Whether it’s a budget issue, management buy-in, lack of individuals or just a small company with limited funds, there are ways to establish an effective oil analysis program with minimal startup and operation costs.
In this article, you’ll read case studies on alternatives to expensive in-house test equipment, good utilization of outside labs, oil storage solutions, methods of reporting findings to further the program, selling the program to upper management as well as to operations and maintenance, and starting over again when your facility is sold.
Here are the steps I experienced setting up our oil analysis program:
- Purpose of an oil analysis program
- Our attempts to set up a state-of-the-art program
- My course of action after management turned down our original plan
- Equipment employed in a lean oil analysis program
- Current program
What is the purpose of an oil analysis program?
In my opinion, reliability is the No. 1 reason we perform predictive maintenance. Uptime is the only way to compete in today’s highly competitive world. Detecting problems and preventing failures are ways to get the most uptime possible from our equipment. Along with uptime, reducing cost is also important to the profitability of any company.
If an equipment problem can be detected early, it can be scheduled for repair or replacement before it causes expensive downtime or equipment damage. The ultimate goal would be to run each component as long as possible and be able to predict in advance when it needs to be changed. This also includes the oil. More and more, the oil is becoming a very expensive component of any piece of equipment; getting the longest life you can out of oil is no different than a bearing or a gear.
Cost of a predictive maintenance program also adds to production costs and is scrutinized more than other expenses, as it is not looked at as being directly related to production. Unlike vibration and thermography, oil analysis usually requires an outside lab to perform the tests for analyzing the samples.
It is imperative to show success early and it must be communicated quickly not only to management but also to production and maintenance. Getting support from production and maintenance will go a long way in selling management on spending money for the program.
So if you are a small company with not a lot of capital to work with, a larger company dealing with cost control, no support of the predictive maintenance by management or, in some cases, there is a combination of issues that keep you from starting or maintaining a predictive maintenance program, success can be achieved with a little determination and a little thinking outside the box.
To start with, I will give you a little history on how I had to set up a lean oil analysis program, what led to it, how it progressed and the success achieved.
Our attempt at a world-class program
In my case, the problems kept changing as our company grew and then was sold twice. At the beginning, we were set up to be a fully cross-craft maintenance, and every technician would be an expert in every aspect of maintenance, including predictive. Everyone was given some basic training on vibration, alignment and oil analysis. It was very evident to us that only certain techs were interested in each of the disciplines, but everyone was expected to complete whatever work order they were given.
This produced very erratic trending and even worse analysis of the data. Many motors, bearings and reducers were diagnosed incorrectly, wasting labor, materials and reducing reliability. Management was still sold on having everyone as an expert in every discipline of maintenance. To achieve this, they planned to send two techs at a time to training. Fortunately, the first two sent to vibration as well as the two sent to oil analysis training were passionate about the process.
They took ownership of each of the programs and were able to achieve some early success, but no one was allowed to be a dedicated predictive maintenance tech; we still had every maintenance tech collecting data and doing the analysis. Whenever there was an alarm condition, the reply was, “Change the oil,” “Change the motor,” or “Run it and watch it.”
The change began when two of the people picked for the original training – one oil analysis and one vibration – decided to take matters into their own hands. Thinking back to what made us do this behind management’s back, it had to be a passion for the predictive maintenance process, or maybe just the thrill of getting away with something.
Some of the original group trained in oil analysis and vibration lost interest in the programs because management wasn’t going to invest in the equipment needed or staff the program full time. Even after putting together a proposal that showed all the benefits and payback of a full-fledged program, management maintained their philosophy of a full cross-craft maintenance department with no specialists.
Figure 1. Before Picture of Clarion Boards' Oil Room
Change of plans
Another train of thought was to go slow and convince management through results. The methods used were a little different and required some risk, going behind the back of management, but they had encouraged us to be a self-directed workforce. All techs at our mill were on-shift and worked 12-hour rotating shifts. Management works straight days and no weekends, which left us to manage ourselves nights and weekends.
