All too often in my consulting work, I'm faced with people who state, "We don't have many (any) lubrication-related failures." Probing deeper, I usually ask something like, "So, you've never replaced a bearing since the plant was built in 1965?" Of course, the response is invariably, "No, we do replace bearings when they wear out, but our vibration analysis or oil analysis typically finds the problem before the bearing fails."
Implicit in this statement is an often widely held belief that for a problem to be considered a "lubrication failure", the machine must have catastrophically failed, causing untold hours of downtime, and have been directly related to either a lack of lubrication or the use of the wrong lubricant. In my opinion, this is much too narrow a focus and fails to recognize all the other ways in which a plant's lubrication practices impact cost and mechanical reliability.
By way of illustration, consider the life of a rolling element bearing. Historically, the life expectancy of rolling element bearings has been given by the bearing's L10 life. This rating is calculated based on the load and speed a specific bearing is expected to support; it represents on a probabilistic basis how long the bearing should last before a fatigue failure occurs, with a probability of success of 90 percent. Put another way, for a population of 100 identical bearings with a specific L10 life, we might expect 90 of those 100 bearings to still be operating when the L10 life period has been reached. Common L10 lives might be anywhere from 80,000 to 200,000 hours (or more), depending on application.
In practical applications, a bearing's L10 life is usually multiplied by three adjustment factors, a1, a2, a3, such that the anticipated life of a bearing can be stated as:
Adjusted bearing life = a1 x a2 x a3 x L10
The factor a1 is very simple. It is nothing more than an adjustment of the L10 life, depending on the reliability requirements of the system. For example, taking the L10 life as the baseline (i.e. a1 = 1.0), to calculate the L1 life (i.e. a 99 percent probability of success, or just a 1 percent probability of bearing failure), we would use an a1 factor of 0.21. Put another way, for us to have a 99 percent probability that a bearing won't fail within a certain time period, we'd have to reduce the life expectancy to just 21 percent of the calculated L10 life. The chart below shows commonly used reliability-based adjustment factors.
The a2 factor is based on the material used to fabricate the bearing and the finishing that has been applied. For example, if we used a material or finishing process that resulted in a bearing that's less prone to fatigue failure, the a2 would be greater than 1, indicating that the bearing might be expected to last longer than the simple L10 calculations.
But from a lubrication perspective, it is the third factor, a3, that is of most interest. The a3 factor takes into account the effectiveness of the lubricant in preventing premature bearing wear. Perhaps the most important component of a3 is the ratio of the actual viscosity of the oil or grease under operating conditions (pressure and temperature) to the minimum calculated viscosity required to create full film separation of the bearing surfaces. This ratio is often referred to as the "Kappa value". It's acknowledged that Kappa values in the 2 to 4 range are required for optimum bearing life.
In my experience, the most common lubrication problem in rolling element bearings (particularly grease-lubricated bearings) is an inability to appropriately select the correct base oil viscosity of the lubricant in order to preserve an operating Kappa value in the 2 to 4 range.
Bearing manufacturers include another correction factor as part of a3, specifically related to cleanliness. While cleanliness is less of a factor for bearings protected by a full film (Kappa values in excess of 4), for bearings with less of a film thickness and/or greater stress, the effects of contaminants can greatly impact the ability of a bearing to near its L10 life. In some systems, life adjustment factors as high as 3 to 5 can be expected, indicating that with clean systems, we might expect that the bearing might last three to five times the anticipated L10 life simply be keeping the lubricant clean.
So, whenever you replace a bearing, even if the problem didn't result in any downtime, ask yourself, "Did the bearing last the longest time possible, or could we have done better in extending its life?" Bearings and the labor required to replace them aren't free!
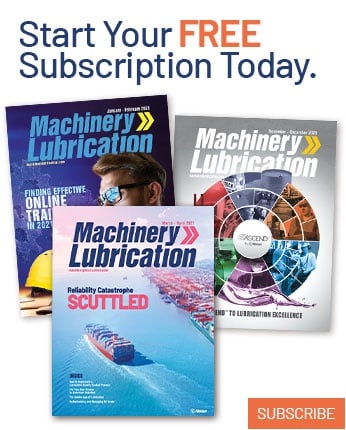