Computerized maintenance management systems (CMMS) have been around for several years and are becoming easier to implement and use. A number of good options are now available. If you search hard enough, you likely can find the perfect match for your unique maintenance situation. The capabilities a CMMS can add are significant if the system is set up and used properly. However, there is one way these systems are not being used well, which is affecting maintenance sustainability.
Many individuals and departments fight the use of a CMMS. Often the system is an add-on to a much more encompassing business-management software package and doesn’t have the true functionality or ease of use the department requires. Sometimes these systems are resisted because they seem to pull personnel away from their primary task of putting hands on the equipment. Physical constraints can also make it difficult for maintenance professionals to use a CMMS well. By physical restraints, I mean issues such as not having the infrastructure or hardware for sufficient technician access. Technicians not having the necessary typing skills to efficiently enter data is another perceived stumbling block.
Of course, any change will have challenges associated with it, but challenges are the meat and potatoes that maintenance departments deal with on a daily basis. There is no reason why the challenges of implementing a CMMS can’t be overcome. All that’s required is to develop the motivation to make it happen. While there are many well-documented reasons for utilizing a CMMS, one reason that maintenance professionals seem to ignore is self-preservation of their strategies and jobs.
When I’ve observed maintenance departments that have regressed, I often notice that production leadership does not always realize it has happened. I suspect the opposite is also true. What this means is that production doesn’t truly understand maintenance. Their opinions are formed on anecdotal observations or perceptions based on the soft skills of the people in the department. This is a situation maintenance imposes on itself, as production is rarely given the hard data that maintenance has in a way that is understandable to the uninitiated. Now, if you’re a poorly performing department with no plans of improving, I recommend you continue this practice because that’s your key to survival. For the rest of you, please read on.
If you visit a manufacturing facility, you’ll typically see information boards that show how the plant is performing. Almost all of this data is production oriented. Whether the data is pertinent or accurate is a topic for another time, but the fact is production has data that is used to justify their existence and strategies. Production (or process, if you prefer) has learned to use data to state their case. This is an ability that maintenance rarely seems to develop or do well. They train their people to act, not to report.
Certainly, there are reasons why maintenance traditionally is weak in this area. For instance, they may be too focused on the equipment to spare resources for this type of soft work, they don’t do it because they are not good at it, no one has ever asked them for that type of information, they prefer to be out in the plant as opposed to in the office, other competing priorities seem more important, and some may be afraid of what the data will show. However, these reasons or obstacles should not prevent maintenance from considering the benefits of using information to justify their existence or path.
We live in a world of limited resources. Few companies ever have the time, money or personnel to do everything they want, so we are always competing for the means to do our jobs. It’s a constant struggle (or game, if you prefer). Except for emergency situations, maintenance tends to stink at this game. Also, without a functioning CMMS, they don’t have the necessary data to even get in the game.
To compete in this arena, maintenance must develop the talent. The first step is to utilize the CMMS effectively. A CMMS is a data repository. If you use it correctly, the information it can provide is extraordinary. This comes with a price, though. The CMMS must be set up intelligently with a lot of thought on the front end. This often involves many secondary steps such as naming and labeling your plant equipment and/or organizing your storeroom so parts have locations, descriptions and prices. Then there are the copious amounts of data input.
After the CMMS has been set up, there is more work to do. It takes determination to establish routines for personnel to input the data from the work and the fortitude to enforce the behavior until it becomes standard routine. A lot of training is involved to ensure the data collection is accurate and consistent throughout the workforce. None of this is easy, but these steps must be taken to make the maintenance department more effective.
Once the CMMS is functioning, use the data it creates to establish a baseline of your performance. For this reason, it is best to set up a CMMS as early as possible. Utilizing the data is where the CMMS process breaks down in many maintenance departments. A familiar refrain is: “Why do I need this data? I know what the problems are and what we need to concentrate on.” Whether these statements are accurate or not, you will need the data not only for yourself but also as a tool to show others what is and isn’t happening in the maintenance department. A huge side benefit is that the data might also point out problems you didn’t even realize. Two truisms come into play at this point. One is that if you can’t measure something, you can’t make it better. The other is that anything you focus on is going to get better.
Although I’ve pointed out some common shortcomings of maintenance departments, I don’t want those comments to be misunderstood. To manage an industrial maintenance department, it takes a certain type of personality, which has its own strengths and weaknesses. The strengths are necessary to handle the job and must be maintained. As for the weaknesses, maintenance professionals must force themselves to understand and use the data to improve. They also need to develop the talents to present the data in a way that shows their successes and shortcomings. They have a good story to tell, which is only a story until it is supported with facts. Publicize these facts so everyone can see them. The data can become as important as the wrench.
Remember, people’s memories are short and unreliable, and perceptions are often formed by almost random events. I’ve seen maintenance departments that had improved drastically and were on a continuing upward trend, but which were perceived as doing poorly. Why? Change always means there are winners and losers. The losers may have the right ear or be able to spread the wrong impression. Without data that is well-presented, those battles can force the maintenance department to become a reactive institution.
Don’t become the fall guy for other people’s problems. Use a CMMS to gather data and learn how to present it to tell your story. Everything is a competition, and whenever more than one person is involved, politics will come into play. The ability to present your data is a political necessity. It also is a tool that can help you run your department more effectively.
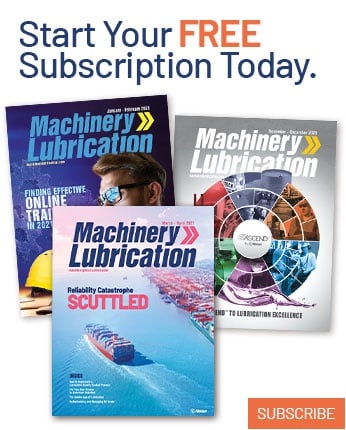