This paper offers a view on the current and future state of maintenance as seen in each region of the world. The topics that will be addressed and discussed are:
- Regional strengths and weakness in maintenance
- Current trends in maintenance management
- The value of maintenance associations around the world
- The future of maintenance societies and certification programs
- Effective practice in maintenance and maintenance management
- The future of asset management and how it is different from maintenance management
- Ten tips for successful implementation of improvements and change in your organization
INTRODUCTION
The maintenance world is evolving just like anything else around us. New methods, processes and techniques are constantly being developed, tested and implemented. Every company wants to produce as much product as possible, at the lowest cost, with the highest return, at the best efficiency rate and, of course, without running their assets to the ground. As companies change, so do the regions’ maintenance societies. Societies are becoming more sophisticated and continue to attract new members. Practitioners participate in these societies as a way to network with colleagues, educate themselves and their peers, and keep in touch with new trends. Current trends are slowly eliminating maintenance management and replacing it with asset management. But what does an efficient asset management program look like?
A VIEW OF MAINTENANCE BY REGION
I have taken the liberty to divide the world into seven regions; North America, South America, Europe, Australia, Asia, Africa and the Middle East.
Currently, North America seems to be improving as maintenance programs begin to gain traction and sophistication. However, some 75 percent of companies still continue to focus on reactive maintenance. There is also a trend in manufacturing to focus on lowering production costs without investing in people and processes. In addition, there is too much emphasis on reliability engineering and not enough on planning and scheduling. Many large companies have seen the light and are realizing that a common system across all plants is necessary to run a successful maintenance program. In this case, petrochemical companies are doing well, but mining and metals are still far behind. Furthermore, organizations such as the Society for Maintenance & Reliability Professionals are helping educate and spread the word about asset management.
My view on South America only focuses on the countries that we have had experience with, those being Brazil, Columbia and Venezuela. The manufacturing community within Brazil seems to have a strong interest in maintenance improvement. This is clearly visible through the rapid growth of Abraman, Brazil’s leading maintenance organization that is focused on aiding and educating its members. In addition, many companies such as Wood Group appear very advanced in their study and application of best practices. We also see the same trend at the region’s oil companies, which are also implementing global best practices throughout their organization.
Europe is a region that pioneered National Maintenance Societies, but the availability of maintenance and operations consulting services is limited everywhere except in the United Kingdom. Most companies and industry professionals have much interest in maintenance models and theory. However, in some cases, theory may be more important to them than demonstrated results. There is much more talk than action in maintenance improvement. Many companies still have strong emphasis on the skills of their craftsman, but this is most likely just a way to compensate for poor maintenance planning. The downsizing and cost reduction trends started later in this region than in the United States, but now there is a very big concern for competitiveness.
Australia is a region that, in many cases, is more advanced in its thinking and practices surrounding maintenance. Maintenance has always been a major focus of companies within the Australian region since replacement parts are not as easily available as in other regions. Also, unlike in other regions, Australian universities offer the most advanced programs in maintenance and reliability, educating and training new, future practitioners. Today, the natural resources economy is booming and new construction has been deemed as much more important than maintenance. Therefore, resources are being stretched to produce more and little emphasis is being placed on maintenance improvement.
Asia is primarily focused on discrete manufacturing where Total Productive Maintenance is widespread and ingrained into the culture. China is a huge manufacturing economy, but for the moment, there is very little interest in maintenance improvement. Reason being, most plants are new, and labor is generally high quality and inexpensive. India faces a very similar situation where labor is very cheap, but maintenance is extremely weak. Russia is an exception to the region; it’s mainly a minerals-based economy and there is a very strong interest by engineers for maintenance improvement programs.
The Middle East has some very good plants for the national oil companies. However, maintenance is generally poor and equipment is often replaced instead of maintained. Currently, many western engineers are beginning to influence the region and as this continues, the focus on maintenance will begin to increase.
