
Utopias are common in fiction, from Plato's The Republic to the Federation in Star Trek. For manufacturers, a world without unplanned downtime would be the perfect utopia. The question is, is abolishing unplanned downtime a far-fetched dream, or is it closer than we think?
Machine downtime costs manufacturers billions of dollars every year. Unplanned downtime halts production, but it can also lead to wasted raw materials or damage to the system itself, amplifying the cost beyond the loss of production.
Research conducted by GE Digital found that 70 percent of companies lack full awareness of when equipment maintenance, upgrades or repairs are due. This is cause for concern, as unplanned downtime is having a significant impact on productivity and causing major losses to the economy. Manufacturers must be aware of when maintenance is required in order to lower this figure.
Does It Have to Be This Way?
Machines break down — it's an unfortunate fact of everyday life. However, there are signs of machine failure that can be monitored and managed. For example, vibration analysis or analyzing the speed of machines can provide insight into the condition of equipment, indicating that it may be about to break down. Proactively monitoring equipment and scheduling maintenance in advance can drastically reduce the risk of machine breakdown, which is why preventive maintenance is taking manufacturing by storm.
What Preventive Maintenance Means for Downtime
Gone are the days of manufacturers being forced to use a run-to-failure, calendar- or usage-based approach, which involved waiting for a motor to fail or a heat-transfer system to leak before taking action. Plant managers can now plan regular equipment inspections, upgrades and troubleshooting to avoid breakdowns.
Industry 4.0 is increasing the capabilities of manufacturers so that maintenance can be data-driven. Information collected by sensors on the shop floor can be relayed to a plant manager and used to make real-time decisions on servicing and maintenance. Employing a digital twin, a virtual representation of a plant's operations, combined with machine learning software could allow the system to identify and plan for faults in advance. In the future, this could involve a system of self-diagnosing and self-repairing – ordering a replacement part or machine from an equipment supplier and planning automated maintenance.
How Close Are We to a Downtime-free Age?
Manufacturers seem to think zero downtime is possible. Eight in 10 companies surveyed by GE Digital thought digital tools could eliminate unplanned downtime, and 72 percent of organizations said that zero unplanned downtime is a high priority.
Taking a proactive approach to maintenance is the best way to reduce your company's risk of downtime. As Industry 4.0 progresses and more connected sensors, digital twins and machine learning software are developed and implemented, unplanned downtime will decrease. While we may still be a ways from the perfect paradise, we are certainly on the right track.
About the Author
Jonathan Wilkins is the marketing director for EU Automation, an obsolete industrial equipment supplier.
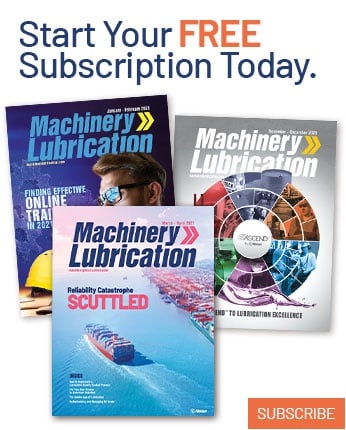