
Die coats prevent premature solidification of the molten metals while filling and also prevent adhesion of the molten metal to the metallic die. A revolutionary new coating developed by the Australian research organization CSIRO, could see die coats that lasts up to 14 times longer than existing products.
The long-life insulating coat, known as CASTcoat, was invented by CSIRO scientists Mahnaz Jahedi and Stefan Gulizia.
"This new coating could mark a signification turning point for Australia's A$500 million die casting industry," says Jahedi, the project leader.
Current coatings offer poor wear resistance as they struggle to adhere to the die for more than a few shots. Every few shots the damaged area of die coat has to be repaired or touched up. Eventually, the conventional die coat is stripped and reapplied. This makes the application of conventional die coats highly operator-dependent.
CASTcoat technology overcomes problems associated with the conventional die coat because of its use of thermal spray technology. Instead of using a silicate-based binder, the bonding between ceramic particles partially melts the ceramic particles during thermal spray, fusing together on impact.
The resulting bond is far stronger than traditional binders. This means high wear-resistance and durability, ensuring the die is better protected, and with no need for constant touch-ups.
In a current European trial, a car parts producer that supplies well-known automotive manufacturers has been "extremely impressed" by the results. Jahedi says the company applied CASTcoat before Christmas and by the end of January it was still in production.
"Using conventional die coats, the insulating coating would have been touched up or replaced many times by then," he said.
Jean-Michel Bachtarzi, Acheson Global Business Director, process and engineering materials, says, "CASTcoat provides Acheson with a revolutionary new technology that creates significant new market opportunities for our company."
The insulating properties of CASTcoat can be tailored to any application, without changing the die-coat thickness, while product consistency can be ensured. A wide range of casting surface finishes, from rough to very smooth, can also be produced by CASTcoat and maintained. Jahedi says the durable insulating coat can be used across a variety of applications, such as molten metal handling or wherever any insulating and wear resistant coatings are needed.
CASTcoat started as a PhD project between CSIRO and the University of Queensland and has continued with financial support from the CRC for Cast Metals Manufacturing (CAST).
For more information, see the CSIRO Web site.
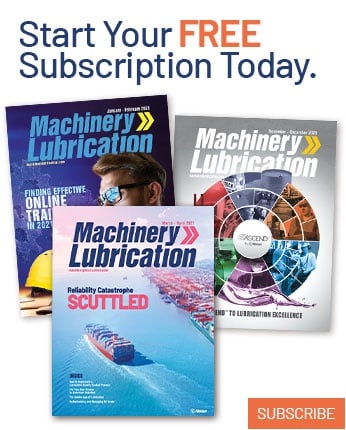