One of the crucial roles of a reliability engineer is to develop and maintain a long-lasting and effective predictive and preventive maintenance program. The main expectations of this type of program are that a company can reduce unscheduled downtime, increase production and improve overall equipment reliability. It is essential to understand how the equipment performs in a facility and to be able to predict and prevent failures before they happen. The results of the combination of these technologies will give the reliability engineer an even greater confidence when communicating to management when an asset is approaching an impending failure.
This article will provide an overview of the utilization of oil, vibration and thermographic analysis in combination with one another to prevent equipment failures. This type of approach, referred to as the “two out of three technology rule,” will give a confidence of 95 percent or greater to the reliability engineer when asking to take an asset out of production to do the necessary maintenance. This article will also provide some real-world examples of how any two technologies in conjunction with one another can lead to proper equipment diagnosis. This “two out of three” rule is referred to as the reliability engineering “Bomb Report.” This is a report from the reliability engineering group that explains what happens when two out of three technologies report the same types of anomalies correlating between them. This report is used in presenting to management when an asset needs to be taken out of service for maintenance.
Payback technologies and how they relate to one another
There are generally three accepted technologies that are looked upon as the main “payback” Technologies. They are as follows:
- Oil analysis
- Vibration analysis
- Infrared thermography
These technologies are essential in order for a reliability engineer to maintain an accurate “condition assessment.” A comprehensive and well-designed condition monitoring program will incorporate different aspects of existing technologies to improve equipment performance, reduce the number of equipment failures and the risk of equipment downtime.
Payback technologies and the problems they detect
Vibration analysis: This technology looks at rotating through various waveform trends and pattern recognition. The types of faults that you look for in vibration spectra to correlate with various technologies are as follows:
- Bearing failure misalignment (fan, pump or motor)
- Coupling lockup or failure
- Unbalance (fan or motor)
- Resonances (belt frequency, sheave and pulley alignment)
- Lubrication
- Electrical
- Structural
- Belts
- Gears
Oil analysis: This looks at fluid properties, contaminants and various kinds of wear debris to determine machine health. Each aspect of oil analysis can help correlate machine issues well before any other technology. Oil analysis is comparable to a blood test on the human machine. It has been said many times that more than 70 percent of failures are lubricant related. One of its benefits is that it detects problems in both the fluid and in the machine. It can also detect some defects earlier than other technologies. It is often referred to as the “first line of defense” as far as predictive technologies are concerned. The oil sample reports will define the following items:
- The presence of foreign fluids or destructive surface contaminants
- The overall fluid physical and chemical condition
- Presence of machine wear materials, how much, and of what type and morphology
Infrared thermography: Thermography detects heat patterns and measures temperatures of electrical and mechanical components. Thermography can detect a temperature difference, “hot spot,” due to electrical resistance or excess friction. Thermography can be used in a number of applications to understand problems with moisture, thickness, bonding, capacitance and friction. Thermography can also detect problems via heat loss from mechanical equipment. Most infrared imaging thermography is qualitative.
The types of anomalies that you look for in correlating data with other technologies are as follows:
- Motors
- Bearings
- Couplings
- Belts and sheaves
- Steam traps
- Heat exchangers
- Electrical (most common utilization of thermography)
Strengths and weaknesses of vibration analysis coupled with oil analysis
Technology |
Correlative method |
Indication |
When used |
Vibration |
Time sequence |
Wear particle build-up |
Routinely (monthly) |
Thermal analysis |
Time coincident |
With major wear |
When bearing |
Advance |
Time |
Major bearing damage |
Routinely with each filter |
Correlation of lubricant wear and wear particle analysis with vibration and thermography
The Bomb Report
The Bomb Report was developed out of necessity as a way to get management to understand the severity of what the reliability program was trying to tell them. When so much money has been invested in technologies, training, additional manpower, etc., you need to provide a means of tracking and presenting your successes to sustain any reliability program.
The Bomb Report is essentially an executive summary on the asset in question. It has the following attributes:
- Location of the asset
- The date of the confirmed presence of a problem
- The issue with the asset
- What steps will be necessary to address and correct the problem
- Provide viable options for a short- and a long-term fix, depending on operational concerns
- Any work orders issued to address the problem
- What predictive/preventive technologies were utilized to find this problem. This keeps the technologies in the forefront of managers’ minds. This aids in building that bridge between maintenance and production.
- All reliability report data to support your find. This may not be important to the leader, but engineers and other technical individuals will see this report also. This will depend on the organizational structure.
This simple name for the report holds great connotation when verbalized in any operational meeting. When I present this report as a Bomb Report, managers tend to listen. I have that “hard to get” 10 to 12 seconds of management’s attention to really drive the fact home that we have a problem out there on the floor and we need to react quickly to avert disaster.
So many times, REs will make a call with only one bad oil report in their hands and realize that they called for something to be done to a machine that had many more months, if not years, of life left in it. They make a call on a bearing because they may have seen a slight spike in lead, tin or aluminum. They could have made a call on a gearbox when they saw a slight increase in iron. Without having the benefit of two or even three technologies telling you the same thing, you really do not have the 95 percent or better confidence to really honestly ask for production to remove an asset from service for maintenance.
Making calls on machinery is a risky business. The old cliché goes that a million “at-a-boys” and one slip-up will cost you years of personal credibility. Without having the benefit of multiple technologies coming to the same conclusions, you run the risk of losing not only your credibility, but your job!
A reliability engineer needs to be trained in various technologies to understand and appreciate the benefits and limitations that each one displays. Oil and vibration analysis are excellent in combination with one another, and vibration analysis and thermography are good complements. It depends on the situation that presents itself to know which technologies to utilize to get you the answers that you need and in the most conclusive way possible.
Example of correlation between technologies
‘Two out of three’ technology rule of thumb
There are a few rules of thumb that I use in looking at my condition monitoring program holistically. By following these few simple thought patterns, a reliability engineer will have the best arsenal at his or her disposal to solve any equipment related problem that is presented.
- At least one technology needs to be used on every major piece of equipment (700 currently monitored)
- If an anomaly is observed, utilize another technology to confirm its presence
- Two technologies confirms a production concern
- Issue corrective work orders and follow-up
- Trend and track results to confirm current PM practices are addressing specific equipment issues (MTTR, MTBF, statistical analysis between like equipment sets)
- No two machines are alike, and they cannot be treated the same!
- Record successes to create business cases for upgrading and adding new technology (EVA, cost benefit analysis, payback, NPV, executive summary)
Conclusion
Correlating more than one technology has huge benefits for being able to accurately diagnose problems and rectify them before they become production outages. A reliability engineer has at his or her disposal many tools in the industry to be able to predict and prevent these types of equipment issues from happening, and also to prevent recurrence. If a few simple steps are followed, such as the “two out of three” technology rule of thumb presented here, a reliability engineer can be extremely confident in the decisions to rebuild, replace and perform specific maintenance on equipment.
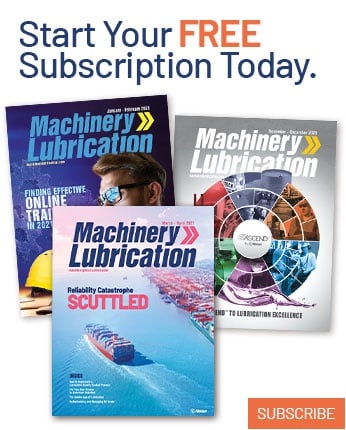