It is not uncommon for criticality ratings to be assigned to equipment. While this practice has some merit, the overall value may be questionable.
Equipment criticality is usually defined as "the consequence of failure of the equipment" and may be given a rating. A typical criticality rating for consequences that impact production in a multi-line process manufacturing operation is shown below.
Where such a scale is used, there likely will be similar ratings for consequences related to safety, the environment and the impact on employees, the community or customer relations.
The criticality rating may be recorded against each item of equipment in the register and used by various maintenance business processes to provide special functions, e.g., to automate the expediting of repairs to spare parts or to select a distinctive label for repair tags. If used for such purposes, the rating has value.
Using Criticality for Setting Maintenance Priorities
The problem with criticality ratings is that they sometimes change and do not take into account the probability of failure. For example, a particular pump may be so important to production that it has an installed spare. Because of this spare, a failure would shut down a production line for only one hour to switch pumps and would thus result in a criticality rating of 6. However, if the pump or its spare is removed for repair, then the failure of the remaining pump would shut down the line for 10 hours while it is repaired. Its criticality rating should change from 6 to 4.
Keeping criticality ratings up to date for this kind of change is an administrative task that is unlikely to be managed with discipline in most operations. Criticality ratings can also change when spare parts are being replenished (i.e., temporarily out of stock) and when different products are being produced.
In addition, just because a piece of equipment has a high criticality rating based on its impact on production, it does not mean that the failure of all of its components should have the same rating. For example, a large piece of mobile equipment may be very critical to the operation. However, while the failure of an engine or a wiper blade may both shut down the equipment, the time out of service will obviously differ. Similarly for a pump handling a dangerous chemical, the safety consequences of a mechanical seal failure may be much greater than a motor failure. For this reason, some have recommended that criticality ratings be assigned at the component level or even the failure mode level. Of course, this introduces a much greater level of administration.
The probability of a production interruption must also be considered. Very critical equipment usually will have some modes of failure that have a long development period (e.g., wear on boiler super-heater tubes), so their repairs may be planned for months or years in advance while maintenance on much less critical equipment continues.
Maintenance work on production equipment should be prioritized in terms of risk, typically the risk of a breakdown occurring prior to the next scheduled opportunity to make the necessary repairs. This risk is calculated as the consequence of failure (or criticality) multiplied by the probability of failure in that period.
While the consequences of a failure mode for any component can normally be estimated, the probability of failure is much less easily determined. Predictive maintenance techniques may help to quantify the probability, but experienced maintenance and operations personnel will generally be in the best position to make such an assessment. These individuals usually have a good idea of the equipment’s criticality without needing a rating system. In fact, they are the ones who likely will provide the criticality ratings for recording.
A good operations/maintenance relationship with disciplined backlog management supported by a practical preventive maintenance program is preferable to a formal criticality rating system. The cost of implementing and maintaining criticality ratings can be significant, and if used blindly for setting work priorities, incorrect ratings will undoubtedly result in some unnecessary losses or costs.
Designing for Criticality
Most manufacturing plants have a set of component standards to assist in the purchase of parts and to minimize the number of spare parts in inventory. These components are usually selected to provide the required reliability at the lowest cost. However, an experienced designer will also take the criticality of service into account when selecting components. The schematic below is of the water distribution system for a large paper mill with three independent operating lines.
Valves A and B both see the same conditions (cold water at about the same pressure and temperature), so the same valve would do an adequate job of isolating each pressure gauge. Should valve B fail, a very local shutdown, or perhaps no shutdown at all, would be required to replace it. However, if valve A were to fail, it could not be replaced without a total plant shutdown. If criticalities are considered during design, valve B should be a good industrial-quality valve, while valve A should be the best that money can buy.
Similarly, the main header isolating valves each require a major plant shutdown for maintenance access and should also be of a very high quality. They are likely to be closed infrequently, and the valve selection should take this aspect of their operating context into account. Main isolating devices in electrical, water, air, effluent and other essential plant services are often the only equipment or components in the plant that will have a criticality rating of 1 (using the rating table above).
In conclusion, equipment criticalities are essential to consider during design and when setting work priorities. However, a criticality rating in the equipment records may be of little help to experienced maintenance and operations people. Where these ratings have value is for providing guidance to staff who support the operation but are not closely involved in day-to-day operations and maintenance, such as purchasing and the storeroom.
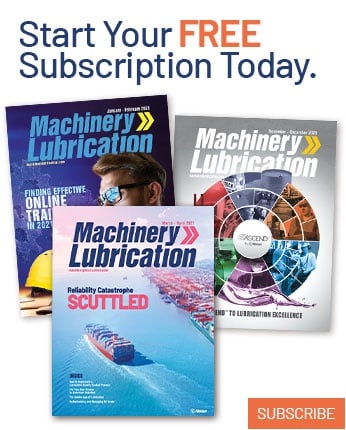