Africa can be divided into two sections, North Africa and South Africa. The situation in South Africa is somewhat similar to Australia. That is, supply lines are long so maintenance gets higher levels of interest. However, the lack of education for blacks must be improved if they want to achieve the high potential that is available. As for North Africa, its manufacturing is mainly petrochemical working with the national oil companies. Much of the maintenance here is related to the learning’s from the major oil companies prior to the nationalization of the oil industries.
CURRENT TRENDS IN MAINTENANCE & ASSET MANAGEMENT
We are currently seeing a “Re-centralization” in the world. There is a shortage of resources as cost-cutting (downsizing) and the retirement of Baby Boomers continues. Many companies are finding the need to hire skilled workers, but are having trouble doing so. Shell Oil expects to hire some 10,000 people within the next five years. We are also seeing the availability of replacement capital becoming harder to come by, which is leading to a need for longer equipment life. As a result, companies will be forced to implement common systems across all plants globally.
Also, the “Maintenance Council” structure within organizations will require change in order to be effective. Current councils have too much democracy and not enough leadership. You cannot lead an organization solely with democracy. As organizations gain a better understanding for maintenance management they are beginning to realize that it is not only maintenance but total asset management that will lead them to success. As this trend continues, the concept of “maintenance management” will be replaced by “asset management”. Finally, the term “operational excellence” has become a global buzzword, but most organizations are having trouble figuring out what it means to them internally. The meaning of operational excellence seems to change from one organization to another.
MAINTENANCE SOCIETIES
Maintenance societies have been evolving and growing ever since their inception. Today, there are societies in every region of the world helping educate and train industry professionals. The meetings and conferences held continue to get more sophisticated and better attended. Currently, the most valuable maintenance societies are SMRP in North America, Abraman in Brazil, and MESA in Australia. These societies continue to flourish and gain new members annually. SMRP has taken on an international approach and is reaching out to global partners who will help spread the Certified Maintenance and Reliability Professional certification worldwide. However, of all maintenance societies, Abraman is the leader. They have been extremely successful in creating value by developing strong education programs for crafts, creating a certification program, and developing a presence in all industries. Surprisingly, the weakest society is the European National Federation of Maintenance Societies (ENFMS). Although ENFMS has done good work and continues to deliver value, they have failed to represent most businesses and are very resistant to change and improvement.
The future of maintenances societies seems to be leading in the direction of world congresses, where various organizations will team up to organize conferences, seminars and trade shows. The focus of societies must be on continually influencing the quality of manufacturing and industry for the country or region it represents. These societies must help set standards in industry as well as educate and train practitioners. A major opportunity for maintenance societies is the combination of certification programs. Rather than having different certification programs for each organization, societies need to work together and merge their certifications into one globally recognized program. This global combination of certifying exams and programs would create a global standard, greater education, and improved recognition for practitioners around the world.
As we continue to see the shift from maintenance management to asset management, the need for an asset management society will also develop. Such a society will stretch beyond maintenance and include the other areas of production, logistics and engineering. The participants will be manufacturing executives, global team leaders and plant managers from all functional areas gathering together to network and learn from one another. This would truly be a diverse group of practitioners sharing their industry experience.
EFFECTIVE PRACTICE IN MAINTENANCE IMPROVEMENT
So what works in maintenance improvement? Over many years of reviewing consulting successes and failures, we have been sharpening a model that is nearly always successful. It is called the SAMI Closed-Loop Improvement Process (Figure I), illustrated below.
Assess and Plan. Getting people engaged for change is the first step, and this is done through the Assess and Plan step of the Closed-Loop Process.
Outcomes from the Assess and Plan steps include:
- Creates a strong emotional gap
- Engages operating management to plan the future
- Develops a functional operating vision of the future
- Creates a forum for agreement
- Creates a multiple year road map
- Identifies expected value of change
- Develops a detailed plan of delivery
- Develops detailed goals by BU
- Aligns leadership!
