It's one thing to claim customer satisfaction in marketing literature and Web content. It's another to achieve it by precisely measuring customer specifications and winning ISO 9000 certification.
Midland Metal Products (MMP) designs and fabricates permanent advertising display fixtures using sheet metal, wire and tubing for a vast array of consumer goods and products. As a fourth-generation supplier, MMP noticed that many of its processes had simply grown with the business. While going through certification audits, it became clear that the company needed to modernize its maintenance management process. Part of that certification process was to implement a computerized maintenance management system (CMMS).
Measurements Count
Because MMP builds advertising displays for ad agencies that serve hundreds of consumer retail brands, it receives specifications from ad agencies to fabricate displays from scratch.
"Because we do custom displays, we're bringing to life fabrications that haven't existed before," said B.J. McDonald, MMP's co-owner and facility director. "Erroneous measures can ruin the display. Therefore, our measuring tools have to give precise measurements."
To meet ISO standards, all 242 of MMP's measuring tools — from tape measurers to micrometers — must be calibrated precisely to the customer's measurement parameters.
"The ISO 9001-2008 certification helped us look at our production system and come up with a precise process to do this one thing perfectly all the time – from the moment you get the customer order to the end product the customer receives," McDonald explained.
Because of the close tolerances for MMP's custom products, calibrating measurement devices was a major issue.
"As part of our certification, ISO auditors looked at whether our measurement devices could fail," McDonald said. "Bigfoot CMMS helped us win ISO certification."
Before MMP installed its CMMS, the company had no way to adequately track or maintain any of its measurement devices. Today, MMP uses CMMS to schedule preventive maintenance (PM) for every measurement device used in the plant.
In addition, by employing CMMS to issue daily PMs, MMP shows ISO auditors and customers that the company is working within the tolerances of its market. According to ISO standards, each device must have a certificate of calibration to get the designation. This is one area where the company simply cannot miss a PM.
Maintenance Matters
MMP not only uses CMMS for measurement devices but also for its entire plant. Within its 110,000-square-foot facility, there are 138 pieces of production machinery equipment, such as turret presses, laser cutters, press brakes and resistance welders. This also includes a total of 2,100 assets from air and power tools to facility equipment, stationary power tools, personal-protection equipment, material handling and even janitorial supplies. However, of the 165 employees, only three are on its maintenance staff. Before CMMS was implemented, McDonald described the maintenance process as "a verbal and casual method of maintenance, responding to the loudest shout."
"We had no time to put a preventive maintenance program in place," he noted. "That also meant noncritical repairs sometimes got fixed before critical requests that were truly important to the operation. So downtime was a problem, too."
While implementing the two programs seemed like a big task, the initial prep work was worth it.
"The ISO preparation can seem, at times, as if it's adding complexity, but the end result is a streamlined system with increased efficiency across the board," McDonald added. "We get a similar result from our Bigfoot CMMS system. We had to asset-number every piece of equipment we use, down to tape measurers and air-conditioning units. Anything that needs maintenance, replacement, inspection, cleaning and calibration now has maintenance scheduled on Bigfoot CMMS."
MMP also uses CMMS for work orders, repair requests and PM scheduling. Its team generates about 2,400 work orders for PMs a year. This has allowed the company to reduce unforeseen repairs to about 20 percent of its previous workload.
PM Efficiencies Boost Uptime
With 15 seats to serve each department and a hierarchy of requestors, MMP has eliminated interruptions from ad-hoc requests. Now, the maintenance staff is more efficient.
"Once the PM calendar was set up, we were able to increase maintenance department productivity by being better able to distribute PMs more evenly," McDonald said.
The CMMS prioritizes high-value machine PMs so MMP can stay ahead of breakdowns. This is where the biggest improvement has been seen.
"With our PM program, we now average 99.6 percent uptime on our production equipment," McDonald noted.
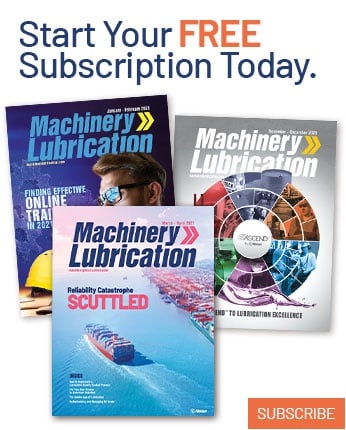