This gave us a great opportunity to get our oil analysis programs set up using non-traditional means. I would get my scheduled work done as quickly as possible or recruit the other techs on my shift to help out with the scheduled work so I could spend a little time each shift on the setup of the program. I also volunteered to perform all oil change preventive maintenance (PM) tasks on down days. This provided me the opportunity to design and install oil sampling ports on all of our equipment.
During this process, we found some support from our corporate office. We started asking questions of the industrial training department, which sparked some interest in what we were doing, and questions were asked of our supervisors about progress. For example, they wanted to know how many sampling points we had for our vibration and how many sampling ports were installed on equipment for oil analysis.
When my supervisor was given a pat on the back for having 150 sampling ports installed in equipment, he was surprised and confused and wanted to know how this was achieved without him knowing. After seeing the interest corporate showed, he began the process of dedicating a couple of techs to the predictive maintenance process. He ran into the same resistance with mill management that we had in the past (no specialist), but because pressure was being applied from corporate, his proposal was pushed through, with some changes.
The plan agreed on by the managers at our facility was a three-month, three-person team to work day shift, to set up and start the PdM program. After three months, three more techs would be brought off-shift, and they would continue with the program. This rotation would continue with our entire maintenance staff. Only three people applied for the positions; the rest knew that management was only doing this because of corporate pressure and would not give the program support needed to succeed.
After accepting the position and listening to the rules and restrictions, we went to work developing the program with one goal in mind – no matter what obstacles they gave us, we would succeed.
We were told right away that there would be no money for the PdM program. We had to use the equipment and resources we already had. Our first goal was to use what tools we had to show success as quickly as we could. Working with the oil supplier, which gave us free oil testing (which turned out to be worth exactly what we paid for), I spent my time working on perfecting the data-collection process.
Keeping the samples clean and getting them to the lab quickly gave me somewhat of a stable trend on most of the equipment. Having one person collect all the data gave us a more stable trend as opposed to having every maintenance tech collect the data. On most of the equipment, I was able to get a nice trend except for the lab deviations – the free oil-testing thing. I’ll get into that a little later.
My next step was to develop a report where we could show all of our success and savings for the company. I used very conservative figures when estimating the money saved or downtime averted. I would make sure the report was sent to management as well as maintenance and process techs. To promote the program, I also forwarded the reports to the industrial training center at our corporate headquarters, which, with their help, went on up the ladder. This created some issues with our plant management, but it secured our place because they could not justify shutting us down.
One of the quickest ways to show a savings turned out to be a benefit from having so many sampling ports installed in our equipment. Every reducer, from the largest to the smallest, as well as every hydraulic and lube system had a sampling port installed. Samples could be taken while the equipment was running. I was able to set up all of this equipment for condition-based oil changes. The OEM-recommended oil changes for the majority of our hydraulic system came due about this same time.
Using the lab results, I was able to show that all of the hydraulic oil in the systems was as good as new. The total oil for these systems was more than 900 gallons. To this day, 11 years after startup, we are still running with the original fill on the hydraulic systems. Going to condition-based oil changes reduced our oil consumption by about 70 percent in the first year.
The oil storage room became my room as no one else wanted to take ownership of the mess. We had a separate building attached to the side of our plant just for storing our oil. This room became a hiding place for everything messy. Some of our systems produced a lot of waste oil contaminated with wood fiber as part of the process. This waste along with other waste oil was everywhere in the storage building, along with our new oil and containers used to fill systems. I had to take charge of the oil room if I was going to have any success with the oil analysis program.
One of our sister mills had an oil storage system that consisted of storage tanks built into a nice racking system with hoses and pumps to transfer and keep the oils clean. My purchase request for this system was turned down, so I set out to use what we had and, using some ideas from Noria training, designed my own storage system. Adding legs to the drum rack system we had, I set out to clean up the oil storage room.
I was able to purchase a new waste oil tank as well as some storage cabinets and over time purchased dedicated oil transfer containers. The finished oil room (Figure 2) eventually became the standard for the entire company, including our sister mill. They had to give up their fancy storage system and replace it with this system.
Figure 2. Oil Room After Taking Control
Next, I set my sights on improving sampling, testing and analysis. I had approximately 100 samples to take each month to keep a close watch on our equipment and to manage the condition-based oil changes of all our equipment. This meant that we would run out of our free samples in about five months. I projected out what it would then cost to continue the program for the other seven months of the year.