First, we must understand something that is a bit of a mystery for most: change doesn’t happen because of understanding or knowledge. Change happens because of PASSION!
The human is likened to an automobile. We steer with our minds, but the drive train is our emotions. If we want change, we must feel strongly about it. And, what feelings might these be? Pride in what we do, and looking for praise is a positive way to approach things, and can lead to success. Caring about our co-workers, wanting the team to perform at a peak capability, loving the business we are in and wanting to perpetuate all the good that is inherent in it — these are excellent motivators for change.
In the Operational Strategic Planning phase, we create a forum for middle managers to review their common progress and gaps, and to decide collectively whether they will address the gaps. This is much more positive than a top-down directive. They develop an emotional bond to “go and get this fixed once and for all”. We help them look at what is on the table, what is real, what could be combined. In the end, several major initiatives are combined into a single implementation plan, and a single implementation team is set up to help them.
Finally, a compelling business case is constructed. It is detailed and owned by the middle managers who have the responsibility to deliver it. And since the initiative has the support of all upper-level executives, CEOs, presidents, vice presidents, everyone understands the importance of this effort.
Design. What are we going to design? How do we organize our efforts?
The Asset Healthcare Triangle (Figure II) helps people see where they have gone wrong in the past. Many times too much emphasis is placed on higher level activities without having the enabling base of the triangle in place. So the design objective is usually clear: Stage 1 activities, driving change.
In most major companies, there is a “Book of Maintenance Processes”. By bringing a team of strong field leaders to an eight-week design and validation project, they add, change and modify the system into something that would really work in the field. The team of maintenance planners and supervisors is chartered to decompose and reconstruct “the process”. At the end of the Design phase, the team is absolutely convinced of the necessity to implement the new work processes in the field. They are on fire, with passion! The next step is set-up, Install, so that these passionate team members become the Champions to deliver the training and coaching.
A quote from Margaret Thatcher might reinforce the point: “Look at a day when you are supremely satisfied at the end. It's not a day when you lounge around doing nothing; it's when you've had everything to do and you've done it.” This is the constructive view of the design team for the new processes.
Outcomes from the Design step include:
- Work process details, including training, SAP revisions, roles and responsibilities, etc.
- Multifunctional team, first- and second-line engagement and empowerment
- Integration of all inputs into a workable system
- A scorecard with key performance indicators and targets
- Passion about the system and the need to change
- Team members become coaches
Install. Some companies tend to think that the implementation is complete once the training is completed. However, that is not the case. Implementation means when the desired behavior is firmly established, and the renewal processes have been developed. Install is only the first step in implementation. One must still Sustain and Certify to achieve a lasting result.
The installation begins with training on process and tool revisions developed by the Design team. This training is the easy part because the real work starts with coaching the “20-year veterans” on this new and better way of working. The success of Stage 1 improvement always hinges on the ability to plan and schedule with discipline. Many hours were spent, on and off-shift, individually coaching schedulers to embed the techniques and the disciplined behaviors required to better manage the platform resources.
After the endless retorts of “but we’ve been doing it this way forever”, the operators and maintainers were coached on the new expectations and behaviors required not only to execute the work, but also to document their actions. The Shell Champions were diligent in their explanations of why the changes were required and communicating the need for patience to see results.
The Owners Group (OG) is another critical part of the implementation activity, providing active direction during the entire course of the work. The OG had line managers, including senior managers, who are committed to project review and management. This level of commitment along with the reporting systems, assure complete visibility to schedule, performance, and behavioral indicators.
To assure a smooth and complete installation of the system, the start dates are divided into several waves of implementation by three to six months.
To assure proper training of enough staff to implement the system in all locations and support knowledge transfer between locations, we designate staff from Wave 2 to help with Wave 1 installations. In this way they learn the system completely when they lead Wave 2 work. Likewise with Wave 3 and beyond, expediting implementation and reducing total costs.
