A combination of technical assistance from the U.S. Department of Energy’s (DOE) Industrial Technologies Program (ITP) and financial incentives from Silicon Valley Power (SVP) enabled the Owens Corning plant in Santa Clara, Calif., to implement numerous energy savings projects. Over a two-year period, the Santa Clara plant received a Save Energy Now assessment from ITP as well as two additional assessments that used DOE software tools and the Save Energy Now methodology. The plant also received approximately $251,000 in rebates from SVP to implement energy-efficiency measures that were generated from these assessments.
The initial Save Energy Now assessment was performed by DOE energy expert Joe Junker on the plant’s pumping systems in 2007. Junker used DOE’s Pumping System Assessment Tool (PSAT) to identify several opportunities for reducing pumping system energy use, including consistent operation of the most efficient pumps, retrofitting inefficient pumps, replacing valves and installing variable speed drives (VSD).
Subsequently, plant personnel evaluated some of the plant’s fan systems, and SVP fully funded an evaluation of the compressed air systems performed by SBW Consulting, a company that conducts Save Energy Now assessments for DOE. Both the fan and compressed air system assessments used the respective DOE software tools: the Fan System Assessment Tool (FSAT) and AIRMaster+. The assessments led to implementation of several energy-efficient upgrades, including installing variable frequency drives (VFD) on fans and upgrading a large compressor.
The recommendations implemented by the Santa Clara plant resulted in aggregate annual energy cost savings of $252,000. With $251,000 in incentives from SVP, implementation costs totaled $325,000, resulting in a 1.3-year simple payback period.
Company/Plant Background
Owens Corning is a leading global producer of residential and commercial building materials, glass fiber reinforcements, and engineered materials for composite systems. The company, known for its PINK Fiberglas insulation products and famous corporate mascot The Pink Panther, was founded in 1938 and generated $6 billion in sales in 2008. Owens Corning employs 17,000 people in 26 countries and produces more than 2 billion pounds of fiberglass insulation annually.
Built in 1949, the Santa Clara plant was the first industrial plant in the United States designed specifically to manufacture insulation. Today, the plant employs 300 people and produces approximately 250 million pounds of insulation annually. Because the plant is served by two large electric furnaces, electricity consumption is significant. The Santa Clara plant is also served by several pumping and fan systems, and two compressed air systems.
Utility Background
Silicon Valley Power (SVP) is the trademark for the century-old Electric Department of the City of Santa Clara, Calif. This municipal utility serves more than 50,000 customers across the industrial, commercial and residential sectors, and is also an active participant in the wholesale energy market in the western United States.
For SVP, large industrial facilities like the Santa Clara plant are not only important customer loads, but are also valuable assets to the community. Helping industrial customers use less electricity is important for SVP because it ensures the customers’ economic viability, which keeps manufacturing jobs in the community, attracts new businesses and helps to keep power costs low by spreading fixed costs across sectors more evenly. As a result, the utility’s rising load growth can be met without building more power plants, mitigating SVP’s carbon footprint.
SVP has used its Customer Directed Rebate program since 1999 to offer incentives to customers for implementing energy efficiency measures. The rebates are paid based on customers’ actual reductions in energy use that result from well-designed energy efficiency projects. Since the Customer Directed Rebate program began, SVP has awarded an average of $2 million per year in rebates, yielding total energy savings over the past 10 years of more than 165 million kilowatt hours (kWh).
SVP actively participates in a collaborative effort between ITP, utilities, utility associations, state energy offices and power administrations to help reduce industrial energy intensity 25 percent in 10 years. This partnership between the utility sector and ITP helps raise awareness about Save Energy Now assessments and encourages companies to improve their energy efficiency and make a positive impact on the environment. In SVP’s case, this effort has helped strengthen its relationship with the Santa Clara plant.
Energy Assessments
Pumping System: During the pumping system assessment, the DOE Energy Expert evaluated several pumps using the PSAT and identified a number of energy savings recommendations. Energy expert Junker teamed up with Owens Corning employees, including the energy leader, who in turn worked with SVP to review each opportunity for technical and economic feasibility.
The assessment generated three opportunities estimated to have little or no capital cost and short-term paybacks. These included:
- Perform regular evaluations of pump efficiency and consistently use the most efficient pumps in redundant systems;
- Reposition tank discharge lines; and
- Re-evaluate flow rates to reduce excessive flows.
Several other recommendations were more complex, but would significantly increase pump operating efficiency and reduce energy use:
- Trim the impeller or replace the pump with a more optimally sized unit on a treated water system. This would improve pump efficiency over the current operating efficiency of 56 percent.
- Replace the pressure reducing valve with a VSD on another treated water system. This system, at times, was found to have intermittent excess flow that was directed to the sump through a bypass line. A VSD would regulate the pump to optimize the required flow rates and energy consumption.
- Install more optimally sized pumps for the systems serving the wash water spray process and the binder lines.
