Some organizations still view operations as the customer and maintenance as the supplier. In my opinion, a customer-supplier relationship between operations and maintenance undermines equipment reliability improvements.
If maintenance is the supplier, what is it a maintenance department supplies? In the organizations where maintenance is a supplier to operations, maintenance usually supplies time and material to operations. Since operations pays the bill for the services supplied by maintenance, maintenance will always be viewed as a pure cost, not as a resource that can deliver value.
I believe the mission of maintenance should be to supply equipment reliability, not time and material, and I don't think operations can be the customer if you want reliability from maintenance. The reason is that operations doesn't understand equipment as well as maintenance, and it usually has a much more shortsighted view of the production process. For example, if one of your most critical pumps is down, would an operations customer ask a maintenance supplier to take extra downtime to align it to two-thousands of an inch? Would an operations customer listen to the maintenance supplier that recommends that you install oil sample ports on all hydraulics and lubrication systems?
Common problems often created with a customer-supplier relationship are:
-
Maintenance becomes more reactive because few operators see or understand the long-term effects of lubrication, alignment, balancing, preventive maintenance, etc.
-
Operations usually likes to have maintenance handy in case of a breakdown. Therefore, the amount of maintenance people on a shift increases.
-
"Honey-do" jobs that often aren't necessary increase because maintenance is more readily available.
-
Less preventive maintenance is done because there is more focus on reactive work.
Some organizations have drawn this system to an extreme with the "kid in the candy store with unlimited resources" mentality. Here, operations is the customer but doesn't have to pay for any services and has very limited responsibility for the maintenance budget. In my opinion, if you have a customer-supplier relationship, operations should at least be responsible for the maintenance budget.
THE PARTNERSHIPI strongly believe maintenance, engineering and operations should be partners in production. Production reliability is, therefore, defined as equipment reliability (where maintenance and maintenance engineering have primary skills) together with process reliability (where operations and process engineering have the primary skills).
If you are going to breed a partnership organization in your plant, I think the following work processes are key items:
-
Operations has a central contact point to screen and set preliminary priority on all work requests (notifications) coming in from operations.
-
Jointly decide what work to do and jointly prioritize work according to clear guidelines. A daily meeting (a maximum of 15 minutes) is the best way to accomplish this.
-
Jointly go through the backlog on a set interval.
-
Maintenance informs work requesters on the status of each job in the backlog.
-
Jointly perform root cause problem elimination.
-
Jointly tackle equipment and process inspection. Operations and maintenance have their own routes, but at least once a month, execute the routes jointly with a maintenance person and an operator. Report the inspection results to the operations and maintenance supervisors.
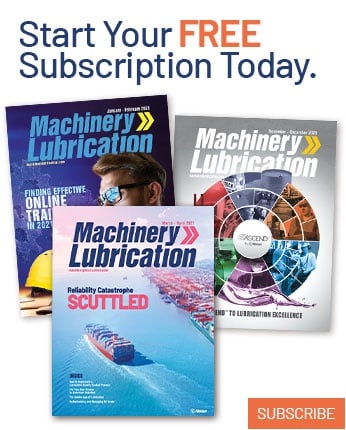