During an economic slowdown, manufacturers tend to downsize in the front office, the plant floor and sometimes even in maintenance. While many maintenance departments already outsource some tasks, force reductions will mean more use of contractors in the months ahead.
It will not be practical for a manufacturer to outsource maintenance entirely, but many will outsource as much as they can. Unlike members of the maintenance staff, contractors are only on the clock for you when they are on site, and there are efficiencies to be realized.
Even with many modern enterprise asset management (EAM) or computerized maintenance management systems (CMMS), it can still be a challenge to optimize the work of an internal maintenance staff, much less the work of outside contractors. But there are some specific technology tools and best practices that can allow a maintenance manager to plan for and coordinate the work of outside contractors just as if you were running a unified, world-class, maintenance department.
Identifying when to outsource
There are really three different situations in which outsourcing maintenance will be attractive. Holistically, good management of contractors requires a preventive maintenance setting, and you should have the sufficient historical data on the amount and type of work required to maintain each piece of equipment so you can make projections about future needs. It only takes a small amount of equipment history, kept in an EAM application that has predictive and statistical capabilities, in order to begin to make some of these determinations.
Object Structure: The plant’s equipment is entered into the EAM Module in Object records that are organized into a structure for cost roll-up. This allows the maintenance manager to then view the cost to maintain the plant’s equipment at different points in the structure such as the overall cost of all equipment in the plant or down to an individual component.
Equipment Object Cost/Revenue Analysis: This is the view that allows the maintenance manager to see the cost/revenue for the equipment at any level in the structure and for any period of time by the different cost types.
During downsizing, a smart manufacturer will hang on to the people whose skill sets are directly related to its specific manufacturing processes. But even in the best of times, many maintenance departments already outsource two types of tasks. The first type is maintenance of assets that are separate and distinct from the automation and production equipment itself – things like air conditioning, refrigeration, HVAC, boilers. These tasks are not immediately related to the ability of the manufacturer to get product out the door, and can easily be handled under long-term contracts. That allows you to specialize in the production equipment.
Highly specialized work is often outsourced as well because it requires skills and equipment that are needed only infrequently – things like thermography inspections, laser alignment of Thompson motors or vibration analysis. But with a reduced workforce, maintenance managers will want to look carefully at their equipment histories and analyze the frequency with which certain tasks need to be performed. If it is hard to cost-justify maintaining the capability internally, contracting that function out may be a better choice.
Conversely, if your maintenance schedule calls for a large amount of refit work and you are short of certified welders or people qualified and mask-fit for confined space work, you’ll need to either work with your purchasing department to find a contractor or work with your human resources department to cross-train existing staff or hire additional staff.
An annual or semi-annual plant shutdown can also be a good time to outsource. Your time during that Christmas shutdown is very valuable, and you’ll want to bring in as many people as possible to get the required work done in that constrained period of time. Integration between a maintenance system and production systems will help you make better decisions about the degree to which hiring contractors is desirable during that shutdown. If the required work can be completed in 14 days instead of 21 days, does the increase in production capacity merit additional contractor involvement?
In order to make good decisions about hiring contractors and manage their work once they are on-site, there are specific technology best practices that will be very attractive.
Integrate with the enterprise
There are some pretty good stand-alone maintenance and CMMS packages out there, but both internal staff and contractors can be managed more effectively when maintenance technology is integrated with software used to run the rest of the enterprise. And it can be a lot easier and more cost effective to operate a maintenance solution that is built into an enterprise suite than it is to integrate a number of point solutions. The benefit of a unified, integrated enterprise resource planning (ERP) strategy as opposed to standalone solutions is that the maintenance manager has a lot more information available to him or her, and can leverage information and expertise in other departments.
It makes a lot of sense to integrate maintenance with the manufacturing schedule so you can see the uptime required of each piece of equipment out to the time fence – as far in the future as your production schedule allows. Then you can plan maintenance activities and schedule contractors accordingly. Integration between maintenance and finance will help make the strongest business case with senior management for either contracting or hiring necessary staff.
Prepare Work Order: The Object ID is entered in the resource tab of the Manufacturing Work Center and is reflected in the Work Order when it is created for the Object.
Load Per Work Center: The Planned Execution Time from the Work Order is then reflected in the Load Per Work Center View on the scheduled Start Date of the Work Order. This is basically requesting a slot in the Manufacturing Schedule to perform the maintenance on the equipment.