Outcomes from the Install step include:
- Install trains, sets expectations, establishes roles, responsibilities
- Owners Group initiated. OG watches, steers, owns implementation plan
- Line Management owns change and results
- Waved Implementation, not big bang
- Wave 2 work on Wave 1, Wave 3 on 2, etc.
- CCC — Champions, coaches, consultants deliver behavior change with the worker
Sustain.
Outcomes from the Sustain step include:
- Key Performance Indicators (KPIs), System Implementation Schedule measured weekly
- CCCs show how to change
- Owners Group reviews progress, shifts resources, solves problems.
- Line management reviews results daily, weekly. Challenges for change, sets example
- Behavior and attitude measured monthly
- Goal — ”I prefer to work this way!”
Our coaching model is to have full-time coverage in all major areas. SAMI’s consultants worked back to back hitches, overlapping with crew changes to ensure consistency. This model of real time, “trench” coaching inspires confidence in the team that “the consultants are in this with me” and “they understand our challenges.” From a tactical perspective, this coverage allows early detection and correction of behaviors that would not sustain performance improvement. Just as important, it allows for positive reinforcement when the behaviors are appropriate and maintains the enthusiasm for continued change.
Of course, without measures, we wouldn’t know the composite effects of the new behaviors. When measures are made public and given attention by leadership, there is often a strong drive to meet or exceed targets. Sometimes we find the actual behavior is one to show good KPIs without actually following the process. This is another reason coaches, champions and consultants are critical to the real success of the project. Beating the numbers can be easy unless someone is watching closely just how that’s happening.
At the same time, the Owners Group operates, results are reviewed at the highest level of the company in weekly performance meetings. Line managers were held accountable for schedule and KPI compliance, and have to explain variances on a weekly basis. This level of review and governance makes the outcome an assured full success.
Certify. This is the final step. It answers the question, “How do we know when we are done?” Too often the answer to this question is, “When the time or money runs out!”
Certify does the following:
- Sets performance standards
- Periodically reviews KPI’s & behavior
- Recognizes achievement
- Enables unit to move to next stage of development
(See SAMI Pyramid— www.samicorp.com )
Certify differs from an audit in subtle, but important ways. It is completed by others who have done the implementation and have been certified. Through peer evaluation, best practices can spread in a very natural fashion, as variations of a like system. The purpose is to improve, rather than an audit which has negative connotations, like a report card. Certify evaluates whether behaviors are in place and continuing or improving from the prior state, assuring that the reporting isn’t simply to show good numbers, but is actually rooted in new behavior.
Based on passing the current standard (we use a flexible tool we call CARAT to help automate the reviews), each area/division is now ready for Asset Healthcare Stage 2, Proactive Maintenance.
Illusions of Change to Avoid. You can fool the numbers. You must look at behaviors, see the system compliance and the hearts of the people, before you know if the system has taken root.
Standalone training can be destructive. It sets up a new expectation of behavior, but as one re-enters the real world, nothing is different. This sets up a conflict, and the conflict is often resolved by resistance and criticism of the new process
Implementing without creating an emotional gap seems faster, but always dies out. Taking the time up front to gain alignment and passion may seem the slow way to get things done, but in fact such actions assure success.
DIFFERENCE BETWEEN MAINTENANCE MANAGEMENT & ASSET MANAGEMENT
We have developed a table that depicts the Functional Excellence Model (Maintenance Management) and Asset Management Excellence Model (Table I). By comparing the two, one can very easily see what the difference is between the models.
