Experimental modal analysis (EMA) and operating deflection shape (ODS) analysis are new techniques used to animate the dynamic response of mechanical systems.
An EMA provides mode shapes associated with natural frequencies of a mechanical system. An ODS offers an animation of the deformation characteristics of a vibrating mechanical system during operation.
The animations can be extremely helpful in defining areas of structural weakness or identifying areas of mechanical “looseness.” In cases of resonant excitation, the animation techniques can be used to evaluate the potential benefit of structural and/or mechanical modifications.
Experimental Modal Testing
Excitation of a natural frequency, referred to as resonance, is one of the most common reasons for excessive vibration of machines and supporting structures and foundations. In some cases, the source of the dynamic force that excites the resonance can be identified and removed.
However, in most cases, the solution to the resonance problem requires design modifications directed at changing the natural frequencies. A complete understanding of the modal parameters of the mechanical system is imperative to any study involving the development of a structural or mechanical modification.
There are many experimental procedures available for identifying the modal parameters of a mechanical system. Modal parameters are dynamic characteristics of a system and include the natural frequencies, mode shapes and damping for each mode of natural frequency.
Experimental modal analysis (EMA) is a test and analysis procedure that provides estimates for all of the modal parameters of a mechanical system.
An understanding of the mode shape is necessary for the evaluation of structural and/or mechanical modifications proposed for a vibrating mechanical system. The mode shape will provide information relative to locations within the mechanical system that are too flexible.
This information can be used for the optimization of the design of any modification made for the purpose of altering the modal characteristics of a system.
An EMA requires impact response data for many locations and directions, referred to as degrees of freedom. The number of degrees of freedom of the test must be sufficient to accurately define all of the mode shapes.
The relative magnitude and phase information at all of the degrees of freedom are plotted to provide an animation of the mode shape at every natural frequency. EMA software is commercially available to facilitate the curve fitting and animation of data.
An experimental modal analysis can be performed using either one of two impact test methods: fixed excitation or fixed response. In the fixed excitation test, the impact location and direction remains stationary for the entire test. The response transducer is moved to obtain data at all of the degree of freedom locations. This is referred to as roving with the response transducer.
The fixed response test method requires that a response transducer remains stationary at a single data location while the impact hammer is moved to excite the mechanical system at each and every degree of freedom. This is referred to as roving with the impact hammer.
The principle of Maxwell’s reciprocity states that the results obtained using either of the test methods will be identical if the mechanical system is perfectly linear elastic. However, very few real industrial mechanical systems are perfectly linear elastic.
Non-linearities introduced by bolted connections, fluid films, load related support stiffness, etc., will affect the results of the modal test.
The fixed excitation method is recommended to minimize the effect of structural and mechanical non-linearities. The participation of a non-linearity in any mode shape will be nearly constant if the force used to excite the mechanical system is applied in the same place during the entire test.
The fixed response method is typically used to test mechanical systems that are constructed of non-magnetic materials, thus requiring the response transducer to be attached using epoxy cement or other adhesive. The time required to complete a modal test of a complex mechanical system can be prohibitive if the fixed excitation method is used and a response transducer is cemented to the mechanical system at each data location.
For non-magnetic structures, the fixed response method is much faster, requiring a single transducer to be cemented to the mechanical system as a reference point. Data is then obtained by simply exciting the system at each and every degree of freedom with the impact hammer.
Experimental Modal Analysis Case History
Catastrophic fatigue failures of industrial fan wheels have been attributed to the excitation of natural frequencies (resonance) during operation. The most common causes for this type of failure are:
1. Excitation of the principal nodal line (wobble) mode of the rotor by dynamic forces produced at either one or two times the rotation speed of the fan. Dynamic forces are normally developed at one times the rotational speed of the fan due to imbalance.
However, dynamic forces can also be developed at one or two times by misalignment, disk skew, looseness between fan wheel and shaft, structural asymmetry, bent shaft, etc.
2. Excitation of the principal nodal circle (umbrella)or two nodal diameter (chip) modes of the fan wheel by pressure pulsations produced at the blade pass frequency or by aerodynamic (rotating stall) or acoustic sources.
An impact test can be performed to determine the natural frequencies of a fan rotor. A picture of a typical shop test arrangement for the modal analysis of a single wide fan is shown in Figure 1.
Figure 1. Single Wide Fan Rotor
An experimental modal test of the fan rotor was performed to identify the natural frequencies and mode shapes thereof. The results of the modal test were then compared to the frequencies associated with dynamic forces produced during operation to evaluate the probability of resonant excitation.
The fan wheel was designed to operate at 1,180 rpm (19.67 Hz). Since the fan wheel contained 12 blades, it would produce a dynamic blade pass pressure pulsation at 236 Hz.