Particle count testing was not part of the free sample deal, and there would be a charge for this test to be added to the package for all samples. As I mentioned earlier, our free lab service we had with our oil supplier was worth exactly what we paid for it. Now we were going to have to pay for the tests, particle count for the first 500 and then full price for all samples after that. I needed to find out if the lab service they offered was going to be worth it.
Having all the data collected by one person, the trending started to level out, but I was still seeing test results at times that were all over the place. Unable to contact the lab, except through our oil representative, I decided to run a simple test to see how reliable the results were that we were getting from the lab. After pulling enough oil from a new drum of oil to make four samples, I sent them into the lab for testing.
Before separating the oil into four bottles, I thoroughly agitated the oil. The results I got back were all different. Particle counts, viscosity and additives results were all over the place. I ran this same test in qualifying an independent lab. I picked the lab with the best repeatability.
Still not having a budget to work with, I put together a proposal that would get us some in-house testing, along with support of an independent lab with very little investment. I compared the cost of a:
- Full in-house lab with all the necessary equipment
- An independent lab doing all the lab work
- Our current system projecting out the fact that we would run through our free samples half way through the year
These all turned out to be very expensive and were all turned down by management. I started looking for alternatives.
Lean equipment
If I could come up with a way to do some in-house testing and only use an outside lab for very critical and questionable samples, I would get more useful data at a lower cost. The criteria I set for my in-house test equipment was repeatability, ease of use and being able to perform tests quickly. Repeatability would be the biggest factor. Knowing that every test was accurate was a must. The three tests I felt were needed to have an effective in-house program were viscosity, particle count and water.
Viscosity
Viscosity can be measured using a visgage, a handheld unit with two tubes each containing a steel ball. One of the tubes is filled with a reference fluid; the other can be filled with the fluid to be tested. After tipping the gauge to get the balls to the one end, the gauge is held at a 45-degree angle until one of the balls reaches the end of the gauge scale; the other ball will indicate the viscosity of the fluid.
When sending out a sample to the lab, I would use the visgage and record the data and compare it with the test results from the lab. I was surprised how accurate the visgage was with a little practice.
Figure 3. Two visgages were purchased through an online auction – one in centistokes and the other in Saybolt seconds.
Patch test
After reading an article about patch tests, I decided to look into what equipment was needed, how accurate the tests were and if the results were repeatable. I also needed a way to trend data viewed in the patch. I found a microscope on the Internet that had a digital camera that connected to a personal computer. With the camera attachment, I was able to save the patch images and trend any changes.
I also found that a top light is necessary to see and identify particles on the patch. A small handheld magnet moved alongside the microscope would make the ferrous metals dance. Using the top and the bottom lights and either the 100 times or 400 times lenses helps to identify the type of wear.
Before testing a sample, it needs to be agitated. I found very early on that the proper agitation of the sample makes a big difference in the accuracy and repeatability of the tests. I priced commercial agitators and found them to be quite expensive. Our vibration tech made a vibration training station from a discarded reducer and an old motor. The output of the reducer turned very slow, attaching a wheel to hold the sample bottles; the slow rotation agitated the samples as well as any vibrating shaker.
The patch test became the backbone of my program. I used the patch to check the sample for contamination, wear debris and to perform a rudimentary particle count. Using the digital image to store and trend the collected data made it easier to detect a change in the equipment condition. If something out of the ordinary is observed, then the sample can be sent to the lab. Because the patch test uses so little of the sample, there is still enough left to send to a lab for further testing and analysis.
There are patch test atlases available to assist in the identifying of contamination and wear debris. Actual images of the different types of wear debris can help you identify what you are seeing in the microscope. To get a feel for estimating the particle content of a fluid, I would send the sample off to the lab and compare my estimate to the actual from the lab.
Figure 4.
I found two methods to make patches. One consisted of a funnel-shaped patch holder that used gravity or a vacuum to run the fluid through the patch. This worked well but had several issues: time, cleanup and exposure.
