EIGHT-CYLINDER DIESEL ENGINE, 2000-2007: Maintained with loving care by one owner. Died suddenly at work due to liner failure. Will be sadly missed by all colleagues who respected and admired an unparalleled work ethic and a commitment to get the job done despite a less-than-ideal working environment.
It is with great sadness that I announce the passing of a dear friend. Not the human kind, but a dirty, smelly, noisy eight-cylinder diesel engine used in a front-end loader. This particular loader, like most, was used in a less-than-ideal environment, exposed to dust, dirt, rain, snow and cold winter temperatures, all of which can make for challenging conditions for any machine. Coupled with this, the loader was used almost constantly (approximately 8,000 hours per year), with the operators habituated to leaving the engine idling during shift changes, again not recommended for extended periods of time.
But rather than mourn the sudden failure of this beloved engine, I'd like to take a few minutes to celebrate its life. You see, this engine lived a full and long life: 50,000 hours to be exact! The secret to its success? A clean and healthy lifestyle.
When I first met this engine back in 2000, it was equipped with a standard full-flow filter, rated at 10 micrometers (µm) nominal. But understanding that one of the easiest ways to extend engine life is through cleaner oil, a supplemental bypass filtration system was installed. Designed to draw a small amount of oil (5 to 10 percent) from an oil gallery immediately after the full-flow filter, the bypass system filtered this oil through a 3 µm absolute filter back to the engine sump. By doing so, oil analysis revealed a 3 to 4 ISO code improvement in fluid cleanliness, equivalent to eight to 16 times cleaner fluid.
When purchased new back in 2000, the recommended rebuild life was 14,000 hours, assuming a time-based rebuild strategy. This figure is, of course, very conservative, designed to insure that a rebuild happens before a catastrophic engine failure occurs. Through the application of oil analysis to drive condition-based rebuilds, it's not uncommon for engines in this type of machine or application to last 20,000 to 25,000 hours. But 50,000 hours? That's nearly unheard of.
The secret again is aggressive contamination control. With engines, the main culprits are the 1- to 10-micron particles that enter though the air intake and cause ring-to-cylinder wear, ultimately leading to scuffing of the liner and other oil-wetted components. By removing these particles, the impact of three-body abrasive wear is significantly reduced - hence, the extended engine life.
So, what does all of this mean to the cost to maintain this engine? For this particular model of engine, the estimated rebuild cost is $150,000. Based on a 14,000-hour rebuild interval and 8,000 operating hours per year, that's equivalent to a rebuild every 1.61 years, at a cost of $85,000 per year. Through the application of oil analysis and a hypothetical condition-based rebuild interval of 22,500 hours, this cost drops to $53,000 per year, or a savings of $32,000 each year. But the real key to maintenance cost reduction is contamination control. Through aggressive contamination control, this engine lasted 50,000 hours - equivalent to one rebuild every 6.25 years, or an annualized cost of just $24,000. But wait, how much did this all cost?
The initial purchase and installation price of the bypass filter was approximately $1,000. In addition, the bypass filters were changed at every oil change (500 hours) at a cost of $200 per filter, or an added $3,200 per year in maintenance costs. But compared to the savings in rebuild costs, these expenditures are insignificant. In fact, if you look at the investment analysis on the preceding page, the net present value return is a staggering $210,000, a rate of return of 5,851 percent!
So, why am I so sentimental about this particular engine? Well, you see, this was my first venture into contamination control. Yes, I had read all of the case studies. I spoke to those who had done this before. I even taught classes on the impact that clean oil can have on machine life. But for me, this was first-hand experience that this stuff works! Success didn't come on the pages of a magazine, but in a dirty, smelly, noisy diesel engine.
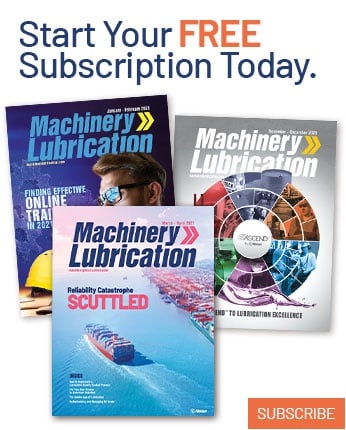