Manufacturing’s Industry 4.0 revolution is affecting every part of the production plant, from equipment to processes to staff. Because the manufacturing line is being digitally transformed, where all machinery and assets in the operation are connected to each other as well as to entities outside the plant, much disruption is occurring.
New technology is available that could unlock opportunities to produce more, fill more orders and obtain more customers. But with anything new, this requires change, and if an organization isn’t ready to embrace change and all the growing pains that go along with it, then it could produce disastrous results.
First and foremost, a production plant needs to, well, produce. To do that, its equipment and processes must be reliable. Thus, plant reliability should be thought of as maximizing output and reducing any unnecessary downtime or waste by optimizing asset and equipment availability.
In smart manufacturing, automated processes manage inventory by connecting supply chains and factories to carry out just-in-time deliveries. The outcome produces a plant receiving what it needs, when it needs it, which improves efficiencies, minimizes waste and boosts reliability to achieve the ultimate goal: increased throughput. However, in a connected operation using just-in-time or lean manufacturing principles, equipment must be available and ready, which means all machinery must be well-maintained and properly operated.
So, if new equipment or technology has been added to the production line or perhaps a significant amount of staff is retiring, people will need to be trained. If workers are not trained, they might not operate a facility’s new six-figure piece of machinery properly. Beyond the obvious hit to the pocketbook with possible damage to equipment, there are the hidden costs, primarily unplanned downtime.
Who's Responsible for Reliability?
Plant managers, as part of their quality management function, are responsible for increasing reliability. To ensure properly functioning machinery, maintenance management must successfully maintain equipment. If a piece of machinery is not maintained, it can fail, and unexpected equipment failures can result in lost production, lost work hours, improper use of plant resources and repercussions for late delivery of finished products. This might also jeopardize future job orders — all of which impact the plant and a manager’s performance.
Since the reliability of a machine or system is only as good as its weakest link, it’s critical for plant managers to identify the weak links and manage or eliminate them. Regular maintenance and efficient troubleshooting are part of a strategy to minimize downtime due to unexpected equipment failure.
With the industrial internet of things (IIoT) and more connected equipment spitting out data, predictive maintenance comes into play. Having insight into knowing the real-time condition of in-service equipment in order to prevent failure before it happens can be a big boon to plant reliability and performance. Also, performing maintenance tasks only when necessary and not routinely, which occurs regardless if it’s needed or not, can reduce wasted time, manpower and resources.
Reliability-centered maintenance is not only a cost-effective practice but can also lengthen the mean time of equipment between failures, which is an important key performance indicator (KPI) in lean manufacturing. But even the most state-of-the-art predictive maintenance system must be reinforced with a solid strategy to get machines back up and running when they do inevitably malfunction. That’s where a trained staff comes into play.
The Skills Gap, Training and Reliability
Finding workers who have technical skills as well as critical thinking abilities to diagnose and repair advanced machines is getting tougher. As a recent Deloitte study showed, 2.4 million manufacturing jobs are expected to be left unfilled in the next decade due to the skills gap.
Even experienced maintenance personnel familiar with a plant’s equipment don’t always use a systematic method to diagnose problems and often end up using trial and error to fix them. This can be expensive if costly parts are unnecessarily replaced or if the process requires an excessive amount of time.
So, how can you ensure your maintenance staff can quickly, safely and efficiently diagnose and repair faulty production equipment before it hurts reliability? Workers likely will need on-the-job training. Maintenance professionals who are trained to troubleshoot electrical faults in a systematic method can find problems and fix them quickly and with the least expense possible so that downtime is kept to a minimum. Troubleshooting training for a maintenance team can pay off in terms of plant reliability and the bottom line.
Other Potential Problems of Industry 4.0
With the connectivity smart manufacturing requires, the opportunity does come with risks, namely cybersecurity. Unfortunately, no one has the magic bullet to completely rule out cyberattacks, as the widespread WannaCry attacks that targeted manufacturers in 2017 showed. But companies can make sure any outside entity that is allowed access to assets takes security seriously, including original equipment manufacturers (OEMs).
In addition, training staff on security protocols must become a necessity in manufacturing plants. Most companies have some type of email-phishing training and possibly policies on personal mobile devices in the workplace, but other vulnerabilities might come from a lack of training, like security procedural mistakes.
The end goal of training employees should not merely be to teach them their job tasks. While that is an important part, the employees’ education should, in some way, advance the company’s goals.
Training and Industry 5.0
Right behind this current revolution in manufacturing is Industry 5.0, which is said to occur when the entire plant, supply chain and enterprise are interconnected. The attention will focus on the interaction between man and advanced automation, such as robotics. Training will become an even bigger role in Industry 5.0 because the technology is moving so fast that employers likely will need to get their staff up to speed on how to use cutting-edge equipment. This means a plant’s training program must be part of an organization’s digital transformation now and beyond.
The skills gap isn’t going away anytime soon, and no matter how automated plants become, people will still be necessary. With a solid plan to quickly and efficiently get workers up to speed, manufacturers can have an edge over their competition.
About the Author
Debra Schug is the marketing communications manager for Simutech Multimedia, a company providing simulation-based training tools for the manufacturing industry. She has regularly contributed to a variety of trade industry magazines and was the editor-in-chief of Food Engineering.
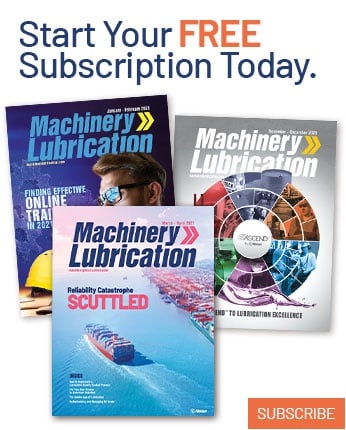