But the most attractive efficiencies for managing maintenance contractors come when maintenance is integrated with human resources and with purchasing.
Within an enterprise-wide solution like ERP, the maintenance manager gets visibility into human resources data like staff schedules, skill sets and certifications. He or she can schedule manpower, see capabilities, view certifications and compare those capabilities with the demands of the maintenance schedule. He or she is also in a position to work more closely with the human resources department to advocate for additional skills training or additional hiring to close capabilities gaps.
Prepare Work Order Allocation – Craft: Work operations can be planned to be executed by a specific craft to which certain qualified employees would be assigned.
Resource Load Graph: The schedule assigned in HR to the employee is reflected in the Resource Load Graph by the red line. The allocated Work Order operation now also shows eight hours allocated to the resource on March 23.
Integration with the purchasing component of an enterprise application relieves the maintenance manager of purchasing responsibility. All the maintenance manager needs to do is place demand in the system through his or her work order and let those who specialize in purchasing and negotiating contracts do what they do best. Purchasing integration also helps ensure that the materials that contractors need are on hand at the right time, or that contractors are supplying materials according to their contract. Once again, demand is driven in the purchasing system directly by the work order.
Work Order Requisition: A requisition for materials or services can be entered from within the Work Order to create the demand for purchasing to buy goods and services required to perform the repair.
Leverage enterprise project functionality
Today, modern enterprise applications like ERP not only provide project management functionality, but also allow for management by project. Within the last three to four years, we have seen a trend toward managing maintenance operations in a project environment, with activities and milestones and work orders tied to those activities.
Work Order Project Connection: The Work Order can be connected to a Project Activity from within the Work Order during the planning of the Work Order.
What this means is that while the technician reports his or her time, materials and work he or she is doing through a work order, behind the scenes, those work orders are tied to a project. That makes the coordination of those work orders very easy, giving management visibility of milestones that have been achieved as well as costs that are being incurred. In the case of a plant retrofit, or a large plant shutdown, a maintenance team can lay all of the activities involved in that large project in a project plan that can be shared with contractors. Work orders are attached to each activity and each milestone so everyone knows when their work needs to be performed, what manpower they’ll need, and what tools and materials they’ll need to execute a specific activity within a project. This helps the contractor complete their tasks according to your needs and also streamlines the management process for you.
Open your system to your contractors
It is very desirable to give your contractors access to your internal systems. There are two reasons that this is a good idea. First of all, as you plan maintenance work for three weeks out, if your contractors have visibility of this in your system, they can be informed of the upcoming work, schedule their people and ensure that they have the right tools and materials available. If they are seeing that rolling schedule, they can be responsive to your needs. This also reduces the amount of time necessary to manage those outside contractors by phone and e-mail.
The Web Portal Business to Business view allows the Contractor to use a customized view to access certain key records quickly.
Moreover, if the contractor can report their work activities directly into your system, you are getting real-time updates of work completed. That eliminates the delay that results when the contractor enters the data in its own system, and the data flows through reporting mechanisms within that contractor environment and back to the manufacturing maintenance team, which then has to enter that record of work back into the EAM, ERP or CMMS. That repeated entry is wasteful and increases the likelihood of mistakes. Real-time data can also allow for tighter coordination between the contractor and internal maintenance staff or with other contractors working on that asset. Moreover, that real-time data could allow for more efficient use of the asset, as in the resumption of a production schedule.
About the author:
IFS implementation manager Mike Auer has more than 25 years of experience in aerospace, power generation and high-speed manufacturing industries specializing in the implementation of predictive/preventive maintenance processes. Prior to joining IFS, he held industrial maintenance, engineering and other positions with Pergo Inc., Commonwealth Edison, Ford Aerospace and other major corporations. He holds a degree in business management from the University of Georgia. To learn more, visit www.IFSWORLD.com.
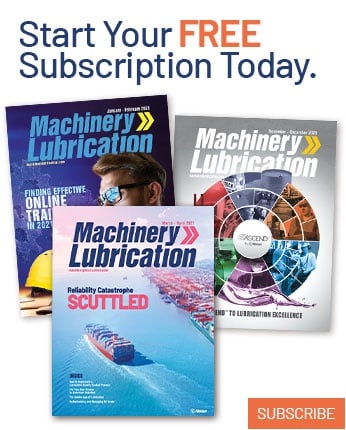