Maxtek Components Corporation, a Tektronix Inc. company and a provider of turnkey packaging services for microelectronics, on September 15 announced the completion of a year-long project to apply lean manufacturing principals throughout their 32,000-square-foot assembly facility. While this change to lean has already resulted in strong improvements in productivity and efficiency, it is more importantly a reflection of the organization's commitment to continuous improvement and the goal of ensuring each manufacturing step is providing value to the customer.
In applying lean manufacturing, Maxtek took a "process-centered" assembly line and created 16 lean cells tailored to meet customer needs for wire-bond BGAs, flip-chip devices and RF/microwave modules. Production goals are now more tightly aligned with customer demand and the company has worked to eliminate waste to ensure that all manufacturing activities provide value to the customer. In addition, the lean conversion has enhanced Maxtek's high standards of quality and performance through the deployment of a visual management system to evaluate each cell on strict production standards.
The impacts of the lean conversion have been telling, with improvements in overall productivity, decreased work-in-progress (WIP) inventory, and reduced lead-times. For example, within two months after lean conversion, Maxtek's RF/microwave cells exhibited an 81 percent improvement in parts produced per hour (productivity). These same cells also reduced WIP by 50 percent, thereby decreasing inventory requirements. These improvements translate directly to an increase in customer value: from decreased scrap and shortened lead-times to a reduction in labor content of 20 percent.
"Our application of lean manufacturing enables us to better base inventory management and production planning on customer demand, while maintaining focus on providing value to our customers," said Tom Buzak, president, Maxtek Components Corporation. "This change represents a long-term commitment to improving our manufacturing processes and ensures that Maxtek will consistently meet our customers' needs for quality, delivery and cost."
A Commitment to Continuous Improvement
Maxtek's switch to a lean manufacturing system is not a one-time change. Rather, it represents the adoption of a new philosophy. The notion of lean is primarily credited to the Japanese automaker Toyota, a company that based its production philosophy on the Japanese concept of kaizen, which means continuous improvement. Kaizen is about the pursuit of perfection and a desire to improve, in every process and activity, at all times. Perfection is generally unachievable, but improvement is always possible.
To help ensure continuous improvement, Maxtek based its approach to lean conversion on the Danaher Business System, which was introduced to the company in November 2007 when Danaher acquired Tektronix, Maxtek's parent company. DBS is unique because it focuses company efforts on improving efficiency in four key areas: quality, delivery, cost and innovation. The Danaher Business System utilizes numerous visual management techniques to enable workers and managers to quickly evaluate overall efficiency and achievement of goals. In addition, DBS employs many unique problem-solving techniques which encourage innovation in process improvements.
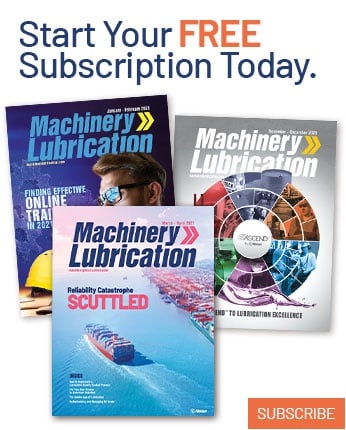