In his groundbreaking book "Good to Great", author Jim Collins takes a critical look at companies that have evolved to become great based on their share price performance relative to both the general market and a comparison company operating in a similar market under similar conditions. While the book identifies many factors which contributed to a company achieving "greatness", one of the most compelling arguments centers on leadership - and, in particular, what Collins refers to as "Level 5" leadership.
According to Collins, one of the key factors that differentiates a Level 5 leader of a "great" company from other key executives from companies who may be good but did not make the grade as "great" is personal humility. These people credit others for their company's success and blame themselves for small bumps along the road to greatness.
Re-reading this book recently, I was drawn to one section where Collins describes a behavioral pattern of Level 5 leaders. He calls this "the window and the mirror". Based on his research, Level 5 leaders looked out of the window to credit others for success and looked in the mirror to apportion responsibility when things didn't go to plan. Conversely, charismatic leaders from companies that didn't make the grade as great had a tendency to look through the window to blame other factors for their lack of success and looked in the mirror to take credit when things went well.
Having spent the past 12 years helping companies improve their lubrication processes and practices, my experience has been that organizations and those challenged with the task of leading lube improvements fall into two similar categories:
-
those that look in the mirror and recognize that there is room for improvement while looking through the window for solutions, and
-
those that look in the mirror and attest that they have done some good things while looking through the window for reasons why they can't achieve world-class lubrication.
Take, for example, the case of mines. By their very nature, mines are dirty, dangerous, difficult places to succeed at lubrication excellence. But, is this really a reason for poor performance or an opportunity for success? In my opinion, it really depends on whether you're a "glass half full" or "glass half empty" type of person. With the right leadership - again, what Collins calls Level 5 leadership - there's no reason why a mine can't be truly world class; it's all a matter of how much you really want to succeed.
In my career, I have met two types of maintenance professionals at mines:
-
those that can rebuild a 16-cylinder diesel engine with their eyes closed yet are not willing to step out of their comfort zone of blaming the heavy loads and dirty environment in the mine for "average performance", and
-
those that are constantly seeking improvement.
Take the example of the large diesel engine I wrote about in my last column, where improved filtration extended the rebuild life from 14,000 hours to 50,000 hours. That took Level 5 leadership to look outside of the current problems and challenges and seek opportunity rather than accepting mediocrity as the norm.
The manager who doesn't make the grade as great but is content with good (surely having the skills, knowledge and experience to rebuild the engine is good, right?) typically hides behind market conditions and the pressure to produce more while cutting maintenance costs as "reasons" why lubrication excellence can't be achieved. The Level 5 leader accepts this as a challenge and looks at the mirror to ask "what more can we do" while looking out of the window for solutions to long-standing problems.
As another example, I frequently run into discord between those charged with performing lubrication tasks on a daily basis and those who manage these activities. Talking to the technicians or operators, I often hear that "management" has no clue and that nobody listens to the problems they have been identifying for years. But when you talk to a manager, what you hear is that our people cause more lubrication problems than anything else, and all they do is complain. So, who's right? Does it really matter?
What's required to resolve this impasse is, again, a Level 5 leader - one who is prepared to listen to the concerns and feedback from the shop floor and, where appropriate, accept that change is needed (look through the window) while asking themselves if there could be a better way to procure equipment or manage the maintenance or production process to resolve the issues at hand (look in the mirror). While it's unrealistic to expect a maintenance technician or operator to be a Level 5 leader - though some truly are - this type of leadership is a fundamental trait that any successful maintenance and reliability leader needs to succeed.
So, ask yourself, when it comes to world-class lubrication, are you a Level 5 leader - one who aspires to greatness - or are you content with good?
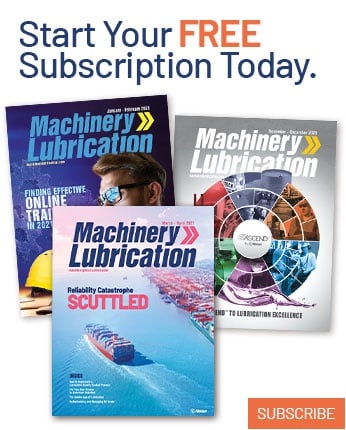