The University of Dayton Research Institute has been awarded $270,000 in Ohio Third Frontier funds for research to design and test structures and materials for composite wind-turbine towers – fiberglass reinforced resin monoliths that will stand as much as 65 feet taller than the steel towers currently dotting wind farms around the world.
In finished form, the average utility-grade tower height is about 80 meters, roughly 265 feet. But the wind industry has been setting its sights on a new standard for tower height at 100 meters (328 feet) Putting larger turbines atop taller towers facilitates access to greater wind speeds, which improves operating performance and cost. As the size of wind turbines continues to grow, however, so grow the problems and expense associated with transporting and building the towers.
“The U.S. Department of Energy has reported that by 2030, twenty percent of all electricity generated in the U.S. could be supplied by wind. But a number of design and material advancements need to be made in wind-turbine technology before that can happen,” said Brian Rice, division head for Multi-Scale Composites and Polymers at UDRI.
Wind turbine towers have to be strong enough to not only carry the weight of the turbine – which can be as much as 100 tons – but also to resist buckling under the stress of the rotating machinery, Rice said. To accommodate weight and stress, steel monopoles are pre-fabricated in sections as large as 14 feet in diameter and 70 feet long, then trucked individually to the wind site to be fit together and installed on a concrete foundation.
“If you increase the height of the tower, you have to increase its diameter as well,” Rice said. “Which means that next-generation wind turbines will require towers that will be too large to ship via highway, even in sections.”
The solution, Rice said, is in composites – fiberglass and resin tower sections that would be manufactured at the wind farm using raw materials trucked to the site. The manufacturing operation would be staffed primarily by local labor.
“On-site fabrication eliminates the transportation problems and makes more sites accessible to wind power development,” Rice said. “Even today there are good potential wind farm sites in remote or hilly locations, but there aren’t sufficient roads to allow for trucking in steel towers; the new design would solve that problem as well.” In addition, the corrosion-resistant properties of composites will be far more suited than steel for off-shore wind farms, which are just starting to be developed in U.S. waters, he added.
The Ohio program team, comprising lead partner Ershigs Inc. in Manchester, UDRI and Edison Materials Technology Center in Dayton, WebCore Technologies in Miamisburg, Owens Corning in Columbus, and Ashland Performance Materials in Dublin, has been working for more than two years to test materials and coupon samples and is now prepared to move into product demonstration, Rice said. The partners will design, analyze, build and test a series of progressively larger components with a goal of completing and testing a full-scale 100-meter composite tower.
“In full size, these will be some of the largest composite structures ever built,” he said.
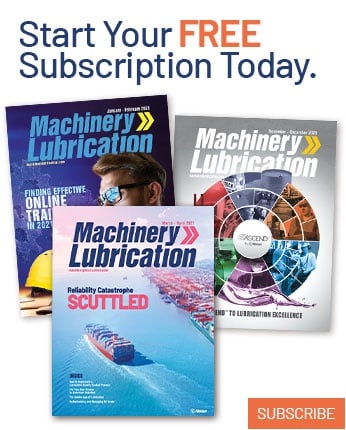