Surprising as it may seem, a particle of 5 microns or less can cause a precision bearing to fail. To put this particle size in context, a human hair is around 60 partial microns; a fingerprint 13 microns; a dust mote 25 microns; and tobacco smoke 6 microns. These particles may be minute, but with their potential for damage, the message has to be that it is vital to maintain a high degree of cleanliness inside precision bearings. It is also vital because even when small particles of foreign matter are not actually causing failure, they can ruin the bearing’s smooth running qualities and low torque values.
In general terms, dirt and contaminants that can impede a bearing’s performance are divided into three main categories: airborne contaminants, transferred contaminants and introduced dirt. Included in the first category are such items as lint, metal flakes, abrasive flakes, industrial smoke and dust. In contrast, transferred contaminants are dirt that is picked up from one source and passed along to the bearing from hands, work surfaces, packaging, tools and fixtures. Finally, the introduced dirt category deals with impurities that enter the bearings from dirty solvents or lubricants.
In addition to the main categories, other contaminants that are often overlooked are humidity and moisture, fingerprints (transferred through handling), dirty greases and cigarette smoke. These, in common with all the above sources of contamination, should be considered abrasive, corrosive or leading causes of degradation of bearing performance.
The problems of maintaining bearing cleanliness begin the moment that bearings are removed from their protective packages. Because of this, it is best not to remove them until they are ready for use, and then only after the work area has been effectively cleaned and prepared. Once unpacked, the bearings should only be handled with clean, dry, talc-free and lint-free gloves.
Here, care should be exercised as material incompatibility between the gloves and any cleaning solvents could result in contaminant films being transferred to the bearings during subsequent handling. Where the bearings are instrument types, even handling with gloves should be avoided in favor of surgical tweezers.
Of course, cleanliness extends not only to the bearings themselves, but also to work and storage areas, benches, tools, fixtures and housings. A clutter-free work area, with good lighting, organized tool storage, handy parts bins and appropriate work fixtures, constitutes an ideal working environment. Under no circumstances should food or drink be consumed on or near work surfaces. Smoking should not be allowed in the area where bearings are being replaced; and bearing installation operations should be located away from other machining operations, such as grinding and drilling (etc.) to help minimize contamination problems.
A further stricture regards static electricity, and other operations that may cause the steel rings and balls of the bearings to become magnetized. These could result in dust of fine metallic particles being introduced into the bearing. If there are any signs that the bearings have become magnetically induced, then they should be passed through a suitable demagnetizer while still in their original sealed packaging.
Also key to maintaining cleanliness is a good workbench surface material, such as metal or plastic. Generally, painted metal is not desirable as a work surface because it can chip, flake or rust. Plastic laminates may be acceptable and are easy to keep clean. In addition to a good surface, every workbench should have a well-stocked complement of clean, burr-free tools that are designed for the job. The tools should not be painted or chrome-plated as these can provide a source of particulate contamination, which might ingress and damage the bearing.
The requirement for burr-free components also extends to all other parts of the bearing assembly, especially housing interiors and shaft seats. These two areas should also be thoroughly cleaned before fitting.
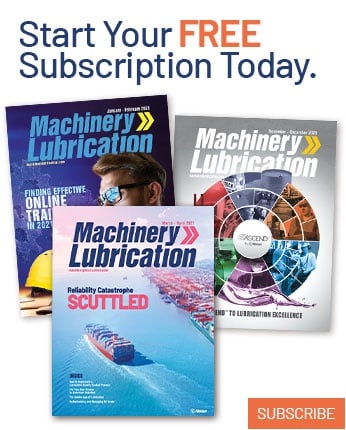