Have you heard the one about the guys that burned up a brand new piece of rotating equipment because it was installed with no oil in it? That little oversight cost $80,000 for a replacement when proper lubrication would have cost less than $100. How about the guys that cut a section out of their raw material feeder line, and then found out that the replacement piece was just a wee bit too short to fit in the gap? That mistake cost thousands of dollars in unplanned repairs, and potentially hundreds of thousands in lost production!
Engineers, buyers and others often go to great lengths and significant expense to design and purchase new equipment, critical spares or other key maintenance, repair and operations (MRO) materials. Yet many times, a critical element of the procurement process – quality assurance – is overlooked or sub-optimized.
Sure, receiving personnel perform a cursory inspection of many incoming materials, but that’s mainly for the purpose of verifying count, reconciling paperwork or making sure that if an item is supposed to be a kafloogle, then it actually is a kafloogle – or at least looks like one. Often that’s not sufficient to ensure safe and reliable installation, operation and maintenance of your assets. Plus, even when some form of purchased material inspection (PMI) is called for, the internal practices and system infrastructure are often inadequate to perform effective inspection and track the material through the process.
This article outlines some steps to consider to ensure that you have an effective quality assurance (QA) process in place for your MRO materials.
Clearly identify the affected items
This is easier said than done. Corporate and/or site policies and procedures will sometimes provide general guidance on the types of items to be inspected based on criticality or other criteria. But this information may be incomplete or out of date, and often does not identify the specific part numbers affected. Engineering is also a key source of technical specifications on items such as project materials and new spare parts. Manufacturers and vendors also may be required to test certain aspects of quality before shipping particular materials and provide documentation showing that they meet specifications. In many cases, it is recommended, if not required, that this documentation be reviewed or even independently verified before incoming materials are accepted.
Whether you ultimately identify just one item that requires inspection or 1,000, the best way to manage PMI is to have each one of them clearly flagged in the computerized maintenance management system (CMMS) or enterprise asset management (EAM) system at the part level so that everyone knows which ones require inspection on arrival.
Communicate to purchasing, vendors and receiving
PMI requirements should be delineated in any purchase requisition and passed along to the associated purchase order. This is key information that the buyer may need to include on a request for quotation (RFQ) or even on a confirming purchase order so the vendor knows exactly what is expected of it before it ships, or at least what you will be looking for upon receipt. Simply passing an “inspection required” flag or even some kind of inspection code from your CMMS/EAM may be sufficient or at least helpful internally. With or without this information, however, it’s a good idea to clearly state somewhere in the body of the purchase order the type of PMI that will be performed (e.g. dimensional check, material verification, chemical analysis, documentation check, etc.) as well as the specific parameters and tolerances that will determine whether the material is acceptable.
Most important is to make sure that when an item arrives at your dock, your receiving personnel can easily determine whether or not it needs some kind of inspection. This will eliminate questions, minimize delays in processing, and make sure that purchased materials meet incoming inspection requirements before being stocked, delivered or, most importantly, installed.
Use properly skilled inspectors
A common pitfall in many operations is to rely on the ever-popular “end-user inspection” for quality assurance. While this practice may be appropriate for routine supplies, it does not assure quality – or anything else, for that matter – and should be discouraged for MRO materials. There is no way to determine if the “end-user” is the right person to be performing the inspection, if that person knows what to look for, or if they have even done any inspection on the material at all.
Another common practice is to place the responsibility for checking incoming materials squarely on the shoulders of the receiving department. While this improves the chances that some inspection may be performed before the material is released, it also provides no assurance that the right people are looking at the right things. For example, properly trained receiving personnel should be able to use a micrometer for taking basic measurements or verify vendor/manufacturer provided documentation. But some items may require laboratory analysis or evaluation by engineers or skilled maintenance employees to determine if they are within specifications.
Rather than placing the entire burden on receiving to identify and complete the required inspection (which in many cases is unfair at best, and dangerous at worst), it is more appropriate to simply alert receiving personnel via the purchase order and/or CMMS/EAM that someone (maybe receiving, maybe not) needs to take additional action to verify the specifications of the item before it is accepted. Who the right person is depends on the type of inspection required and the skills of different individuals, and should be spelled out in PMI procedures.
Don’t leave pass/fail decisions to chance
Clearly define inspection requirements. What are we checking for? What tools are required? What additional information is needed? All this should be spelled out prior to initiating the inspection.
Ensure that any allowable tolerances are specified. If an item is supposed to be a foot in length, is 11.5 inches long enough? Is 12.25 inches too much? Are there standards or go/no-go gauges to compare to? There should be no question whether an item meets acceptable criteria.
Most importantly, make certain that all inspection information is captured in written documents that have appropriate content and revision controls. Make sure that all purchase orders reference the specific document (by title, date and revision) that will be used as the basis for the inspection.
Document non-conforming items
Any item that fails to meet the specified quality standards should be held for resolution and disposition, and discrepancies should be documented immediately. If a decision is made to reject the material, it should be returned to the vendor through a best-practice “return to vendor” process. If the material will be accepted in spite of the quality issue, the vendor should be notified. A record of the non-conformance should be issued describing what was wrong with the material, why it was accepted and the potential impact that the nonconformance could have downstream (if any).
Track material through the process
Some CMMS/EAM systems provide the capability to track material through the PMI process. In an ideal world, the system would be able to track material through receiving, into and out of inspection, and into the storeroom or onto its final destination without ever losing visibility to it. It would also allow for the possibility of destructive testing, accounting for a portion of the material being consumed in the inspection process itself. This isn’t always possible, so at the very least, the system should prevent PMI material from showing as available inventory until the inspection is complete and it is deemed to be acceptable.
Measure the effectiveness of your process
The primary purpose of PMI is to ensure that your materials are usable. However, a robust PMI process will also provide the capability to measure and manage vendor performance. If you find that you have vendors who continually send you non-conforming material, maybe you should consider an alternative supplier. If you find that a particular vendor always or consistently meets specifications, maybe you don’t need to inspect their materials as often.
Don’t be penny-wise and pound foolish
Granted, maybe not too many MRO items require this kind of attention. But the ones that do are usually expensive, possibly custom-made, with long lead times, and they can have a significant negative impact on your operation if not handled properly, as evidenced by the examples cited above. Don’t assume you have no materials to which this applies. Carefully evaluate all of your MRO items, and if even one requires some kind of incoming quality assurance, it is worth the time, effort and expense to establish a robust process up front rather than suffer the consequences of being unprepared.
This article first appeared in the April edition of Life Cycle Engineering’s RxToday.
About the author:
Doug Wallace is a materials management subject matter expert for Life Cycle Engineering (LCE), a consultancy based in Charleston, S.C. Doug has more than 20 years of practical supply chain management experience in the semiconductor industry, including positions in production control, shipping/receiving, incoming inspection, finished goods and spare part warehouse management, material planning, customer service, global capacity planning, and global production planning. For the past eight years, Doug has provided materials management education, training and consulting services to clients in a variety of different industries. Doug can be reached at dwallace@LCE.com. For additional information, visit www.LCE.comor call 843-744-7110.
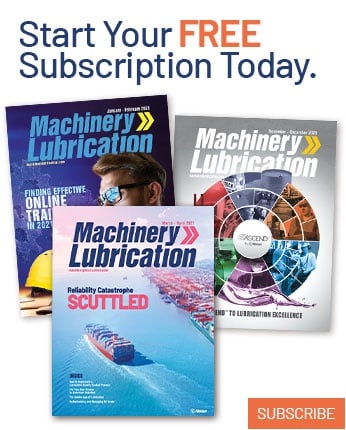