Anyone in manufacturing, supply-chain management or logistics likely has been exposed to the growing buzz around demand-driven material requirements planning (DDMRP). But why is DDRMP gaining popularity and how is it reshaping lean manufacturing principles for industrial manufacturers, enabling them to better react to changing consumer demand?
According to the Demand Driven Institute, DDRMP is "a formal multi-echelon planning and execution method to protect and promote the flow of relevant information through the establishment and management of strategically placed decoupling point stock buffers."
DDMRP thus departs from a traditional forecasting process which originates with a defined customer order or a forecasted demand. DDMRP uses what real demand exists and how that demand could put your buffer at risk, not what might happen based on a single-number sales forecast. This approach requires planning around a range of values, rather than a definite outcome. DDMRP offers a straightforward approach of identifying constraints in the production process and placing buffers in those areas.
This obviously may increase inventory for strategic purposes on some parts, but it should reduce inventories overall because the bullwhip effect is mitigated by these strategic buffers, where traditional lean manufacturing initiatives may be measured on inventory reduction. The following reveals how DDRMP relates to existing lean manufacturing approaches.
A New Look for the BOM
Most discrete manufacturing organizations rely on a bill of material (BOM) to understand demand for component parts and materials required to manufacture products and satisfy orders or projected demand. DDMRP, however, does not use a bill of materials explosion to determine how you plan the manufacturing of a part.
DDMRP recognizes that demand fluctuations can leave a business flat-footed in its ability to respond to the customer or prospect and seeks to smooth out lumps in demand to a greater extent than traditional lean manufacturing process. Lean is built around the assumption that a nice, smooth schedule is the goal. DDMRP lets you make adjustments quickly as things change and can increase agility of the supply chain and manufacturing processes.
Instead of traditional BOM-driven planning and scheduling where planners try to decide if they have enough of a part to fulfill a given demand, under DDMRP they will look at inventory levels and determine what level of demand they can respond to, given the inventory on hand or on order. DDMRP also adds buffers in strategic parts of the value flow.
What is the best place for these strategic buffers? Some of this is based on how common a part is in the BOM and at what point in a manufacturing process you would run out. Buffered inventory is not treated as excess or waste but rather as a way to store potential to meet demand. When that demand materializes, the inventory is then pulled through the system.
DDMRP in Practice
Some customers are already expressing interest in the capabilities of DDMRP, even if they do not initially use that term. What they are asking for is a way to shrink lead times and respond faster to opportunities. They need the ability to produce on time and meet customer requirements to a degree not possible with material requirements planning (MRP) alone. They can do this by buffering their parts intelligently to mitigate risk. Only then can they handle unanticipated demand without sacrificing existing or anticipated orders.
Although beneficial in a process environment, for practical purposes, DDMRP will be more useful in discrete manufacturing. Let's look at a discrete setting such as industrial manufacturing. One pain point industrial manufacturers typically struggle with is reacting to demand shifts, and DDMRP is an excellent solution to this problem. DDMRP could enable these manufacturers to be more competitive because they can turn around projects faster and win more business. After all, if you can commit to satisfying an order and your competitor can't, you will win the business and they won't.
Make-to-stock discrete manufacturers selling through distribution channels can also benefit from DDMRP. For instance, if you are supplying a large chain store, the retailer must keep a buffer in the stores to meet their daily requirements. The manufacturer or retailer may also have a small buffer in their warehouses, but the manufacturer is separated from the end customer by the retailer and often a wholesaler or distributor, so they need to watch for demand signals from the market that will indicate when they need to prepare for changes in order volume and adjust strategic buffers accordingly. These buffers are monitored and adjusted by modifying the unprotected lead times.
ERP Needs a Facelift
As DDRMP becomes more common, enterprise resource planning (ERP) must evolve to deliver functionality that streamlines and formalizes DDMRP in the system of record. Yet not all ERP software can cope with the introduction of DDRMP, so you must look for some key criteria. The software must be able to build in protected versus unprotected lead time and the average daily usage rates for parts. It will need tools to help you calculate these metrics. There must also be a way to identify what demand is real by designating qualified demand versus unqualified demand — with qualified orders linked to a customer order and unqualified demand tied to anticipated demand fluctuations.
In addition, the software must carry the ability to add DDMRP features to certain parts but not others while identifying which parts require buffers. It also will need the level of visibility to buffer inventory and get the best possible outcomes, with the flexibility to quickly adjust those strategic buffers so they stay in an optimal range.
Strike While the Iron Is Hot
DDMRP holds tremendous promise for manufacturers in industries where demand can fluctuate, which is almost any industry in the current consumer climate. It is rapidly replacing lean manufacturing principles and is here to stay. Just be sure you aren't hamstrung by rigid software support.
About the Author
Bill Leedale has more than 30 years of experience leading large-scale implementation and business process reengineering engagements for global companies, making him a sought-after consultant across multiple industrial sectors. Leedale holds a bachelor's degree in business and economics from Wittenberg University and a master's degree in business administration from Ohio State University. His certifications include Certified Fellow in Production and Inventory Management (CFPIM), and Certification in Integrated Resource Management (CIRM).
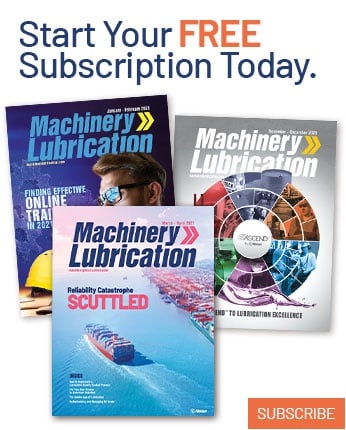