In a competitive, global marketplace, customers are more attuned to quality craftsmanship than ever before. They are also more likely to value corporate stewardship, especially as it relates to sustainability.
In a Nielsen survey, two thirds of customers responded that they would prefer to buy products and services from companies that contribute to the good of society, with environmental stewardship highest on the list. Nearly half of the respondents said they would pay more for such products and services.
Industrial facilities can achieve dramatic improvements in both quality and sustainability by adopting a single process methodology: Lean Six Sigma.
However, personnel in many enterprises — from executive decision-makers to plant employees ― often misunderstand both the concepts of Lean Six Sigma and the realities of its implementation. In this article, we will look at these issues and make recommendations for how plants can reap substantial rewards from a Lean Six Sigma program.
What is Lean Six Sigma?
Lean Six Sigma is a conceptual framework that, when properly implemented, extends far beyond the plant floor and into every aspect of a company's business. It combines two of today's most influential trends:
-
Improving quality, as measured by eliminating defects and process variation, increasing predictability and consistency, and focusing on those products/processes/services that the customer values most (Six Sigma).
-
Reducing waste, as measured by eliminating or drastically reducing unnecessary motion, transportation, inventory, processing, production and defects (Lean).
Lean Six Sigma represents a perfect union of two beneficial practices. Although the concept of Lean encourages a sustainable, cost-effective outcome, it does not by itself provide the necessary process-improvement strategies to achieve these goals.
Six Sigma is all about process improvement, with benchmarking (measuring to establish performance-improvement targets) and prioritizing (determining which process improvements will yield the greatest results) adding value to the effort.
In other words, with Six Sigma, a company can determine exactly how many problems, defects, flaws, inaccuracies, etc., are occurring and then provide a systematic methodology to eradicate them.
DMAIC
Lean Six Sigma involves five distinct steps: define, measure, analyze, improve and control (DMAIC). Although many facilities pay lip service to these steps, the ones for whom Lean Six Sigma provides the most improvement truly embrace them throughout all levels of operation.
DMAIC isn't a magic recipe for achieving the benefits of Lean Six Sigma as a whole. Rather, it is a formula for achieving the incremental benefits that eventually lead to quality and waste reduction, using a continual feedback loop to refine processes in pursuit of excellence.
While Lean and DMAIC may drive improvements on the plant floor, the principles are applicable in every corner of the organization. The excellence that Lean Six Sigma fosters permeates the entire operation, and both customers and employees are happier as a result.
This fact is evidenced by the many companies ― from accounting firms to human resources agencies―who are achieving dramatic results with Lean Six Sigma. These are 100-percent service firms without a single product to design, engineer, build, finish or repair, and yet Lean Six Sigma is meaningful to them.
Keys to Achievement
For many companies and facilities, the breakdown of Lean Six Sigma occurs when management or personnel misunderstands its intrinsic nature. Lean Six Sigma isn't an approach that an organization adopts purely to save money. It also isn't a sprint or a cookie-cutter solution that works the same way for everyone.
Lean Six Sigma requires substantial discipline and governance. In order to prove its effectiveness, it must produce results that can be validated, whether that validation comes from the finance department documenting monetary savings or the service department being flooded with positive customer feedback.
The importance of dedicated effort and patience in a successful implementation cannot be overstated. A few of the core requirements that are necessary for companies or facilities to succeed with Lean Six Sigma include:
-
Organizations must have a compelling reason for implementing Lean Six Sigma.
-
Senior management must be 100-percent invested in and committed to achieving Lean Six Sigma.
-
Companies must be willing to invest in appropriate, qualified resources for the initiative, whether those resources are employees, materials, technologies or a combination.
-
Stakeholders and participants must work together as a team.
-
Team members must be empowered to carry out initiatives without the need for constant evaluation and approval.
-
Organizations must commit sufficient time and resources to training, which is crucial to achieving a positive outcome.
-
When companies work on their priorities, they should focus not on improvements that create change quickly but rather on those that have the most impact on quality.
-
The feedback loop is pivotal to incremental and long-lasting improvement and cannot be bypassed.
Why Lean Six Sigma?
If Lean Six Sigma requires so much dedication and effort, why go through it at all? The answer is that the rewards can be truly amazing. Some of the positive improvements that facilities see when adopting this approach include the following:
Value for the Customer
Lean Six Sigma leads to improved service, delivery and quality, all of which creates value for customers and drives business to the company's door.
Increased Workforce Productivity and Morale
Not only does the process improvement from Lean Six Sigma increase productivity, but surveys show that it also boosts employee attitudes and satisfaction within the workplace.
More Fluid Strategic Positioning
Lean Six Sigma operations are more nimble and flexible regarding changing conditions, enabling them to adapt more readily to unanticipated changes in the business or economic climate.
Stronger Competitive Stance
Customers, vendors and partners are drawn to the type of excellence and success that Lean Six Sigma operations exhibit, making these firms more competitive in all aspects of business operation.
Standards-Driven Achievement
When processes are standardized, personnel training, project management and monitoring, problem-solving and other aspects of corporate operations are simplified and streamlined.
Better Innovation
When personnel and management aren't constantly solving problems and/or surmounting challenges, it opens the way for more innovative and imaginative thinking.
Healthier Bottom Line
Not only do lean operations save money in terms of reduced waste of all types, but greater customer satisfaction and fewer returns result in higher profitability.
Numerous companies have documented annual savings from Lean Six Sigma initiatives that range from $2,000 to $250,000 (and higher) per improvement, and those figures don't include the added value of increased sales, enhanced reputation and expanded customer goodwill.
The U.S. Army reports that its Lean Six Sigma initiatives have resulted in savings approaching $2 billion.
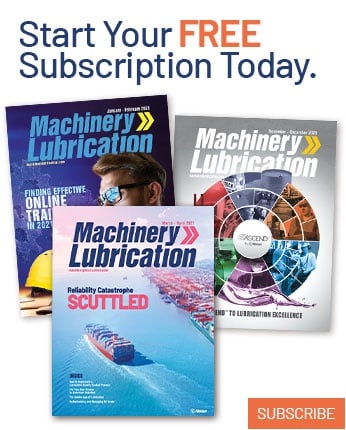