As a lean sensei, I try to live up to the standards set by my Japanese lean sensei as I teach the way of lean. Although I readily will testify that I am not perfect in my methods and have ample room for improvement, there are teaching moments that actually seem like magic. These wonderful, magical moments are where the student and the teacher hit the sweet spot. Things seem to fit together without force. Everything aligns and clicks. Excitement and joy are created, very much like the feeling around Christmas time.
I experienced one of those moments today with a group of my students (a rare case since this experience typically occurs just in one-on-one moments). I was leading a simple point lesson at lunch time with a small group of plant leaders from our Batesville plant in Indiana. The topic was the classic spaghetti diagram. The spaghetti diagram is a simple map indicating the path of a part or person through a process. As you draw the travel path back and forth, up and down, etc., the lines can resemble a bowl of spaghetti noodles.
For a point lesson, it is best to focus on one small topic and keep it short. Usually I target 15 minutes, depending on the topic. Following the short explanation (using little or no PowerPoint slides), I have my students try it. Learning by doing is the best way to understand. If done well and often, these point lessons can have a far greater impact than full-blown kaizen events.
I asked the students to go to gemba (the shop floor or office) to find a process of their choosing to map using the spaghetti diagram. I gave them a deadline of just the next 20 minutes. The group practically ran out the door to meet the deadline. I knew I would get a few good responses upon their return, but I was not entirely prepared for what happened next.
At the appointed 20-minute deadline, my students started funneling back. Everyone was excited about what they discovered in just 20 minutes. People were comparing stories and looking over the discoveries of the others. Many of the students were shocked at how much travel they just witnessed. Plenty of ideas were being thrown out to make improvements.
With that, I asked them to please make those improvements as tonight’s homework assignment due by the end of the day tomorrow. After making these improvements, I asked that each of them sketch out an after-kaizen spaghetti diagram and share it with the group.
In just a short, focused 35-minute session of learning by doing, we had more than 20 processes targeted for immediate improvement. Pretty awesome! I can’t wait to see the results tomorrow. It almost feels like I’m 7 years old again on Christmas Eve. I'll let you know what I find under my tree in a future column.
About the author:
Mike Wroblewski started his lean journey with instruction in quick die change from Shigeo Shingo. Mike is currently the lean sensei at Batesville Casket Company in Batesville, Ind. He also writes a blog called “Got Boondoggle?” featuring lean and Six Sigma topics. Check it out at http://gotboondoggle.blogspot.com/.
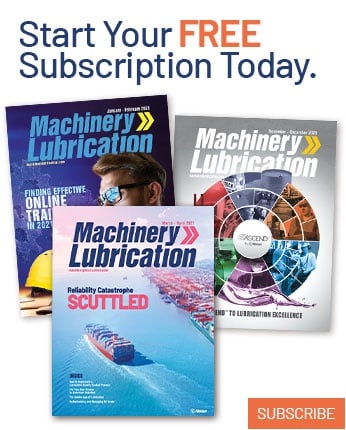