Pop quiz: What's the opposite of bright? Hint: It's not dim.
![]() |
For a Ford engineer studying the quality of sound, the answer is dull. The opposite of clear? Muddy. The opposite of tinny is boomy.
Of course, there are lots of ways to describe a sound — like, say, just too loud — but those are a few of the precise words Ford sound-quality engineers use to describe everything that enters the human ear.
“In sound quality, you can actually do some tuning,” says Alex Petniunas, a sound-quality engineer at Ford Motor Company. “When you design a particular vehicle, there are lots of things you can do to enhance the image. For instance, a big effort we’re involved with right now is the chime.”
He’s talking about the beep you hear when you leave your key in the ignition or when you leave your lights on.
“We’re not really expressing anything with these sounds today, so it’s the perfect opportunity to do something with it,” Petniunas says. “We can synthesize the sound at will.”
A team of engineers is trying to establish a brand sound DNA and get a note sequence — one for Ford, one for Ford Trucks and another for Lincoln. Look for custom, or maybe even downloadable, sounds for your Ford car or truck in the near future.
Still, “beeps” and “dings” are just two of many contributions to sound inside a car. Road, wind and powertrain are the traditional ways to measure noise, vibration and harshness levels inside a vehicle. There are also squeak, rattle and component sound qualities.
When building a car from scratch, sound engineers take all that into account and create a health chart, essentially a list of targets to hit when designing a vehicle. Sound engineers are involved from the beginning, making sure that the structure is rigid enough to not bend and squeak, that the electric seat motors don’t make a grinding noise when a user moves the seat back and that the doors make a solid “thud” when they close instead of a quality-bursting “tink.”
Engineers don’t just use their ears to study sound — there’s science to it, too. Laser vibrometry is where engineers put a source of vibration inside a car and then use light to measure what moves. During one recent test in the Ford sound laboratory, engineers put a home audio speaker on the center console of a Mustang. The speaker repeated a pulse that sounded like the “red alert” warning from the Enterprise on “Star Trek: The Next Generation.” The noise made parts on the Mustang vibrate, and a laser pointed at the doors, hood, dashboard, engine bay and other parts of the vehicle and measured what moved and by how much. Basically, laser vibrometry uses the wavelength of light as an extremely accurate measuring stick.
During another test at Ford, a perfectly machined, perfectly round brake drum was making an unpleasant noise in preproduction tests. Laser vibrometry revealed the problem: With the brake installed, the torque from the bolts used to install the piece made the brake slightly oval, which created a “thump, thump” sound. The solution was to instruct the supplier to machine the part with the proper amount of torque so that after the brake is delivered to Ford and re-torqued during the final assembly process, the brake part is a perfect circle again and the noise is gone.
Another sound-measuring test uses accelerometers. These are tiny sensors placed at contact points on a vehicle — a handful of them positioned on a steering wheel, for example. Just like with the speaker, engineers will create an input source (a drive over a bumpy road, for example) and measure the reaction, or acceleration, on the steering wheel.
“When you measure an item’s acceleration, you can measure how it moves,” says Petniunas. “If you stop that item from moving, you can eliminate or reduce the noise it makes.”
In the real world, he and his team used these methods to scan everything on the 2007 Ford Edge. Years ago, Edge engineers had made computer-aided design estimates in the advance prototype phase, and they recently came to the sound lab to verify their designs and make small tweaks.
“There is always more than one variable,” says Petniunas. “There might be three or four possibilities as to what’s causing a particular noise or sound. Once you eliminate one sound, you reveal another. Actually, cars are so quiet now, we are finding sounds inside cars we never knew were there before. Using these scientific test methods, we have a pretty good idea how to study sound and how to make the customer’s experience inside the vehicle as nice as possible.”
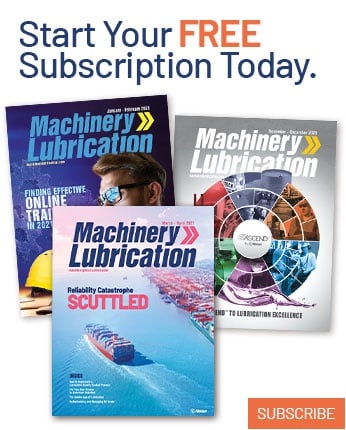