Figure 2. Impact Test Results
Figure 2 contains the results of an impact test performed to identify the natural frequencies of the rotor. The upper plot shows the “ring-down” response. A trigger delay was used such that some of the data prior to the application of the impact force was retained in the FFT Analyzer.
The amount of background noise can be visualized in addition to the approximate “ring down” signal/background noise ratio. The “ring down” characteristic of this waveform is a clear indication of a valid impact test.
The lower plot is the transfer function. The transfer function is obtained by dividing the frequency spectrum of the response data by the frequency spectrum of the impact force. It is an indicator of sensitivity since it is in units of the amount of motion per pound of force.
Peaks in the transfer function curve are indicative of a natural frequency. Natural frequencies are evident at 42.5 Hz, 73 Hz, 107.5 Hz, 140 Hz, 175 Hz, and 236.5 Hz.
Figure 3. Mode shape at 42.5 Hz
A complete experimental modal test was performed to determine the mode shape for each natural frequency. A side view of the mode shape for the natural frequency at 42.5 Hz is included in Figure 3. This mode shape is commonly referred to as the principal “wobble” mode.
It is also referred to as a single nodal line mode. The line of data points associated with the blade tips form a nearly straight single line, having one maximum positive and one maximum negative nodal location.
This mode was not considered a problem since the natural frequency was much greater than both one and two times the rotational speed of the fan and was much less than the frequency of either the blade pass or acoustic pulsations.
Figure 4 contains the mode shape for the natural frequency at 73 Hz. This mode shape is commonly referred to as the “umbrella” mode. It is also referred to as the principal nodal circle mode. The line of data points associated with the blade tips form a nearly straight single line and all move in phase axially together.
This mode can be very sensitive to dynamic pressures since the entire surface of the back plate of the fan wheel moves in phase. However, it was not considered a problem for the subject fan since the natural frequency was much greater than both one and two times the rotational speed of the fan and was much less than the frequency of either blade pass or acoustic pulsations.
A side view of the mode shape for the natural frequency at 140 Hz is included in Figure 5. This mode shape is the two nodal diameter mode, sometimes referred to as the “butterfly” or “chip” mode.
The line of data points associated with the blade tips (trailing edges) form a curved surface with two maximum positive and two maximum negative axial nodal deformations.
Once again, this mode was not considered a problem since the natural frequency was much greater than both one and two times the rotational speed of the fan and was much less than the frequency of either the blade pass or acoustic pulsations.
Figure 4. Mode shape at 73 Hz
Figure 5. Mode shape at 140 Hz
The experimental modal study indicated that the natural frequencies associated with the major modes of concern were all separated from the frequencies of dynamic forces produced by the fan and should not be a problem.
However, the impact test identified a natural frequency at around 236.5 Hz, which almost coincided with the blade pass pressure pulsation frequency. The mode shape for this natural frequency was developed to investigate the potential for excitation thereof by the dynamic pressure pulsations that would be developed by the fan.
Figure 6. Mode shape at 236.5 Hz
Figure 6 contains a side view of the mode shape for the natural frequency at 236.5 Hz. This mode shape is referred to as a four nodal diameter mode. The axial deformation of the fan forms a curved surface with four maximum positive and four maximum negative axial nodal deformations.
The natural frequencies identified by the impact tests were for a stationary wheel. The actual operating natural frequencies will be affected by centrifugal stress stiffening and gyroscopic effects.
Although centrifugal stress stiffening generally has less of an effect on the higher energy mode shapes, such as the four nodal diameter mode, it would only have to be increased by a small amount to fall outside of the magnification range of the natural frequency. The amplification range of this natural frequency is limited due to the extremely low amount of damping.
The experimental modal study discovered a higher energy mode with a potential for excitation. Although this mode would not be as sensitive to dynamic pressure pulsations as the previous two modes, if excited, it could still adversely affect the fatigue life of the fan wheel and the reliability of the air-handling system.
Because of the results of the experimental modal test, this fan wheel was strain gauged to evaluate the dynamic stresses during operation and confirm that the stress stiffened value for the natural frequency was not a problem.
ODS Test Procedure
The test procedure for an operating deflection shape analysis consists of acquiring information regarding the displacement and phase of a mechanical system at any discrete frequency. An ODS test is performed while the equipment is in operation using either single- or multi-channel instrumentation.
The first step in either a single-channel or multi-channel operating deflection shape test is to develop the ODS model that will be used to animate the data. The number and location of data points used in the model must be sufficient to describe the deformation characteristics of the mechanical system.
An inadequate number of data point locations could result in visual aliasing that could lead to a misleading ODS animation.
The amount of data required to provide an accurate ODS animation is dependent upon the vibrating mechanical system to be analyzed. An understanding of the structural dynamics of the system is necessary to develop an optimum ODS test procedure. Knowledge gained from preliminary vibration test results can be used to optimize the test procedure.
