At Alpenrose Dairy in Portland, Ore., operators process the raw milk into a dozen varieties of milk, six cultured products (cottage cheese and sour cream) and 31 flavors of ice cream. It’s a challenge to keep the complex Alpenrose production facility, with its hundreds of motors, pumps and gearboxes, running butter-smooth. But thanks to the new Fluke 810 Vibration Tester, it’s easier today to maintain Alpenrose as the cream of the crop.
This isn’t your average dairy. Family owned and operated since 1916, Alpenrose Dairy Inc. has evolved over time into a community entertainment center that includes Alpenrose Stadium, Dairyville, a replica of a western frontier town, a 600-seat opera house, a Quarter Midget racing arena and an Olympic-style bicycle track.
The hub of this high-profile enterprise is the production plant, churning out dairy products that get to market the day they left the farm. Maintenance manager Eric Trummel and maintenance technician and electric motor expert Todd Toburen keep their fingers on the pulse of the plant.
In the U.S. Navy, Toburen learned vibration analysis to find and diagnose electric motor problems. “We would take our readings and send the data to Annapolis. Annapolis would compile tons of data bouncing off of different frequencies and give us a call back to tell us whether it was good or bad,” Toburen said. “We would rewind and rebuild the motor and retest it, just to make sure what we sent out to the fleet was a good piece of equipment.”
Pumps, motors, gearboxes and more
In his five years at Alpenrose, Toburen has taken charge of the hundreds of pumps, motors, gearboxes, compressors and other equipment required to operate a midsize dairy plant.
“We’ve got equipment here that if it goes down, processing stops,” he said. “If the bad part is a high-dollar item, we don’t have sitting on the shelf. We could be down for a couple of days.”
In the dairy business, where fresh products are essential, such an outage is a non-starter.
To prevent such incidents, Alpenrose manages a more proactive maintenance program to help understand when a motor or machine may encounter problems.
“Our biggest concerns are the pieces of equipment that are critical to the processes,” he said. “If we see that there’s deterioration in the bearings or what have you, we’ll be able to schedule the downtime to take care of that problem.”
But accuracy is key. Trummel recalls an incident when a vibration analysis contractor doing a semiannual check warned of bearing deterioration in an important air compressor.
“He claimed that one of the bearings had gone bad, and that we needed to take care of it in the next couple of months,” Trummel said. “The next week, the coupling on the compressor disintegrated. The air compressor went down, and it represented a limitation of the plant. That’s when I realized these guys may not know what they’re doing. This is why this Fluke 810 is relevant to us. It’s good to have this capability in-house and check this equipment every couple of weeks. We get a better idea and a better feel for what’s going on.”
The handheld Fluke 810 is designed for maintenance professionals who need to troubleshoot mechanical problems and quickly understand the root cause of equipment condition. It’s programmed to diagnose the most common mechanical problems of unbalance, looseness, misalignment and bearing failures in a wide variety of mechanical equipment, including motors, fans, gearboxes, couplings, pumps, compressors and more.
The diagnostic technology in the Fluke 810 analyzes machinery condition and identifies faults by comparing vibration data to an extensive set of rules and algorithms developed over years of field experience. The Fluke 810 is not merely a vibration detector, but a complete diagnostic and problem-solving solution.
“Using the Fluke, we’re able to take a reading once a week or once a month” said Toburen. “If we notice something different, we can build a trend analysis with that data. If we notice there’s a change in our frequencies, that’s something we need to look at. Of course, we won’t be able every single month to do every piece of equipment here at the dairy. We’ll prioritize what equipment we want to check on a monthly or a quarterly basis, and I’m basing that on what my baseline reading is.”
‘The diagnosis was right on’
Machine operators form an important early warning system. If a machine doesn’t feel or sound right to them, Toburen troubleshoots the equipment with the Fluke 810 to see exactly what’s going on.
“The nice thing with this is you’re able to tell, ‘Is it the gearbox? Is it the compressor? Is it the motor? Is it the drive end? Is it the off end?’ It even breaks it down to if you have a loose coupling or not,” he said.
The Fluke 810 also rates the level of severity of any problems it finds.
“It has four different levels,” Toburen said. “Green being slight, yellow being moderate, orange being serious and red being extreme.”
But Toburen said it took some checking to fully trust the opinions of the Fluke 810.
“I had to develop a comfort level with the Fluke’s interpretation,” he said. “I’ve done quite a bit of that. Somebody would come up and say they had a real loud motor. I’d go out and take a vibration analysis on it, and each time I’ve done that it’s come back as ‘extreme.’ The Fluke will actually give you ‘loose bearing’ or ‘bearing wear’ – it will give you the diagnosis. I’ve taken the motors apart, and each time I’ve done it, the diagnosis was right on. Then I’d also rebuild the motor, throw it on the workbench, put the 810 back on it and it comes back as either ‘no problem detected’ or ‘slight wear or vibration.’”
Has the Fluke 810 saved money?
“I don’t know,” said Toburen. “But being able to say there’s something wrong with our equipment, troubleshoot that, get the parts on order, repair it in our downtime and bring it back up online – it’s almost priceless. If you don’t have that part on the shelf it could be two days out, and you’re not doing any processing. The amount you can save? It could be significant.”
For more information, visit the Fluke Corporation Web site at www.fluke.com.
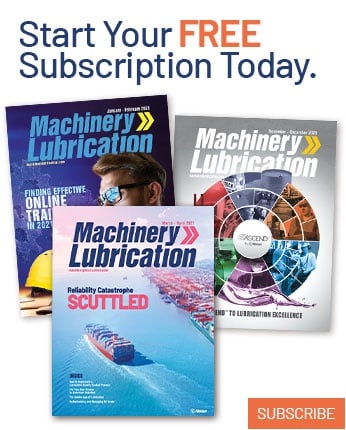