Here is a list of the top five GE technologies that turn waste into energy.
1. The Nuclear Reactor That Eats Its Own Waste
![]() |
GE’s Hitachi Advanced Recycling Center burns nuclear waste (even weapons-grade plutonium), and emits zero CO2.
Here’s the secret: The system uses sodium to control the nuclear reaction, instead of high-pressure water. Sodium-cooling allows the reactor to “burn” the leftover energy in used fuel. When used fuel is removed from a traditional water-cooled reactor, 95 percent of its potential energy is still untapped.
2. The Jenbacher Engine
![]() |
The Jenbacher could be called the alchemist of energy: It’s a gas-fueled reciprocating engine that can run on natural gas, biogas, landfill gas, coal mine gas, sewage gas, and more.
Jenbachers are used by a broad range of commercial, industrial, and municipal customers to generate power, heat, and cooling. Europe currently has more than 1,100 engines running on biogas, and they’re being used to convert coal mine gas to electricity in Australia and Ukraine. (China’s largest chicken waste biogas plant is seen above).
3. The Hybrid Locomotive
![]() |
The Evolution Hybrid Locomotive can capture and store braking energy for later use. Every time the conductor hits the brakes, ordinarily wasted braking energy goes to fueling the battery.
The energy that’s wasted in braking a 207-ton locomotive during the course of one year is enough to power over 8,900 average U.S. households for a year.
4. Waste Heat Recovery
![]() |
The technology GE just acquired from Calnetix recovers heat given off by industrial processes and uses it to produce electricity. It’s a fast-growing trend in the global power industry, and for good reason: it can dramatically improve operating efficiency while lowering a carbon footprint.
How it works: heat is captured in an evaporator that boils the working fluid, producing vapor. The vapor expands, spinning a turbine, which drives a generator and produces electricity. The vapor is then cooled back to a liquid and pumped back to the evaporator to repeat the process.
5. Re-Using Industrial Wastewater So There’s More For Your Tap
![]() |
Twenty percent of all water consumed is used for industrial purposes — a medium-sized industrial cooling tower sucks up 1.5 million gallons of fresh water each day. GE’s TrueSense technology can slash this fresh water use by up to 20% and save $400,000 annually — with part of the system using an iPad-sized monitoring system and a set of diagnostic tools. By industries using less water in the first place, there’s more freshwater available for the drinking water that energizes you.
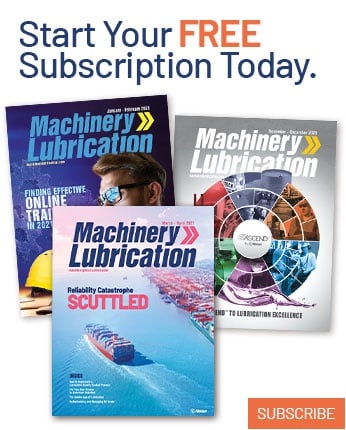