be that efficient. As techs can only work about 12 hours before they need to rest, anything longer than a 12-hour period doesn’t help.
One option is to set up maintenance on two crews, but are you now spreading out the work because of the workload or to match people? Secondly, do you really want to do the most difficult, critical and non-standard work when there are the fewest managers in place with less support personnel? That doesn’t make sense.
Pitstop Maintenance
Let’s think outside the box a little. You want to use maintenance most effectively and quickly so the plant can get back to work making money. Is there any group maximizing wrench turning in the shortest period possible to get operations back to their main business?
Think about stock cars for a second. Pitstops are critical to keeping the car on the track, but no laps are being made in the pit, just like no products are being made during maintenance. At Daytona, they deal with this by focusing a highly trained crew on the problem at hand and turn the car quickly. Isn’t that what plant leadership wants to do — get back to production and making money?
You can take the pitstop concept into the plant by having the maintenance crew very focused so they can get the job done in the shortest period of time. If the crew has enough resources, they can get in, get out and move onto the next job. This is the essence of pitstop maintenance.
A few years ago, a Midwest bottling plant did just that. The plant had five production lines and several support areas that needed about a day of maintenance each week. Together with plant leadership, we developed a schedule that had a pitstop maintenance team focus on each area one day every week, from Monday through Saturday. We found that 10 weekly hours would cover most issues. Sundays and special down periods could be used to deal with larger, more difficult events.
The pitstops were scheduled during the day. For example, if Line #2 was down for maintenance on Tuesday, the night shift would shut it down early in the morning. Maintenance was prepared to go to work as soon as the line was ready. Work packages were pre-prepared, while tools and parts had already been staged to the area.
As this was the most non-standard and difficult process in the plant, management and supervision were available to ensure things went smoothly. If there were any problems, the original equipment manufacturers (OEMs) were reachable by phone and the controller was there to approve additional time. To make sure production did not miss a beat, key leaders stayed on until the line was back at 100 percent operation.
Where did the crew come from? They were pulled off the shift where many had been “standing around waiting to work the weekend on overtime.” Overall, the facility had 36 maintenance technicians across the mechanical, electrical and instrumentation classifications.
We calculated that 18 techs spread across three shifts could conservatively provide the production coverage needed to support operations. That allowed six techs to support each shift Monday through Friday. This strategy enabled the other 18 techs to form a pitstop crew.
It’s interesting to note that all managers and supervisors believed that the maintenance techs focusing on shutdown equipment were much more effective than those trying to do maintenance while the equipment was operating. When asked how much more productive, their answers varied from 25 to 75 percent more effective.
Assuming 18 of the 36 shifted to the pitstop crew, and the fully loaded wage was $46.96, this increased effectiveness would be worth $400,000 to $1 million annually. The savings could be achieved in better maintenance or in reducing maintenance headcount requirements. Either way, the savings for this bottling plant were significant.
What did this mean for employees? Involving the staff in the scheduling process enabled them to design their own schedule. The decision was made to rotate employees through the pitstop crew on a rotating basis. This permitted everyone to share in more days off and longer weekends.
Conducting pitstops during the day allowed all employees to work at least 50 percent of the shifts on days. The rotation also let everyone cross-train on basic skills while providing well-trained employees for coverage on the backshifts.
For the lines with capacity constraints, the process became even more focused. Different aspects of the bottling process were shut down sequentially. For example, bottles were still being packaged after the filler had shut down. The opposite was true for the startup — the pre-filler equipment came online while packaging maintenance was still wrapping up. The main goal of running a pitstop was to get more operation time out of each critical line, and this was achieved.
Other Considerations
So, what about longer shifts? Are they more or less efficient? On paper, the answer is more efficient. Each day, some time is always lost on the starts and stops of the processes. This would include shift changes, tool issues, lunches, cleanup and more. In fact, managers often admit that they are happy to get 50 percent effective time from their workforce.
Therefore, if I have the same amount of starts and stop times during each shift but have longer shifts, I can increase my labor efficiency. Efficiency increases of 15-20 percent are typical when moving to longer shifts. However, it is important to ensure that some measure of productivity is in place prior to making the change. Failure to have such a measure invariably leads to the same amount of work each day over fewer days.
Another consideration in shift design is the stop and start of shifts or longer runs. Things often break when you start and stop machinery, not when they are just humming along. How many cars break down while being driven on the highway compared with those that cannot start up in the morning? When you are designing operations and maintenance, it is critical to take this into account, both in measurement and in practice.
It also is important to not be caught scheduling maintenance around the day, week, month or year. For instance, if equipment maintenance is required every 10 days, performing it weekly so it can occur on the same day every year can be very expensive. An item being maintained weekly had 52 maintenance events per year. This is 15 more maintenance cycles than if it was done every 10 days. Hence, the added cost would be 15 times the total cost of labor and parts for each cycle.
For expensive items, both in time and materials, it may be worth a little more analysis. The good news is the math behind this type of analysis has already been done. If one has the data, a Weibull curve can be used to calculate where maintenance should be completed. A Southwestern mine worked through this analysis, and by conservatively shifting its maintenance pattern of liner replacements, it saved more than $600,000 annually.
In the end, good maintenance managers should have more questions than not. Most schedules are really a “ball of Band-Aids” that has been developed over time. Imagine a few years ago there was a problem with overtime, so management made a rule on how to deal with it.
Today, the reasons behind that rule may or may not be valid, but the rule remains, as do the rules for weekends, shift rotations, sick days, absenteeism and more. These rules, which often relate to work, pay and coverage policies, can have dramatic effects on the workforce and the ability of an organization to match the required workload. Remember, the goal of any good schedule is matching the workforce to the workload.
This article was previously published in the Reliable Plant 2019 Conference Proceedings.
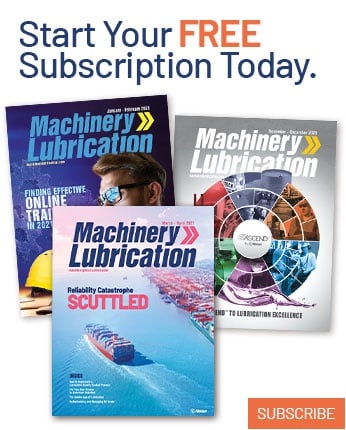