The boiler at the Tulco Oils plant in Tulsa, Oklahoma, has never gone out of service – and the company wants to keep it that way. That’s why this midsized manufacturer of industrial lubricants invested in a computerized maintenance management system (CMMS) when it embarked on a multimillion-dollar expansion project that added 15,000 square feet to its main plant.
Tulco Oils chose Bigfoot CMMS, produced by Smartware Group Inc., to automate maintenance tasks for the new machinery installed during the plant’s expansion, including seven new blending tanks, 50 pumps and an air-compression system.
"With the increase in the number of key components in the expanded plant, we needed a CMMS for work orders and preventive maintenance (PM) management to schedule ongoing maintenance and downtime," said Don Stanton, Tulco Oils’ vice president of operations.
During the expansion, the company also had to automate maintenance processes for the plant’s existing gas, air, boiler and steam systems.
"We added a load to those systems that made it even more critical for every piece of equipment to be well-maintained," Stanton said.
As a designed lubricant manufacturer, Tulco Oils custom blends a broad array of hydraulic and gear oils, transformer oils, turbine oils and cutting fluids used to build equipment sold to original equipment manufacturers – from tractors that plow Midwestern farms to machines that produce consumer goods in China.
Typically, it can take from three to seven days for Tulco Oils to fill orders and deliver its products to customers. However, some local customers have sent out emergency calls for help in one afternoon and taken delivery of lubricants the next morning.
"Often we have to respond to a customer’s emergency," Stanton said. "If a customer has a failed piece of equipment and comes to us with an urgent need to get the oil to repair the broken product, we respond immediately. The giant brands make no such claims about these quick turnarounds."
When expanding its plant, the company used the opportunity to redesign its maintenance operations and configure the CMMS program to fit its specific needs. Instead of using a standard-issue database template, the Tulco Oils team worked with Smartware Group to design an equipment database that matched the company’s asset-management needs and captured the most relevant information for the industrial lubricant market.
"We don’t have off-the-shelf products," Stanton noted. "We don’t stock products because it’s impossible to keep on hand all the different combinations specified by our customers. We custom blend our oils and lubricants for specific orders."
Because quick turnaround time is the linchpin of the company’s competitive advantage, Stanton underscored the importance of keeping equipment at Tulco Oils’ expanded plant in shape.
"If a boiler were to go down, it would kill our ability to blend products," Stanton said. "The same goes for the air compressor. We have an air dryer on the system because oil and water do not mix, so the air must remain dry. We have to make sure these pieces of machinery work every single day."
Prior to adopting the CMMS program, staff members kept a paper trail to track service calls and maintenance tasks for its equipment.
"We didn’t operate off of memory, but we used lots of handwritten records and logs," Stanton recalled. "The more machinery we added, the more impossible it became to manage. We needed a better method for creating preventive maintenance schedules."
Now, thanks to the new CMMS, the operations team at Tulco Oils no longer relies on handwritten work orders. Instead, the CMMS automatically produces email reminders that go to whoever is responsible for the maintenance task – whether that person is a technician on staff or an outside vendor. The system is also designed to avoid email spam to make the process even more efficient.
"One big benefit we’re getting from our CMMS system is better communication about maintenance," Stanton added. "When a piece of equipment is not operational, we can tap in and create a work order without having to run someone down or spend time trying to contact someone by phone."
The company also used the CMMS to set up a non-asset PM calendar, including occupational and environmental safety checks, such as for water contamination analysis and prevention, as well as other municipal safety regulations.
With an expanded plant and increased capabilities provided by its CMMS, Stanton foresees his company gaining even more clout in the marketplace.
"Now we can run circles around our competitors," he said.
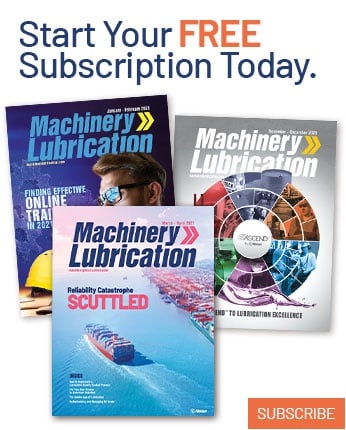