Airmen assigned to the 36th Maintenance Squadron's Fabrication Flight at Andersen Air Force Base in Guam are a mixture of permanent party and deployed Airmen supporting the U.S. Pacific Command Theater Security Package deployments and Continuous Bomber Presence in the Asia-Pacific region. The flight is composed of Airmen who work in the aircraft structural maintenance section, aircraft metals technology section and nondestructive inspection section.
Nine Airmen are permanently assigned to the flight while 24 are deployed from Elmendorf AFB, Alaska, and 10 Airmen are deployed from Barksdale Air Force Base, La. As a team, the fabrication flight is the sole repair facility for any air frame that arrives on the flightline.
"On average, the fabrication flight is responsible for more than 1,600 aircraft dispatch repairs each year, which can range from replacing a rivet to an aircraft's skin," said Master Sgt. Michael Bohanan, 36th Maintenance Squadron Fabrication Flight chief. "There would be a potential for catastrophic failure of aircraft structures if the expertise was not available to make the necessary inspections and repairs to the aircraft deployed or transient to Andersen."
Bohanan said one of the major issues here for the fabrication flight is the constant battle to combat corrosion due to the weather and Andersen's geographical location near the ocean. Each section within the flight plays an important role in supporting all aircraft, which include the deployed bombers and fighters, as well as U.S. Navy and Coast Guard air frames.
"The nondestructive inspection section is responsible for inspections to maintain the integrity of the aircraft," he said.
These types of inspections include joint oil analysis program sampling of engine oil to detect contaminations, which could lead to potential engine failure and other inspections such as magnetic particle, eddy current, dye penetrant and x-ray inspections, which detect material deficiencies such as cracks and gouges on aerospace ground equipment and aircraft.
Since the integration of permanent party and deployed Airmen, Bohanan has seen a great deal of change since his deployment in 2005, from Barksdale AFB.
"This flight has come full circle," he said. "It's all due to the responsibility of the leadership. Their efforts help us accomplish the mission."
The leadership includes NCO like Tech. Sgt. Brian Leonard, 36th MXS aircraft structural maintenance craftsman.
"Integration is used to effectively utilize manpower to increase maintenance efficiency for both flight line and back shop maintenance," said Leonard. "We had growing pains, working past the traditional mind set of temporary duty versus home station, but over the different rotations, we've ironed things out and work smoothly as a team."
Leonard said that the additional manpower helps due to the added workload with mission capability.
"Our mission here at Andersen Air Force Base has increased due to the Theater Security Package, Continuous Bomber Presence and upcoming Global Hawk missions. Because of these missions, Andersen AFB is a major force in the Pacific," he said.
The structural maintenance and corrosion control section is responsible for the structural maintenance and corrosion control on transient and deployed aircraft, and support equipment. This includes inspecting, repairing and removal of corrosion on support equipment.
"We're a full paint and body shop for aircraft parts," Leonard said. "We can fix a crack or remove corrosion and repaint the part to like-new condition."
The fabrication flight works to prevent aircraft from returning to depot or home station for necessary parts. All field level repairs are accomplished here rather than sending the aircraft elsewhere.
"Everybody has an important job to keep the planes flying, but we're the ones who machine the parts that go on the plane," said Staff Sgt. Frank Ruckel, 36th MXS metals technology section NCO in charge, who is deployed from the 3rd Equipment Maintenance Squadron at Elmendorf AFB. "We can make a screw for the aircraft if crew chiefs need us to. This prevents the aircraft from going to the depot saving the Air Force money and keeps the aircraft flying."
The metals technology section can make something as simple as a bushing to keep the size of the hole within tolerance of a technical order to fabricating a bath tub fitting, which prevents a crack from spreading on a main joint.
"Whatever comes up with the aircraft, we're here to support," Ruckel said.
Ruckel believes the task at hand can be somewhat difficult at Andersen given the time delivery of materials and supplies.
"Not having the proper tools or materials to complete the job is the most difficult part of the job," he said. "It takes weeks, even months to get them ordered and to the island. Where as in the states, it takes days, but we overcome by using alternate strategies to complete the job; it just may take a little longer."
While overcoming some disadvantages of obtaining parts in Guam, Ruckel said the best part of his job is being able to make a part out of square or circle stock and seeing an aircraft complete a mission.
"Being able to take a piece of metal and watch it turn into a part that is installed on an aircraft, which you can see take off, complete a mission and return safely ... knowing that you are the one that helped fulfill that mission, is the best part of my job," he said.
The fabrication flight is on call 24/7 to support maintenance operations to ensure a 100 percent success rate.
Airmen deployed from Elmendorf and Barksdale AFB are deployed for four-month deployments and will return to their home stations between September and October.
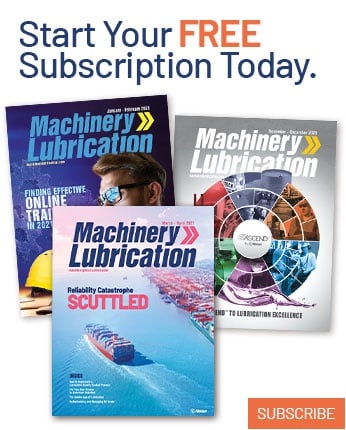