Novice analysts should obtain as much data as possible. The acquisition of too much data will not hurt the operating deflection shape animation. Also, since the ODS test is performed while the equipment is operating, the extra time required to obtain additional information beyond what is optimally required should not affect the productivity of the equipment, although the same cannot be said for the productivity of the analyst.
The data acquisition technique used in a single-channel analysis differs from a multi-channel analysis. In either method, attention to bookkeeping is extremely important to ensure an accurate animation of the vibration data. Each data point must be stored with proper identification, including identification number, direction and sign (+/-).
Single-Channel ODS Procedure
In a single-channel test, the operating deflection shape animation is based upon the absolute amount of response obtained for each vibration measurement. Phase information is obtained from a tach signal, usually placed on a shaft that rotates at the frequency at which the animation is desired. Response data is obtained by roving with a transducer among all of the data points in the mechanical system.
Vibration data should be acquired in all three orthogonal directions for each data point location. Therefore, the total number of degrees of freedom in the ODS animation will be three times the number of data points identified in the model.
Vibration and phase must be obtained for each degree of freedom. This information can then be manually entered into a commercially available modal/ODS computer program to obtain the animation of the deflected shape of the mechanical equipment.
Multi-Channel ODS Procedure
The animation of multi-channel ODS test data is based upon a curve fit of the magnitude of vibration at multiple locations throughout a mechanical system relative to the magnitude of vibration at a single reference location. The phase information required for the animation is obtained from the cross-channel function of the reference and response transducers. A tach signal is not required.
Figure 7. Multi-channel ODS Test Setup
Figure 7 shows a typical multi-channel ODS test setup. The reference transducer should be placed at a location that contains a significant response at every frequency at which an ODS animation is desired. It remains stationary during the entire test. Response data is obtained by roving with a transducer among all of the data points in the mechanical system, collecting data in all three orthogonal directions for each data point identified in the ODS model.
The frequency response function (FRF) for each data point contains the phase and relative magnitude of vibration between the reference and response transducers.
Many multi-channel analyzers have the capability of automatically transferring the FRFs to commercially available ODS software, eliminating the need to manually input data. The ODS software is then used to provide an animation of the deflected shape of the mechanical system at any discrete frequency within the frequency range of data acquisition.
One advantage of multi-channel testing is that the variation in vibration that might occur during an ODS test will not affect the accuracy of the animation because a multi-channel ODS is based upon the relative magnitude of vibration between the response and reference transducer.
For linear mechanical systems, the vibration at the response transducer will increase or decrease in direct proportion with the reference transducer. This is important for lengthy tests of large mechanical systems.
Data can be appended to a multi-channel ODS animation months or years later if the structural dynamic characteristics of the mechanical system are not changed. Since a single-channel ODS animation is based upon the absolute magnitude of vibration at the time of acquisition, variations in vibration will adversely affect the accuracy of the animation.
In addition, a single-channel operating deflection shape is limited to the animation of the response of the mechanical system at the rotational frequency of the shaft at which the reference signal is obtained. Multi-channel ODS animations can be developed at any frequency within the defined frequency range of the analyzer.
This is important in cases where vibration does not occur at either shaft speed or a harmonic multiple (such as aerodynamic and flow-induced vibration, response to broadband excitation, etc.).
ODS vs. Modal Testing
Operating deflection shape analysis is often used to either supplement or sometimes replace a modal analysis. If a mechanical system produces a dynamic force at or near a natural frequency, the resultant operating deflection shape will approximate the mode shape for that particular natural frequency.
Since an ODS test is performed while equipment is operating, it can be used to define the structural dynamic characteristics of a resonant condition without interrupting production. A modal test requires that the equipment not be operating, which in some industrial processes can be very difficult.
An operating deflection shape analysis cannot identify natural frequencies that are not excited during operation of the mechanical system. Therefore, the ODS test does guarantee that other mode shapes do not exist.
Impact testing is recommended to identify all natural frequencies within the frequency range of concern before modifying any mechanical system based upon the results of an ODS animation. A complete experimental modal analysis (EMA) is recommended for cases where several natural frequencies are identified.
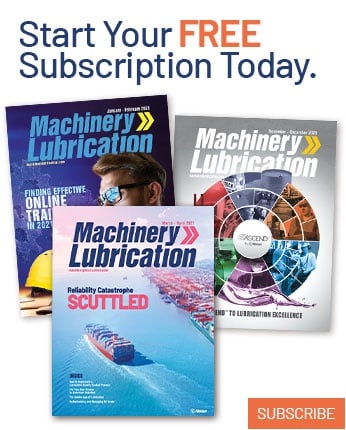