- Retrofit the pump serving the industrial water supply with a smaller unit fitted with a VSD to lower the system’s energy use and eliminate excess flow.
The combined annual energy savings for all these measures was estimated at $122,000.
Fan System: Based on the positive results from a Save Energy Now fan system assessment performed at an Owens Corning plant in Newark, Ohio, the company formed a corporate fan system assessment team in 2007. The team successfully coordinated fan system assessments at the Santa Clara and other Owens Corning plants using DOE’s FSAT and the systems approach utilized at the Newark facility.
The internal evaluation conducted in Santa Clara yielded several efficiency project proposals with significant energy savings potential:
- Install VFDs on the large dust collection fans (Penclones) serving each of the two production lines. The upgrade was estimated to yield annual energy savings of 361,000 kWh.
- Install a VFD on a large oven fan to save an estimated 398,000 kWh per year.
In late 2008, an additional fan system evaluation using the FSAT generated a proposal to install a VFD on a large forming fan. This measure was estimated to yield up to 3.2 million kWh in energy savings per year and is under serious consideration.
Compressed Air System: Also in 2007, the Santa Clara plant received an assessment on its two compressed air systems. The assessment was completely subsidized by SVP and was performed by Lynn Qualmann, a DOE energy expert with SBW Consulting. Qualmann found that one centrifugal compressor did not generate the amount of air for which it was rated and was at the end of its useful life. He recommended replacing the aging compressor and maintaining a crossover valve that connected the main headers of both systems in the open position to allow the process system to support the main system. By taking these steps, the plant could save more than 2 million kWh annually.
Results
Following each assessment, personnel at both the Santa Clara plant and SVP were eager to implement the energy savings measures. Initially, the implementation costs were too high for the measures to meet the established three-year corporate financial hurdle rate to qualify for project funding. However, SVP recognized the benefit in reducing the plant’s energy use, and leveraged the Customer Directed Rebate program to help defray some of the project costs. Working with personnel at the Santa Clara plant, SVP’s public benefits program coordinator developed a strategy to make many of the projects more cost-effective with a series of strategic rebates.
These rebates enabled personnel at the Santa Clara plant to replace a pressure-reducing valve with a VSD on the treated water pumping system and to install a VSD on the wash water spray process pump. The VSD on the wash water spray process pump not only reduced that system’s energy use, but also reduced a considerable amount of cavitation, enhancing equipment life. The implementation of these measures achieved annual pumping system energy cost savings of approximately $67,000. With a $9,000 rebate from SVP, the implementation costs were approximately $22,000, leading to a four-month simple payback period.
After successfully implementing the recommendations of the pumping system assessment, plant personnel carried out the following energy savings projects based on the analyses of the fan and compressed air systems:
- Install VFDs on the two Penclone fans and one VFD on the large oven fan. These improvements are yielding annual energy cost savings of more than $65,000. With $32,000 in rebates from SVP, project costs were more cost-effective for the Santa Clara plant at $62,000, which led to a simple payback of 11.5 months.
- Replace the aging compressor. Again, strategic rebates from SVP of $211,000 reduced implementation costs to $244,000, making this project possible. With annual compressed air energy cost savings of approximately $120,000, the simple payback period was just over two years.
Overall, SVP provided approximately $251,000 in rebates to the Santa Clara plant. These projects resulted in total annual energy savings across all three systems of $252,000. With total implementation costs of $325,000, the plant achieved a 1.3-year simple payback.
Lessons Learned
Strategic relationships between companies and utilities can lead to greater implementation of energy savings measures and result in a win-win situation for all parties involved. At Owens Corning’s Santa Clara plant, some recommendations from assessments using DOE tools were too costly to initially merit project financing. By working with plant personnel and offering strategic rebates to make many of those measures more cost-effective, SVP enabled the Santa Clara plant to qualify for internal, corporate project financing for many of the projects. The Santa Clara plant realized substantial energy savings and SVP was able to satisfy its load without bringing peak power generation assets online as often, keeping average power prices low and reducing emissions.
About Save Energy Now
Save Energy Now is a national initiative of DOE’s Industrial Technologies Program to drive a 25 percent reduction in industrial energy intensity in 10 years. Save Energy Now energy assessments help industrial plants operate more efficiently and profitably by identifying ways to reduce energy use in key industrial process systems. State and federal agencies, utilities, industry associations, and others can partner with ITP to leverage Save Energy Now resources and help companies boost their energy efficiency. Learn more at www.industry.energy.gov/saveenergynow.
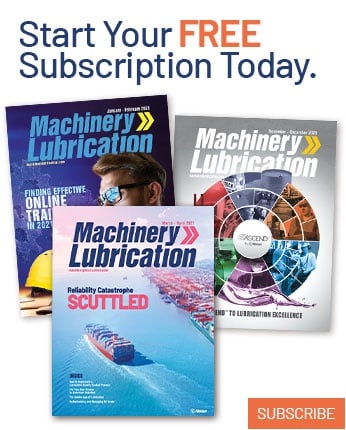