Functional Excellence Model Operations owns production, maintenance owns equipment. Maintenance excellence means efficient service (e.g. repairs) to production. A customer service model dominated by operations. Most work is inside planning time horizon. Repair efficiency is the best measure of maintenance performance. No time to do it right, but hope there is time to do it over. Production runs at any cost. Don’t have time to turn equipment over to maintenance as scheduled. Goals are set by functional managers, resulting in contradictory and self-defeating reward/recognition practices. Most measure are lagging indicators, demonstrating past results. Purchasing excellence means having the lowest cost of items available. Pressure is on individuals to do better. No gauges or tools of “better” exist.
|
Asset Management Excellence Model Operations owns equipment and is responsible for equipment health. Maintenance is a partnership with operations to identify and work ways to improve equipment health. Breakdowns represent an unacceptable management system failure, and require failure analysis of equipment and process. Production insists on and participates in assuring prevention and improvement activities. Goals are developed top-down in a cascaded fashion. Functions share lagging indicator goals (e.g. monthly production), and have unique leading indictor goals that support activities (e.g. % of PMs performed to schedule). Purchasing and inventory management’s highest goal is parts service level and mean time between failure for purchased parts. Each piece of equipment has an operating performance specification, and gets the attention necessary for it.
|
Table 1 : Functional Excellence vs. Asset Management Excellence
James Davis stated in his paper “Strategic Planning for Asset Management” that in the past, reliability improvement initiatives have been restricted to site-level programs that achieve impressive results at individual manufacturing sites. These benefits often are lost due to management changes, failure to establish a reliability culture and a lack of senior management support. The ability to duplicate results across multiple sites is restricted due to cultural differences, lack of consistent business processes, and plain old territorial jealousies. Strategic Asset Management (SAM) programs are designed to overcome these deficiencies and achieve significant and sustainable improvement in corporate business processes and financial performance.
The benefits of a successful Asset Management Strategy include:
- Accurate analysis of equipment maintenance, repair, and replacement records.
- Increased availability of production systems and equipment.
- Fewer failures of production systems and equipment, resulting in fewer unplanned outages.
- Improved product quality associated with a reduction in costs related to losing or reprocessing product.
- Lower costs for system and equipment maintenance, spare parts inventory, and capital replacement.
- Enhanced morale among management and the hourly workforce as they learn to enjoy a proactive environment instead of surviving in chaos.
- Additional real capacity as operating units are able to operate at higher levels for sustained periods without excessive equipment failure.
- Higher profits from the compounded effect of reduced conversion costs and increased production levels.
CONCLUSION
Every region in the world is experiencing change and improving in its own way. Maintenance societies are also changing and playing bigger roles as educators and certification providers. However, in order to keep up with the transforming global market, societies will need to pull their resources together and develop a single certification program that will be accepted worldwide. Industry professionals can focus on these 10 improvement and change tips to help lead their organizations on the road to a successful asset management implementation.
- An organization must make a multiple-year commitment to improve and make it a priority.
- There must be continuous monitoring and the results evaluation.
- Senior leadership must support the initiative.
- All operators and crafts people must feel ownership of the initiative and understand the reason for it.
- The business case must challenge the company. It should be “overwhelming”.
- All functions cooperating fully in the initiative.
- There must be accountability for meeting monthly goals.
- Behaviors, attitudes and KPIs must be evaluated regularly.
- It must be one of the top three initiatives year after year.
- There can only be a single road map to success.
About the author:
Brad Peterson, CMRP, is the founder of Strategic Asset Management Inc. To learn more about this topic, e-mail Brad at bpeterson@samicorp.com or visit www.samicorp.com.
REFERENCES
James W. Davis, “Strategic planning for Asset Management”, 2004
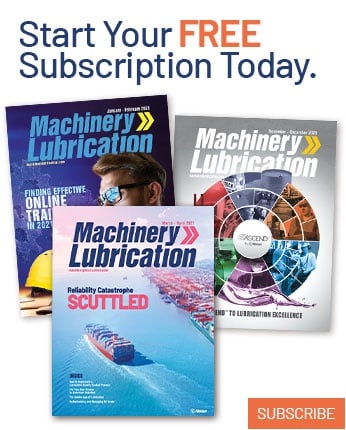