In past articles, I outlined why planning frustrates many companies and why many planners do not plan. I explained that serious frustration stems from incorrectly encouraging supervisors to wait on planning for all reactive work. I also wrote that planners commonly help jobs in progress to the extent that they have no time left to plan new work.
With these major issues addressed, this column enumerates all of the principles of a successful planning and scheduling program. The six planning principles and six scheduling principles listed on this page form the essence of my “Maintenance Planning and Scheduling Handbook”.
Planning Principle 1 requires keeping planners independent from the supervision of the individual crews. Supervisors commonly grab planners to help on jobs, making them unavailable for planning.
Planning Principle 2 is to have the planners (now available for planning) concentrate on planning future work rather than merely helping deal with delays of jobs already in progress. This principle takes advantage of the repetitious nature of most maintenance work and moves jobs up a learning curve.
Planning Principle 3 recognizes that planners can only practically retrieve prior job feedback to improve jobs if the file or computer system tracks jobs at the component level (e.g., a valve instead of a system).
Planning Principle 4 utilizes the expertise of an experienced technician as a planner (with perhaps limited history review) to estimate job labor hours. This avoids time-consuming techniques of building estimates.
Planning Principle 5 has this planner utilize the skills of the field technicians and avoid extra time giving more procedural information than necessary on initial job plans.
Planning Principle 6 reminds us that the purpose of planning is to reduce delays and help technicians spend more time on jobs.
Planning also involves scheduling because reducing delays during individual jobs allows supervisors to assign more jobs. Scheduling answers the question of how many jobs to assign. While the planning principles address major issues, the scheduling principles are more of a framework.
Scheduling Principle 1 obligates each job plan to estimate labor hours and craft skill levels.
Scheduling Principle 2 encourages not interrupting jobs already in progress through proper prioritization of work.
Scheduling Principle 3 commits crew leaders to forecast labor hours for craft skills available for the next week.
Scheduling Principle 4 combines all of the forecast crew labor hours with the estimated labor hours of the planned jobs, generally in order of job priority.
Scheduling Principle 5 has crew leaders schedule and assign daily work (even though the planning department allocates the week’s goal of work).
Scheduling Principle 6 establishes the importance of measuring schedule success. Measuring this outcome helps management insure that planning and scheduling does take place.
Finally, maintenance must acknowledge reactive work. Management must assure crew leaders that for urgent work, it is OK to work an unplanned job and it is OK to break a schedule. Planning must not constrain crews from immediately beginning work on urgent jobs. Nevertheless, planning can abbreviate its efforts on urgent work and many times produce a helpful job plan before maintenance begins work.
Allowing crews to work unplanned work and break schedules is vital to consider, especially for reactive plants. If it is OK to work on unplanned jobs and break schedules, where is the productivity gain? Actual experience shows that simply starting each crew every week with a sufficient allocation of work as a goal significantly boosts crew productivity, usually in excess of 50 percent.
This column and my previous two are most appropriate for readers that already recognize the value of a planning program. My column in the January/February issue will address and quantify the value of maintenance planning. Future articles after that will review the principles in greater depth and will also handle individual issues that commonly arise in planning efforts.
Doc Palmer is the author of the “Maintenance Planning and Scheduling Handbook.” He is a CMRP and has nearly 25 years of industrial experience as a practitioner within the maintenance department of a major electric utility. From 1990 through 1994, he was responsible for overhauling the existing maintenance planning organization. The resulting success played a role in expanding planning to all crafts and stations owned and operated by the utility.
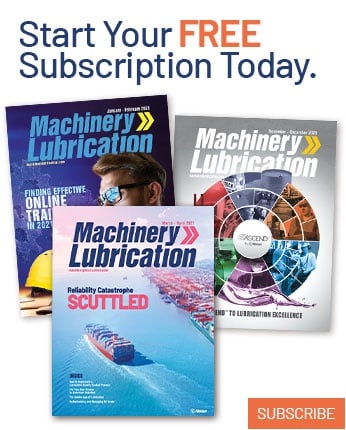