Nothing leverages your parts and training budgets like standardization. It is one of the key areas of the 5-S process. The more you can standardize, the fewer parts you need to maintain and the further your training goes.
Some plants have dozens of manufacturers represented on their production floor with the subsequent glut of critical spares in the storeroom, shelves full of manuals and lost time while technicians re-familiarize themselves with troubleshooting procedures. It can also mean extra money spent on special tools, calibrators and handheld programmers, as well as maintaining extra vendors on file with the insurance, credit and shipping requirements that go with them. It takes some time and effort up front to establish standards, but the payoff can be continuous. The flavor of the month may be sexy and/or cheaper at the time of purchase, but you will probably pay for it later.
Here are some simple guidelines to get you started. These are just a few places to look but may not be the place you want to start. Review your facility for problem areas and opportunities, then formulate your plan of attack.
Check out your present equipment and look for commonalities like motors, variable frequency drives (VFDs), gearboxes, chains, sprockets, solenoid valves, PLCs, etc.
- If you are primarily a “one brand of PLC or VFD” plant, get your distributor to help you create a standard that leverages its stock. For example, if you use VFDs, consider standardizing on the largest horsepower-rated drive in each frame size. If the 30-, 40- and 50-horsepower models are the same frame, this range of drives can be consolidated into the 50-horsepower model. This means one spare in the storeroom instead of three. The cost savings can help compensate for the extra cost of the installed drives. Your distributor may only stock the largest horsepower size anyway and likely stocks it without a communication card. Follow his suit and leverage his stocking strategy for yourself. You also make emergency repairs faster and easier to manage, since the chances are good that you actually will have a spare available this way.
- NEMA frame motors are dimensionally interchangeable, so look for the brands that work the best for you and consolidate your spares while specifying them for future installations. It doesn’t always work with manufacturers, but the old saying goes that you know you won’t get whatever you didn’t ask for, so ask for it and see what the OEM says.
- ISO dimension valves, solenoids, relays, etc., are also dimensionally interchangeable. Move this direction and you can use any ISO-compliant manufacturer’s product in a pinch.
- Shaft couplings can be of different types and brands, so look for opportunities to standardize on the brand and type that serves you best. The local stocking distributor can make a difference if it stocks what you use and you don’t have to wait for a replacement element. Check into standardizing on sizes, too. If a unit can cover multiple horsepowers, it may be cheaper to use it on all of those horsepower applications rather than stock multiple spares. The time savings can be significant if the techs don’t have to search for the right element.
- PLCs are a good place to save some parts money. If you can standardize on a brand and format, you leverage your spares and your training.
- ANSI pumps are like NEMA motors in that the dimensions from flange to flange are the same. Where it gets complicated is the repair parts for the power-ends themselves. Different shafts, bearings, seals, etc., can add up fast. If you can move toward a single brand for similar applications, you can standardize on power-end assemblies and seals. If you use both stainless steel and carbon steel shafts, see if the stainless steel will work in both applications. The price difference is not as big as you might think. Having several variations of the same size seal means more spares and more opportunity for misapplication mistakes. See if you can use a higher-end seal (like hard surface vs. carbon surface) for more applications. While it will cost more initially, you will have fewer spares in the system and won’t have to worry about a tech putting a low-end seal into your aggressive product pump.
- Don’t forget that your procedures are a great place to save time and money. There are lots of procedures available out there from OEMs, vendors and organizations that can save you time. Like the old saying goes, “Why reinvent the wheel if someone else has already done it?” This can mean anything from a standard inspection procedure from the Internet to a product-specific repair or replacement procedure from the OEM.
Like most journeys, it starts with the first step. Decide to make the journey and then dive into the available information stream for help. There are plenty of folks out there to help you, so ask your vendors, peers, techs and contacts for suggestions. Then, you can look at your plant and seek out the hidden opportunities. Remember, reliability doesn’t cost — it pays.
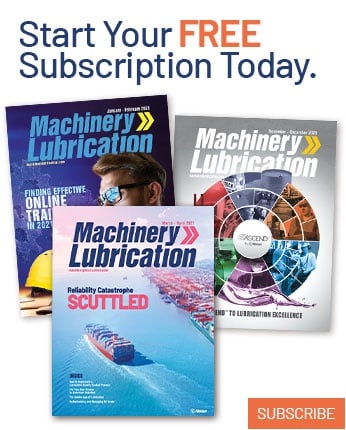