Is an inspector actually doing the inspection on the task list? That’s one of the toughest maintenance problems to solve. Horror stories about maintenance catastrophes often feature task lists that were signed but not performed.
Step one is to pick the right people. “A successful preventive maintenance (PM) program is staffed with sufficient numbers of people whose analytical abilities far exceed those of the typical maintenance mechanic,” writes August Kallmeyer in the book “Maintenance Management”.
Why pick high-level people? Because they can detect potentially damaging conditions before those conditions arise. Your best tear-down mechanic is not necessarily your best PM inspector.
A great PM inspector can work alone without close supervision, is interested and trained in new advanced predictive maintenance technology, knows how to review a unit history and its class history, is proactive – acts on predictions rather than reacts to situations – detects deficiencies early, is not interrupted and (while in the PM role) is segregated, if practical, from the rest of the maintenance crew.
Step two: Motivate your people to do the tasks as specified when the tasks are required. Most people find PM tasks boring and mind-numbing. The challenge for leaders is to inspire the troops to want to do the tasks well.
The inspector mentioned in this section can be a regular part-time mechanic (or helper, if appropriate) or a full-time PM mechanic. Here are some steps you can take to help ensure compliance.
-
Make sure the inspector knows how PM fits in with the overall scheme. Inspectors for nuclear power plants or airlines know full well the impact of missing a PM – and even then, it happens.
-
Take your top managers down to the bowels of your plant and have them address maintenance crews about the criticalness of PM and output or safety. (You might have to write the speech.) People attend to what they think management thinks is important. Let them hear it from the horse’s mouth.
-
Present the job as important. If people feel that PM is stupid, boring and low-priority fill-in work, they are less likely to put themselves out.
-
Let your PM mechanics themselves design the system and tasks. Train them in reliability, Total Productive Maintenance and general maintenance management. Then, let go of the reins.
-
Be explicitly certain that your PM people are fully trained. Someone with the title maintenance person, electrician or millwright must have the skill to perform the PM task. A test for PM certification might be appropriate.
-
Improve the relationship between the mechanic and the maintenance user. Where there is an operator such as a driver, machine operator or building contact person, instruct the mechanic to make personal contact. Some PM task lists include “talk to operator and determine whether equipment has operated normally since the most recent visit.”
-
Make it easy to do tasks. Simplify paperwork, re-engineer equipment to simplify the tasks, and route people to minimize travel.
-
Improve accountability by mounting a sign-in sheet inside the door to the equipment. Be sure the people who do the tasks sign a form and are included in discussions about the equipment. When people know they might be quizzed about an asset, they are more likely to complete their PM tasks. When people know that an inquiry is conducted after a breakdown and that the PM sheets are reviewed, they have motivation to complete their tasks.
-
Make PM a game. One supervisor got up a bit of money and bought 50-cent gift certificates at a local fast-food restaurant. Each week, he hid eight 3-by-5 cards (which said, “see me”) inside equipment to undergo PM. He traded the cards for the certificates.
So when a card wasn’t found, he knew PM hadn’t been done. His comment: “What people will do for 50 cents they wouldn’t do for $17.50 an hour!” -
Give your PM professionals new, better toys (sorry – better tools, not toys). Technology has opened up the field for sophisticated, relatively low-cost PM tools. They might include $700 for a pen-size vibration monitor, $500 for a cigarette-pack-size infrared scanner or $1,500 for an ultrasonic detection headset and transducer. If appropriate to the size and type of equipment, these tools motivate the troops and increase the probability that they will detect deterioration before failure.
-
Stave off boredom. In any repetitive job, boredom sets in. To improve morale, consider job rotation, reassignment, project work, and office work such as planning, design and analysis.
The last key to success is to ensure that the mechanic has the information, tools and materials to complete the job:
Actual task list, with space for readings, reports and observations.
-
Equipment manual (or ready access to the manual).
-
Standard tools and materials for short repairs.
-
Specialized tools or gauges to perform inspection.
-
Standardized PM parts kits.
People tend to wait till something goes wrong before acting. PM is diametrically opposite to human nature – it doesn’t happen organically. In this article, I hope you found some ways you may not have thought of to help PM survive.
About the author:Joel Levitt is a leading trainer of maintenance professionals. He has trained more than 10,000 maintenance leaders from 3,000 organizations in 20 countries in over 500 sessions. Since 1980, he has been the president of Springfield Resources, a management consulting firm that services all sized clients on a wide range of maintenance issues. He has almost 25 years experience in many facets of maintenance, including as a process control designer, source equipment inspector, electrician, field service technician, merchant marine worker, manufacturing manager and property manager. Prior to that Levitt worked for a CMMS vendor and in manufacturing management. To learn more, visit www.maintrainer.com or call 800-242-5656.
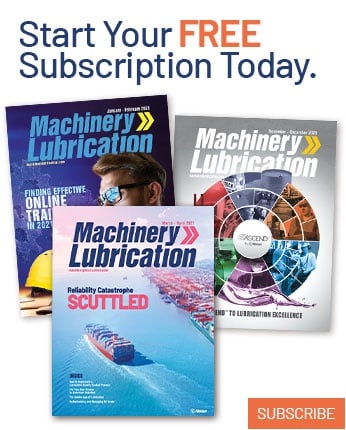