Using gravity to get the fluid through the patch took time and was very dependent on having the right amount of thinning fluid added to the sample to make it thin enough to go through the patch. Cleaning the funnel between tests not only required time but could also affect the next sample if any residue is left. Pouring, mixing and the time the sample is exposed to the air can affect patch results.
The second method, using a syringe with a two-way check valve, solved all of the issues I had with the funnel method. With the two-way check valve, I can draw up the right amount of oil and then thin fluid in the syringe as well as push it through the patch with minimal exposure to the atmosphere. Cleaning the syringe is very easy and quick, in addition to purging all fluid and contamination quickly using the same method. It only takes a few minutes to create a patch ready for analysis.
Figure 5. This bottle agitator was built in-house using discarded parts.
Moisture test
Testing oil for water can also be simply done in-house. Water in the systems I test in-house is not as critical as those I send to the lab. Small reducers running under normal load can handle a small amount of moisture without too much trouble. However, for reliability checking to make sure moisture is not an issue, I use the crackle test.
A couple drops of oil placed on a hot plate set to the right temperature will give you a quick check for the presence of water. Having a magnifying light over the hot plate not only protects you from the hot oil but also gives you a better view of the test. I also have used this in emergency tests for our critical equipment to test for a cooling water leak.
The in-house test
A typical oil sample would go through the following steps after collection:
Visual test: Look at the color and clarity of the oil. For this purpose, I use clear bottles only. I have a rack of new oil samples handy for comparison and record any change in color. Loss of clarity can indicate contamination by water, wear particles, dirt or wrong top off oil.
Smell test: This can reveal issues with contamination, oxidation and varnish. Samples of new oil come in handy for this test as well.
Viscosity: Use the visgage to test the viscosity and record the data.
Crackle test: Deposit a couple of drops from the visgage unto the hot plate and check for water in the oil.
Patch test: Produce a patch and analyze. Check for ferrous metals, using a magnet, and record the amount and size of particles. Look for and record the amount of other contaminants on the patch. Save the image to a database for trending.
Report: This is probably one of the most important parts of keeping the program running. Reporting findings and successes will generate a lot of interest in the program. Keep reports short and to the point. Usually only the first page of a report gets read, so try to keep it to one page and cover your successes. I found that sending the reports to management to process helps in keeping everyone aware of the success of the program.
Starting over
Shortly after getting everything working well and getting experience with the equipment, we were shut down. Market issues caused the shutdown, which lasted 18 months. When we were finally sold, half of the maintenance techs did not return. In September 2004, we restarted the mill; and to this day, we are still trying to restaff our maintenance department. Again, I have to start over-selling the importance of oil analysis to management.
Figure 6. Patch Holder, Two-way Valve and Syringe for Making Quick and Reliable Patches
Finding the right person for the job is key to success. To make it work in a lean environment requires someone who is dedicated and has a passion for the process of oil analysis. Currently, I am still looking for the right person to fill this position – someone who is willing to take ownership of the oil storage, take charge of the setting up the sampling, testing and reporting as well as someone who can think outside the box.
Figure 7. Hot Plate for Crackle Tests
About the author:
Dave Lander is the mechanical maintenance supervisor at Clarion Boards Inc. in Lucinda, Pa. Dave is a lifelong resident of, Lucinda, a small town in western Pennsylvania, located in heart of the hardwood lumber industry. Dave spent 22 years working in saw mills, where he came to believe sawdust was an oil additive. The past 12 years have been spent in the panel products industry making medium-density fiberboard at Clarion Boards. He has a Machine Lubricant Analyst Level II certification through the International Council for Machinery Lubrication and is a volunteer on ICML’s test-writing committee.
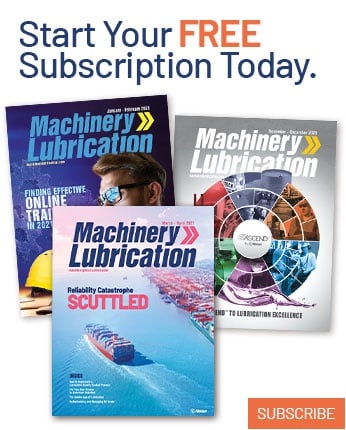