Every day we are hearing more and more about the internet of things (IoT), the next generation of the internet, but what exactly does it mean? Essentially, the internet of things is the interconnection of everyday devices to the internet. The concept of the IoT is so big that it has been described as the fourth industrial revolution after steam, mass production and the internet.
Today, you can control your heating system via your phone or tablet so your house is at the right temperature when you get home. In the future, technicians will be able to see equipment failure codes on their Google glass in real time as the breakdown is happening.
According to Gartner Inc., there will be nearly 26 billion devices on the internet of things by 2020. This growth is largely due to the availability of faster and more reliable mobile networks, where no fixed line connection is needed.
In the coming years, the IoT will be fundamental in improving productivity and efficiency everywhere. It will lead to more efficient power management at plants and factories by automatically adjusting environment control systems to reduce energy consumption when it is not needed.
For example, lighting and heating, ventilation and air-conditioning systems can be switched to a lower mode when systems in the immediate area are powered down. The IoT will also enhance asset management processes by introducing more automation, real-time data analysis and intelligent decision-making.
Following are seven ways the IoT can improve the way assets are managed, but undoubtedly there are many more.
1. Greater Adoption of Predictive Maintenance
The main reason for applying IoT to manage your assets is predictive maintenance. Rather than performing routine calendar-based inspections and component replacement, predictive techniques monitor equipment for pending failures and notify you when a part replacement is required. Sensors embedded in equipment check for abnormal conditions and trigger work orders when safe operating limits are breeched.
When a predictive maintenance strategy is working effectively, maintenance is only performed on machines when it is required, thus reducing the parts and labor costs associated with replacements. With more and more systems shipping with internet connectivity, the concept of predictive maintenance is likely to expand exponentially in the internet of things.
2. Real-Time Data Analysis
Machine-to-machine (M2M) is defined as the technologies that allow machines to communicate with each other. The internet of things takes M2M to the next level by including a third element: data. The availability of all machine data in one virtual network gives original equipment manufacturers (OEMs) the ability to aggregate and analyze the data to generate better predictive analytic models.
Rather than waiting for a system to fail, manufacturers are able to accurately predict failure because sensors start reporting back when operating conditions trend out of specification. By accurately mapping user behavior, identifying failure patterns and quickly recognizing recurring issues, OEMs will be able to design out failures, improve their product and guarantee uptime. This should result in increased customer satisfaction and fewer warranty claims.
3. Accurate Performance Metrics
Availability, reliability and other key performance metrics such as mean time between failures (MTBF) and mean time to repair (MTTR) can be calculated automatically by the system and fed to reporting dashboards. This removes the human element in capturing all downtime, ensuring the data is as accurate as possible. In addition, reliability metrics from different customer sites can be analyzed to identify best practice for implementation around the world.
4. Automatic Software Upgrades
Software changes can improve equipment performance or eliminate technical issues. internet-connected machines make the software upgrade process easier and more efficient. When software fixes or patches are needed, the OEM vendor can push the upgrades to all systems in the fleet at the same time without customer assistance.
5. Recommended Repair Actions
When equipment goes down, failure data from various sources can be gathered, aggregated and analyzed in real time within the cloud. Repair options can be taken automatically by the system, and actions can be recommended to the technician if necessary.
All possible failure data will be used to direct the repair, including system operating conditions at the time of failure, previous repair data from the computerized maintenance management system (CMMS), wear patterns and operating data from the equipment fleet. In effect, the technician will be presented with all the information needed for more effective decision-making and the fastest route to resolution. Deploying a CMMS with an application programming interface (API) that makes connection with IoT devices possible will be crucial in ensuring the actionable information can be presented to the end user in a usable way.
6. Tighter Parts and Inventory Control
Effective inventory control can have a significant impact on limiting equipment downtime and controlling maintenance budgets. Connected stockrooms that proactively monitor inventory movements and stock on hand to ensure the site is only holding what is needed will become commonplace in facilities everywhere. Through predictive maintenance and data analysis, OEMs will be able to optimize the recommended spare parts lists, freeing up much needed capital and increasing customer satisfaction.
7. Remote Assets
When it comes to unplanned breakdown maintenance, the IoT will make repairing geographically dispersed assets a breeze. As mentioned above, it will reduce unnecessary service visits to remote or geographically dispersed assets through predictive maintenance. Imagine connected assets such as wind farms, substations and pumps generating their own work orders in the CMMS with a proposed list of action items and recommended list of spares to complete the job. This will reduce the mean time to repair, which will in turn reduce the costs associated with those emergency repairs.
Every business type can find bottom-line value from IoT devices and services, but this will only occur when the IoT seamlessly interacts with other applications such as CMMS software. The IoT can also be a game-changer for OEMs. It will redefine the business model as equipment vendors supplement their offerings with software and data analytics services. Hardware will ship with greater computing power, becoming more intelligent and more connected.
OEMs will create added value through ongoing monitoring and analysis, improving reliability while reducing unnecessary maintenance costs. Organizations can then allocate their resources in more efficient ways.
The true value of the internet of things can only be fully realized when you take a holistic view of asset management. Powerful virtual cloud networks will continually collect, aggregate and model data to then accurately predict failures and put contingencies in place to limit their impact on system availability. The IoT will become fundamental in improving asset reliability and driving cost takeout by delivering real-time, intelligent and actionable data to connected systems or the end user. Although it may take time for your company to become an IoT data-driven organization, the change is coming, and you should be prepared for it.
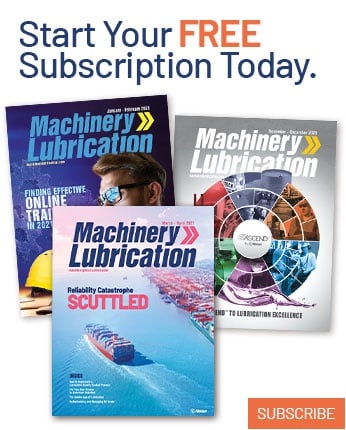