Trying to save energy dollars is not always as simple as it seems. Installing variable frequency drives (VFDs) and retrofitting lighting systems are two of the quickest and most widely accepted ways to achieve significant energy savings. Yet, new problems may surface as a result.
One of the first steps in solving these problems is to understand that the energy-efficient devices themselves may be the cause. While most energy-saving electronic lighting ballasts, lighting controls and
VFDs work just fine on modern electrical distribution systems, this equipment can create troubleshooting nightmares in older facilities.
Electrical problems resulting from high-efficiency, energy-savings upgrades fall into one or more of three areas:
- Application
- Installation (including startup)
- Maintenance
VFD mismatches
One of the most common energy-saving applications in facilities is to use VFDs on centrifugal pumps, fans and blowers. Varying motor speeds is a much more efficient way to control flow rates and, thereby, maintain water temperatures than to run the motor and pump at full speed and throttle a valve to adjust flow rates. But problems will result if:
- The VFD has not been properly sized and selected
- The drive and motor installation was not done with a VFD in mind
- Parameters were not properly set at startup
- The effects of harmonic currents were not considered in design and addressed in maintenance
The non-linear effect of electronic loads
Variable frequency drives are complex electronic devices called non-linear loads that vary their output voltage and frequency to control motor speed. The distribution system supplies voltage, however current does not flow into the VFD until the rectifier circuit in the converter section begins to conduct. Since current does not flow linearly as voltage is applied, the equipment is called “non-linear.”
When the diodes suddenly allow current flow, it creates a “notch” on the sine wave that causes sine wave distortion. The VFD rectifier circuit also causes currents to flow back into the distribution system in multiples of 60 hertz (Hz). Current that flows back in multiples of the fundamental is called harmonic current. The third harmonic is three times the fundamental of 60 Hz, or 180 Hz. The fifth harmonic current is at 300 Hz, and so on.
Harmonics
These harmonic currents not only tend to distort voltage throughout the plant, but certain harmonic frequencies create problems unique to that harmonic. For example, the third harmonic causes overheating in neutral conductors and transformers. The fifth harmonic can cause motor issues, such as overheating, abnormal noise and vibrations, and motor inefficiency.
The bottom line: All electronic equipment creates harmonics and distorts the voltage distributed in-plant.
Other typical non-linear loads added during energy upgrades include electronic ballasts, computers, controls (PLCs, etc.), and various components of building automation systems. Always use a true-rms responding test tool when measuring non-linear loads, especially current. For a backgrounder on why true-rms, visit www.fluke.com/true-rms.
Sensitive controls
Here is the root cause of the problem: Modern control systems are quite often sensitive to any quality problems with the electrical power they are supplied. That means non-linear, high-efficiency loads create operational problems not only with other sensitive plant equipment, but with themselves as well. Ironically, the very equipment installed to save energy often causes inefficiencies and unexpected maintenance costs.
Fortunately, some quick checks and basic electrical troubleshooting can resolve many problems.
VFD troubleshooting examples
Poor motor speed control and/or nuisance trips: For example, a typical VFD problem encountered in the field is that the drive fails to control motor speed properly and may even experience nuisance trips. The two mostly likely causes of this particular problem:
- Voltage unbalance on the three phases supplying the drive
- Harmonics flowing out of the drive, back into the distribution system
For example, a chiller with a VFD installed may experience temperature control problems at specified locations in the system due to distorted sine waves created by the harmonics. This distortion affects the operation of PLCs, temperature controllers and other controls in the chiller.
Another possibility: If tachometer feedback cables are not properly selected and installed, erroneous motor speed information will be fed back into the VFD, making it impossible for the VFD to control real motor speed.
The solution: Run shielded cable for these low-voltage signals and ground only at one end.
When routing these low-voltage conductors, ensure they are not installed close to power conductors. Electromagnetic induction from power cables can affect low-voltage control.
Installation checks: To troubleshoot VFD control problems, first review the installation design. Chances are that the proper drive, motor and associated equipment were selected – but verify anyhow. Walk down and observe the installation. Were correct cable types selected and installed properly? Is the installation suitable for the environment in which it is installed? Are enclosures free of dust and adequate ventilation provided?
Drive parameter checks: Review the parameters programmed into the drive. Does the data entered match the motor nameplate? Has the drive been set for proper operation, such as variable torque for energy-saving pump and fan applications? If the VFD is not controlling the motor as expected, it could be because operational parameters were either not set correctly or, more than likely, were reset by some well-meaning individual attempting to correct other problems.
