Many times in my manufacturing career, I have struggled when dealing with the dilemma of producing “the cats and dogs.” The cats and dogs are those parts or products that are typically small volume, hard to make, less profitable or generally a royal pain that cause us headaches and disrupt the harmony in our manufacturing flow.
Since our lean manufacturing focus is to improve flow, how do we deal with our cats and dogs?
Do we outsource our cats and dogs so we can maximize our internal efficiency by producing only our high runners? Do we discontinue making the cats and dogs entirely if they are not profitable? Do we outsource some of our high runners to work on the cats and dogs? Do we separate the cats and dogs from the rest of the pack?
It would be easy for us to take the path of least resistance and either outsource them or drop them from our product offering. Life is too short, so why struggle with the headaches day after day. With our short-term thinking and pressure for quick results, we can present convincing arguments to get rid of these cats and dogs and do it fast. Especially if we are not making any money on them, it should be a slam dunk to get rid of them. Let’s just focus on our core competency and we will be more profitable.
That sounds logical, right?
From my experience, I do not completely trust our accounting systems in determining the profitability of individual parts or products. With the typical standard cost method, erroneous data, estimated inputs based on some formula or, worse, some average and our sometimes strange allocation of costs, how can we really make good decisions on true profitability on a part-by-part basis? Just take a stopwatch to gemba and do a simple random audit to see that our data is as reliable and trustworthy as a celebrity in rehab.
If we outsource these cats and dogs, passing the headache on to others to deal with, we will only add additional waste to our overall process. We will need to increase our efforts to insure the quality of these parts now on the outside, increase our inventory levels to protect our delivery to our customers and most likely soon end up paying more for these parts. Before long, we will end up dropping them because they will be deemed unprofitable.
In the book, “The Birth of Lean”, Taiichi Ohno faced the same dilemma at Toyota. His thoughts on this issue were described as follows: “A lot of people in the company thought that we should outsource small-volume parts to low-cost contractors and make the large-volume parts on our own, like bicycle manufacturers did. They figured that we could build an export business by getting the contractors to supply parts on a just-in-time basis and by assembling vehicles from those parts and from the parts that we made in-house. I argued for taking the opposite approach. I insisted that we should produce low-volume items in-house and buy large-volume parts – stuff that anyone could make inexpensively – from outside suppliers. Making the low-volume parts in-house would mean high unit costs, and that would pressure us to tackle kaizen improvements and cost reductions.”
What a great viewpoint, to send out the easier, high-volume parts and keep the hard ones in-house to pressure our kaizen efforts. Think about that for a moment. Do we trust outside suppliers to kaizen better than we can internally? Do easy, high-volume parts present the same kaizen opportunities that low-running parts provide? Which would challenge us to be better problem-solvers? As for our customers, which kinds of products are growing in demand: the generic, high-volume products or the custom, low-volume products? How about the trend in the future?
What do you think?
About the author:
Mike Wroblewski started his lean journey with instruction in quick die change from Shigeo Shingo. Mike is currently a senior operations consultant for Gemba Consulting North America LLC. He also writes a blog called “Got Boondoggle?” featuring lean and Six Sigma topics. You may contact Mike via e-mail at MWroblewski@gemba.com.
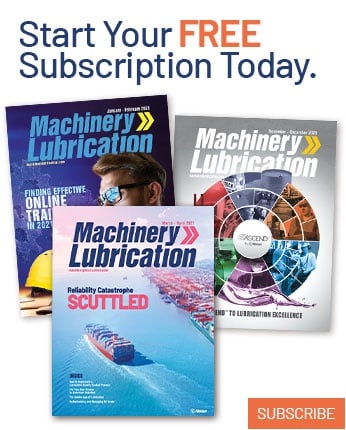