The Hollywood version of Willy Wonka’s chocolate factory is far removed from the realities of contemporary candy manufacturing, but Willy Wonka might find some things in common with the Zaini S.p.A. chocolate and confection plants in and near Milan, Italy.
For one thing, Willy Wonka’s phantasmagorical sweets sprang from ingenious contraptions operated by his workforce of Oompa Loompas. Luigi Zaini’s original factory, established in 1913, produced hand-crafted chocolates, cocoa and candies, but as the business grew, machinery was incorporated to help employees meet the growing demand.
Willy Wonka’s product mix included inventions such as ice cream that never melts or chewing gum that never loses its flavor. Zaini produces a vast range of chocolates, confections, sugar-free candies, and seasonal items (such as Christmas candies, Valentine hearts and Easter eggs) at its two plants in Milan and Senago, Italy.
In the economic boom following World War II, the company’s production expanded through the creation of candies and chocolates enriched with vitamins and minerals, authorized by the Italian Ministry of Health.
Today, the Zaini factories might not look out of place in Willy’s Wonkavision Room. For example, at the Senago plant, the ABB FlexPicker IRB 340 has been working since 2005 to organize and box a wide range of bagged candies and chocolates.
The IRB 340 has an almost otherworldly ability to “see” up to 130 different product variations and adjust its activity accordingly, with minimal human supervision.
Flexible production line
The FlexPicker came to Zaini at the recommendation of PRB Packaging Systems, specialists in end of line machinery and solutions, based in Bologna, Italy.
“Zaini asked us to develop a system to handle a vast range of their products for packaging,” recalls Agostino Biagini, a partner at PRB. “The system had to be flexible, easy to operate, and easy to modify, since the products and boxes for shipping change very frequently. This made the assignment especially difficult.”
“We sell to supermarkets and retail outlets such as bars, and both are highly competitive markets,” explains Amerigo Pallanti, factory manager for Zaini.
In competitive markets, even a small cost or efficiency advantage can be determinant in holding or winning share.
An additional consideration for Zaini is the seasonal nature of the candy business, with huge volumes between September and December, less so for Valentine’s Day through Easter, then tapering off till the following September. Flexibility on the production line means employees are free to handle more demanding assignments.
The proposed solution had to be reliable, flexible, precise, adaptable and easy to operate, with equipment sensitive to changes in product format, according to Biagini.
PRB came up with a combination of the FlexPicker and its own F-30 vertical case packaging machine, capable of dealing with products that – when they arrive at this phase of the production cycle – are not always aligned on the production line but follow each other in a determined distance.
Challenging demands
The biggest challenge for ABB, PRB and Zaini was to ensure that the robot could handle up to 40 formats and 130 different iterations: Zaini’s range of bags holds from 50 grams to one kilo of chocolates or sweets, the bags’ contents have different sizes and shapes (e.g., small squares, rounded eggs, hard candies), and there are different-sized packages for shipping and display, depending on the content and weight of the bags.
In addition, “the formats change every day,” says Dario Stringhetti, a technical specialist at Zaini.
As the pre-bagged items roll down the production line, a tele-camera “sees” the format and pre-disposes the robot to the proper activity so it can sort and place items in the appropriate containers. The camera is deliberately not mounted on the robot arm in order to prevent damage to the camera as a result of vibration from the robot’s movements.
The IRB 340 proved equal to the chocolate challenge. It can handle 90 50-gram packages a minute and 35 one-kilo packages a minute, working two shifts (16 hours) a day, five days a week. Before the FlexPicker, no “pick and place” robot had ever taken on this level of complexity in a food or confection line.
“The robot could go even faster, but we don’t do that for logistical reasons,” says Stringhetti. “We expected a lot from this machine, and we got everything we expected.”
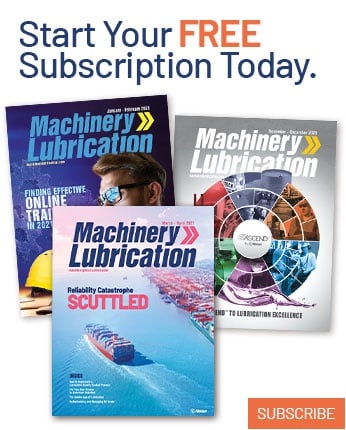