Most of us come from traditional plant organizations with an operations group and a maintenance group with their own supervisors and specialized skilled crafts.
One of the major European postal services decided in the late 1990s to make a change in their plant maintenance organization. In my own U.S. Postal Service, there had been talk for years of combining the operations and maintenance supervision and reducing the supervisory ranks. It is easy to say, but how do you do it? Be careful of what you wish for.
They negotiated with their union to change the working condition of “supervision” (changes in hours, wages and working conditions are negotiated contractual obligations) to put the operating equipment technicians under the operations supervisors. In doing so, they split the maintenance craft workforce and established a plant facilities maintenance support function separate from the operations maintenance function.
The facilities function had responsibility for everything but the operating equipment. That included storeroom, custodial, HVAC, all the plant’s infrastructure and the computerized maintenance management system. Work order estimating was done by the facilities planners.
Operations now had control of their own machines, both production and maintenance. The thought was to make teams that could work together and decrease downtime, better identify degradation sooner, and “keep the maintenance employees involved.” In mail-processing plants, there is considerable time spent by maintenance personnel on “area assurance,” of which operations wanted to take advantage.
In a previous article, I discussed the “enabling process design” and focused on the levels of effort and training required for making a change such as this in people’s lives. Rather than tell you the level of effort, I will relate several of the results:
- The supervisors had problems communicating with the technicians and vice versa. The supervisor could add nothing of value to assist the technician when a piece of equipment was down and also did not know how to judge technician performance.
- Supervisors tended to drift toward the operators and avoid the technicians until something broke down. Technicians felt they were subordinated to the operators and felt unappreciated. This led to a reduction of discretionary effort and creativity as it was not recognized.
- The area assurance was misunderstood, and supervisors were uncomfortable for appearing lax toward technicians and pushing the operators. Cooperation between the two factions was less than before the big change.
- The technicians felt disenfranchised, not really belonging. In maintenance, they had camaraderie, mutual support, management that championed them and a home.
- Issues arose over planned work orders between the technicians and the estimators, and between the estimators and the supervisors, with the supervisors trying to understand the now fragmented process for which they used to be a benefactor, but for which now had a part in completing the work order.
This was implemented one plant at a time, and it became evident that maybe a plant-by-plant evaluation should determine the readiness to attempt this change. It resulted in a decision that “one size does not fit all,” and that there could be two approaches: Leave some plants as they are and implement the new structure through a modified process to address the learning from the earlier-on plants. Some early plants reverted back. It also became evident that retrained maintenance supervisors may be more successful in managing a mixed team of operators and technicians.
The lessons are many in this story. I believe that planning for such a change must focus on the roles of each player. I am a believer in getting people to verbally walk through a typical work day as though they were in the new process. This should be done with teams of all involved. Not only should this be early on to beta test a concept, but should be carried forward for all employees involved in every installation.
If you are considering any kind of change, this story is a good beginning for facilitated training sessions on enabling change, along with all of the other process management redesign tools that quality and re-engineering bring to the table.
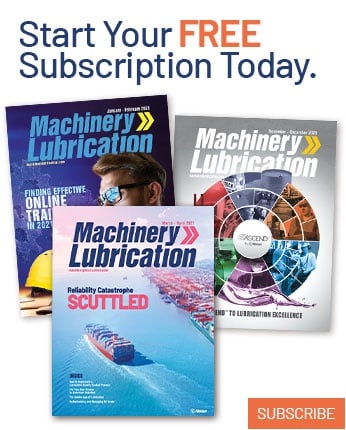