Quick measurement checks: Measure VFD input voltage with a true-rms digital multimeter, verifying voltage unbalance falls within manufacturer’s specifications. Measure harmonic frequencies and levels at the point where power is supplied into the VFD, using a power quality clamp meter or power quality analyzer. Also, check for harmonics back at the feeder where the power to the VFD is also supplying other loads.
The solution: If voltage unbalance is the problem, shift and evenly distribute single-phase loads. If harmonics are found to be the cause, contact the drive manufacturer or a harmonic filter manufacturer and determine and install a properly tuned harmonic filter.
Problems with lighting retrofits
Nuisance tripping: Without a doubt, lighting retrofits save money on the monthly electric utility bill. But many facilities invest in lighting upgrades only to find lights flickering or not operating at all. Seemingly unrelated, three-phase motors overheat, servers and computers malfunction, and data is lost. Nuisance trips on circuit breakers suddenly begin occurring. Newly installed electronic equipment mysteriously trips on overvoltage or overtemperature – yet the equipment does not show any signs of such abnormal conditions.
Such problems are generally associated with harmonics. One IEEE study indicates that these harmonics can become a significant issue if fluorescent lighting comprises 25 percent or more of the facility load.
Electronic ballasts often introduce harmonic currents back into the distribution system. If the facility is an older one and only one neutral wire was pulled in for each of the three ungrounded phase conductors to the lighting circuit (sharing neutrals), the result may be overheating neutral conductors, panelboards and transformers. Maintenance often finds and corrects these problems.
A tip: Pull-in additional neutral conductors, one per phase total as needed. Infrared thermography can often identify these issues before failure.
Dimmer controls: Common retrofits to T-8 lamps with electronic ballasts and the replacement of incandescent lamps with compact fluorescents (CFLs) both create significant energy savings. For additional energy savings, dim the fluorescent lighting when full light output is not needed. This dimming can be achieved with manual dimmers or with photosensors that sense light level either indoors or outdoors as required.
Make sure to match the proper type of dimmer control with the ballast and lamp type to be dimmed. Mismatches here can result not only in improperly operating equipment, but in damaged lighting system components, as well.
Depending on the type of dimming controls used, additional control wiring operating at zero to 10 volts may be installed. Placing such control wiring too close to power conductors during installation or maintenance can result in erratic lighting control.
A tip: Keep control wiring as short as possible during installation.
Automated lighting controls that switch lighting banks off and on erratically after the installation of energy-saving controls should be checked for proper sensor operation. Some photo sensors may have a deadband adjustment available to change the time between lights-off and lights-on.
Overheating motors: As part of the energy savings lighting upgrades, banks of lighting may be switched to save energy. Depending on the circuits switched, phase unbalances could result on three-phase systems. Maintenance gets the call to replace motors that have been destroyed by overheating.
A tip: Check the voltage supplied to the motor during all phases of plant operation.
Maximum voltage unbalance at motor terminals should not exceed 1 percent. Operation of a motor at greater than 5 percent unbalance will probably result in motor damage.
Conclusion
The best tool for solving problems, after an upgrade, is a well-trained and properly equipped workforce. Knowledge of how the energy-saving application works is the first step in solving associated problems. Review the design, installation and any startup procedures to isolate and correct many problems. As maintenance on the equipment is required, use a logical, systematic approach with the right tools to isolate problems.
Review Figure 1 for typical problems encountered after energy-saving upgrades and for ideas on where to get started.
For more information, visit the Fluke Corporation Web site at www.fluke.com.
Figure 1. Typical problems reported after energy upgrades and some quick checks to resolve issues.
Figure 2. To preserve your energy upgrade savings, learn to troubleshoot and repair associated problems in-house.
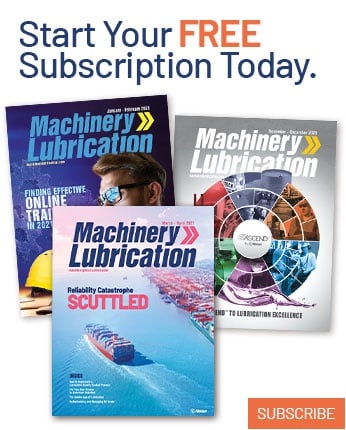