The greenhouse effect and global warming. Rising fuel costs and dependence on foreign oil. A crumbling infrastructure and a massive economic stimulus and recovery package. All of these concerns are inextricably linked together, and all of them can be addressed, in part, through better, more environmentally sound manufacturing and shipping materials.
“When people think of environmental awareness, they tend to think of fuel consumption and carbon emissions,” says Wayne Rodrigue, chairman and chief executive officer of Texas-based Exousia Advanced Materials. “However, the materials used in manufacturing and shipping impact everything from depletion of natural resources, to being smarter about recycling and fuel consumption. A reconsideration of materials technology is vital if we are to begin to get serious about the environment.”
Exousia is creator of two core advanced polymer materials, RPA Resin and VISTAMER engineered particles, that are used in an array of products including proprietary resins, additives, industrial coatings, and structural materials used in the manufacturing and construction industries.
An eco-friendly alternative to wood and nylon for the transportation and plastics industry, RPA Resin is a family of polymers used as a manufacturing material in high-volume production. A proprietary TPO (Thermo Plastic Olefin) resin that bonds rubber and plastic, RAP Resin enables Exousia to develop, manufacture, and market a wide range of advanced composite materials with enhanced performance characteristics.
“These new materials have high-volume applications in the automotive, building, recreation, maritime, and household goods industries,” explains Rodrigue. “RPA solutions can be developed to replace wood, fiberglass, Luan, and other plastic materials across a wide range of applications.”
The key differentiator of RPA is that it successfully bonds plastic and rubber materials to form a new category of composites. RPA enables the development of new thermoplastic-elastomer alloys that overcome earlier problems of poor strength and performance. This provides a degree of rubber-plastic compatibility not previously achieved, and results in a thermoplastic blend with a highly improved tensile strength and elongation capability.
“Moreover, RPA Resin is markedly lighter than the materials it replaces,” says Rodrigue. “A composite material that uses RPA, TRUSSCORE can be used as a structural component that replaces fiberglass reinforced plywood or similar natural materials in various applications such as marine decking. This means cargo boxes and chassis that use the material will be lighter and require decreased fuel expenditures, making this an environmentally friendly solution.”
Exousia’s other leading polymer material, VISTAMER, is a performance additive made from a fine black powder of crumb rubber that originates from recycled tires. When mixed with plastics, concrete, epoxy, latex, or polysulphides, VISTAMER becomes part of the material matrix and chemically alters the surface of coatings, in ways similar to Velcro.
“Intended for use in bridges, highways, cranes, and ships, VISTAMER binds materials to surfaces with 30 to 40 percent greater adhesive strength, thereby improving impact resistance, tear resistance, adhesive strength, traction, durability, flexibility, and abrasion resistance,” Rodrigue explains. “VISTAMER ensures less peeling and rusting, and better protects surface coatings and substrates.”
In September 2008, Exousia opened a 30,000 square foot industrial coatings facility in Tianjin, China, cementing a long-term commitment to the Chinese market. As America and China gird themselves for massive infrastructure refurbishment projects, the cost-saving and environmental implications of Exousia’s material solutions are profound.
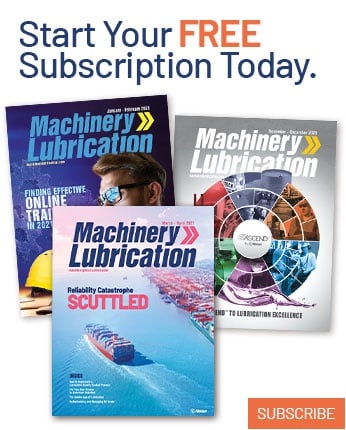