If you desire to implement a world-class effective reliability/maintenance process in your plant, two sequential projects must be performed.
First, map/document the how, what, where and when of what is happening today — not as the manuals say it is to be performed, but what is actually happening. This should be done with a facilitated team with full disclosure and comments allowed from all concerned. Avoid calling it re-engineering; it is an effort to gain full understanding of “today.”
The team should be representative of the maintenance organization (include crafts and operations). This will take several months and should not be secretive. The working lives of many people are going to be affected.
Much of the mapping tools come from total quality management (TQM). Some process flow charts and fishbones can cover the walls. What is being documented is the work order from inception to sign-off by the customer and archiving.
From this process-management documentation will come understanding and buy-in that we really understand what we are now doing. Byproducts of the effort are suggestions on what the process should be and why. After the present is known, it will be possible to write objectives for the process we want to implement.
Second, the team should design what they consider to be a world-class maintenance organization and how it would operate. Again, a skilled facilitator should lead this. New to the same batch of tools are brainstorming and negotiation. Remember, here is where work is being redesigned with impacts on all involved. It may be advisable to have a human resources person on the team.
From this comes a process-management chart defining the new process and, by the way, the information required to make it happen. Now we are beginning to define the requirements for our computerized maintenance management system (CMMS).
An interesting tool at this point is to get everyone involved in mentally walking through his or her workday as if the new process was in place. From this comes understanding and identification of training, roadblocks and a new language replete with openness of feelings and confusion.
Now a plan of implementation can take place. Communicate, communicate, communicate. Remember, the most important employee in a process is the one who operates a machine or process. His or her skill makes it or breaks it. Who is the most important person when the machine fails? The maintenance technician.
The bottom line is that a new process must provide actionable information tied to assisting the technician to perform world-class work and feel a bit of self-actualization at the end of the day. How does the redesigned process help him on a daily basis? If it does not, it’s back to the process design.
If a new CMMS is included in the planning, now is the time to complete the specifications and start the acquisition process. I doubt there is a CMMS that meets all the requirements, and there may have to be some modifications to your expectations. Just be sure to buy the CMMS that supports your process, not the other way around.
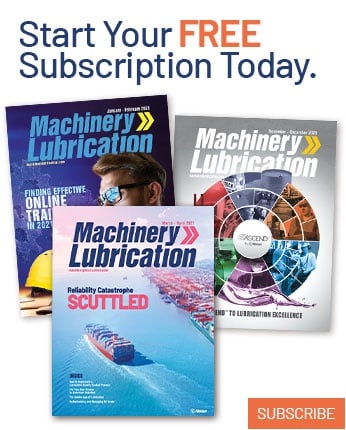