Nissan Motor Company Ltd. on September 25 announced details of its quality improvement program "Nissan GT 2012 – Quality Leadership", one of the three commitments outlined in the company's five year mid-term business plan, Nissan GT 2012 announced in May 2008. The program aims for leadership in four quality areas, perceived quality / product attractiveness, product quality, sales and service quality, and quality of management.
In this program, objectives are formulated across six indices with seven Nissan Excellence Program (NEP) global teams setup to achieve these goals. Headed by a corporate officer, the NEP teams will address seven key issues including improvement in engineering quality, production quality, breakdown quality, customer service qualities in sales and service, countermeasure lead time, and supplier quality. The NEP teams already started preparation of "Nissan GT 2012 – Quality Leadership" in May, 2007 and moved into the operational phase in April this year.
The six objectives of "Nissan GT 2012 – Quality Leadership":
· To halve warranty claim rates for first three months in service after delivery
· To halve supplier parts defect rate
· To halve breakdown ratio compared to fiscal year 2007
· To halve lead time from occurrence of defect to preparation of new parts
· To double regions where SSI (Sales Satisfaction Index) and CSI (Customer Service Index) are only Nissan as top level
· To double the number of models which are rated high in perceived quality by both internal and external metrics
Kazumasa Katoh, senior vice president in charge of product quality, said, "Nissan is continuously making efforts to improve quality and by using benchmarked information from its alliance partner Renault, the company is able to adopt a wide range of actions for improvement. "Nissan GT 2012 - Quality Leadership" is indispensable for us and I believe, by achieving this, Nissan will gain trust from all its stakeholders".
Six objectives established in "Nissan GT 2012 – Quality Leadership"
1) To halve warranty claim rates for the first three months in service after delivery.
Defective parts accounts for about 35 percent of all the vehicle parts. The remaining 65 percent, the company has achieved ZERO rate defect. To reduce defects by half, 35 percent of those defective parts need to be examined from the start of its engineering phase and integrated into the requirements for achieving ZERO defect. To engineer more defect-free parts, Nissan will adopt a system called Design Review (DR). In DR, procedures to examine potential defect risks of parts which are newly engineered or implemented in the new models will be improved in order to prevent defects. In addition, a new approach, Quick DR, will also be introduced this year which greatly expands the range of DR application. As Quick DR can be only conducted by a qualified person, the number of personnel will be increased globally. From 2006 levels, the numbers will be increased from 2 to 50 in general manager level, 5 to 1,000 in manager level and 250 to 4,300 in staff level by FY 2010. At the production phase, more accurate measuring devices will be introduced as needed this year. This will thoroughly prevent vehicles with defective parts to come out from plants and, by measuring manufacturing process capability, eliminate elements in production process which can lead to defects.
2) To halve supplier parts defect rate.
Nissan's suppliers are expanding globally. To ensure product quality level, Nissan ranks quality assurance levels of production sites of its suppliers based on "Alliance Supplier Evaluation Standard (ASES)" and only employs suppliers which have acquired a certain level. By maximizing the use of Field Quality Center (FQC), which was established last year in Nissan Technical Centers in Japan, US, and Europe, The company provides suppliers with more market information on quality, defective parts and intensive joint studies. In addition, suppliers will be re-evaluated based on ASES and improvement plans will be jointly formulated. This will promote improvement and reduce the supplier defect rate by half by 2012. Partnerships with suppliers will be increasingly strengthened in the future.
3) To halve breakdown ratio.
Breakdown means vehicle defects which require repairing on site. Nissan will set up Shift_Quality Teams in the dealerhips in German, France, the United Kingdom, Spain, Italy and Russia that will monitor such breakdowns. Nissan aims to acquire detailed information on breakdowns within 20 minutes after an incident happens, send a engineering team to the site, and determine the cause. Nissan will also try to increase the rate of detection for vehicles with defects to reach dealers to more than 90 percent by 2012. This will reduce the need for vehicles with breakdown to come in for repairs at local dealers.
4) To halve lead time from occurrence of defect to preparation for new replacement parts.
When defects are found in the market and the vehicles are taken into dealers, causes of defects are determined, necessary countermeasure in engineering and production phases are taken, appropriate parts are implemented in plants, and service parts are prepared. This time frame from delivery of vehicles to completing preparation of service parts will be managed and the length will be reduced. For problems resulting during the engineering phase, the length will be reduced by 40 to 50 percent compared to FY 2007, and for those from production phase reduced by 25 to 40 percent. To achieve these, development team, production team, and suppliers, will work together using FQC to investigate causes of defects and take necessary countermeasures.
5) To double regions where SSI (Sales Satisfaction Index) and CSI (Customer Service Index) are on their top levels.
A Global Sales & Service Quality Department was established in April 2008 and is working to spread Nissan Sales and Service Way (NSSW), the company's policy for customer care, to more than 7.000 outlets which sells Nissan vehicles. Customer service and support for dealers are strengthened by adopting sales and service training for over 130,000 dealer staff globally and utilizing Nissan Customer Service Center (NCSC) established in March 2008.
6) To double the number of models which is in the top in perceived quality.
Perceived Quality (QR) is an index which evaluates how customers actually perceive quality by seeing, touching, and using the vehicles. This year, Nissan will be focusing on 10 main items that customers put special emphasis on.
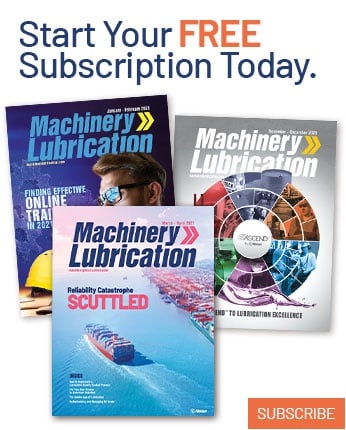