I can’t overemphasize the importance of selecting the right person to be a maintenance planner. Controlling the entire planning effort relies on staffing, period. At stake is a 1.57-fold increase in workforce efficiency.
Planners function as respected professionals making highly independent judgments one after the other based on their skills and experience.
These skills include craft skills, people skills and data skills. A company can usually find a few of these people. However, making them want to be planners can be a challenge.
This article doesn’t delve into the benefit of planning. Nevertheless, it’s worthwhile to mention it. Work coordination from planning increases wrench time from the 35 percent of a typical good maintenance force to as much as 55 percent.
Fifty-five percent divided by 35 percent yields a 1.57 improvement. This means 30 people with planned and scheduled work could perform the work of 47 people (30 x 1.57 = 47). Hence, investing in a single planner creates a 17-person increase to the workforce!
Staffing refers to selecting and training. It’s the primary controlling mechanism for a group of professionals. Without getting too deep into organizational theory, other coordinating mechanisms such as continuous communication, direct supervision, extensive rules and numerous indicators aren’t appropriate for the planning function.
If a doctor didn’t have the proper training and skills, all the other coordinating mechanisms would simply confirm that the doctor can’t perform. Similarly, you can’t hire the wrong planners and make them into good planners.
Planners should have a combination of key skills and experience. The first of these is craft skills. Planners should be journeymen-level craftspeople. Having 15 to 20 years of experience actually doing work makes them better planners. Candidates planning work outside their own areas of expertise could somewhat compensate if they excelled with people and data skills.
Planners also should have superb people skills and be able to talk with anyone. Planners ask operators to clarify needs. They deal with supervisors on a peer level. They arrange materials and services through purchasing personnel and vendors. They encourage and interpret feedback from technicians.
They must also write accurate work descriptions in the job plan. A regional manager for a shoe distributor told me that his No. 1 problem was salespeople who couldn’t write a letter that made sense.
The same goes for craftspeople. Also, note that planners interact with others not under their supervision. A supervisor may have responsibility with authority, but a planner has responsibility without authority.
Planners must also have excellent data skills. Planners can’t fall into the trap of planning every job from scratch. They must not only research information for new work but also use past feedback and files to make job plans better. In addition, they must be able to use a computer to speed the flow of information.
On top of these requirements, planners must be self-motivated to stay ahead of 30 technicians and be well-respected by the crafts. The nature of job planning is that estimates are many times merely an educated guess, and the plan itself is only a head start. This is the nature of maintenance work over assembly line work.
Nevertheless, these estimates and plans are sufficient to assign and control work and form the basis to improve plans. Technicians can’t complain about the “dim-witted planner who came up with this plan.” Technicians must realize that the “planner is a top craftsperson and the plan is a starting point. Let’s get on with the work.”
Finally, realize that the people who often meet these requirements are the hard workers who volunteer for overtime. They aren’t afraid to get their hands dirty. They would make good supervisors if there were enough openings. Yet, they don’t want to become planners for two reasons.
First, past frustration with planning creates a stigma. Second, many plants wrongly transfer technicians to planner positions at the same pay rate. Therefore, because it’s difficult to use planners to work much overtime, the planners take a net pay cut from the OT loss. Thus, only the technicians who avoid OT and want to get off the shop floor are interested in the job.
Planning can’t work when you select the wrong people. Know how to control planning with staffing. Know what makes a good planner. Deal with the issues involved and be on your way.
Doc Palmer is the author of the “Maintenance Planning and Scheduling Handbook.” He is a CMRP and has nearly 25 years of industrial experience as a practitioner within the maintenance department of a major electric utility. From 1990 through 1994, he was responsible for overhauling the existing maintenance planning organization. The resulting success played a role in expanding planning to all crafts and stations owned and operated by the utility.
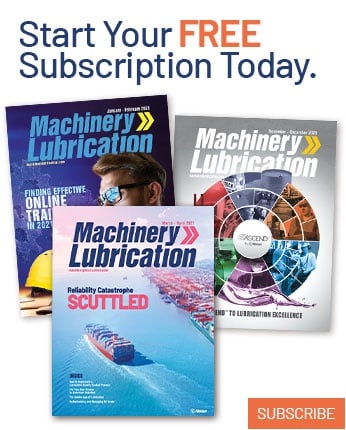