Anyone of us in business today that has to deal with enterprise resource planning (ERP) systems knows that while these systems are meant to make life simple for us, it more times than not works in the opposite direction. We are constantly battling to schedule our work to match our customer requirements based on the output of our computer system. To borrow a quote by Japanese NUMMI leaders as reported on Curious Cat blog, “computerized inventory systems lie”. Regardless of all our efforts to keep current and accurate information fed into the mouth of the computer ERP system beast, our computer system never matches the dynamic, real (physical) world. In my experience, it’s true that computerized inventory systems lie.
This is a visible problem. What are our choices?
We could run through the PDCA (Plan-Do-Check-Act) cycle and put as many countermeasures into place as required until the problem is fixed. We could improve the training of all our associates to insure that we follow the system as designed. We could buy another ERP computerized system that is more adaptable, flexible or customizable to fit our needs. Or, we can just give our ERP system the finger and try a different approach.
The latter approach is exactly what we are trying to do at Batesville Casket Company (as seen in the picture above from our lumber fabrication facility). Of course, by finger I mean just a visual indicator of our FIFO (First In, First Out) flow, not the other finger as I may have intentional led you to believe. It is just part of our lean focus in making our parts flow using simple visual means instead of using ERP solutions within the plant. We even have started using the whiteboard scheduling approach in our dry lumber storage before cutting. The whiteboard approach has been recommended many times in the past by Kevin Meyer at Evolving Excellence. The goal is to make it simple and visual. It is still early, so I’ll wait to share the results until after we stabilize and sustain our new process.
Although we have been dabbling with kanban systems and other visual management techniques for many years, we have never really committed to pushing ourselves to making this visual management system of material scheduling and inventory control a major part of our culture. No excuses, but we just had other improvement opportunities to go after that we thought were simply more important.
About the author:
Mike Wroblewski started his lean journey with instruction in quick die change from Shigeo Shingo. Mike is currently the lean sensei at Batesville Casket Company in Batesville, Ind. He also writes a blog called “Got Boondoggle?” featuring lean and Six Sigma topics. Check it out at http://gotboondoggle.blogspot.com/.
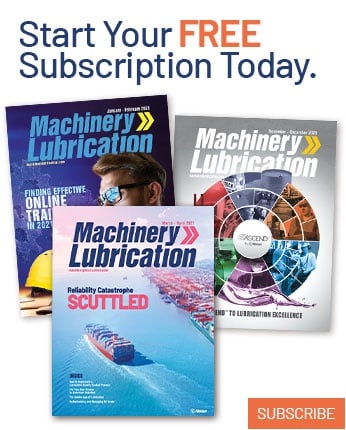